階梯軸加工工藝過程分析
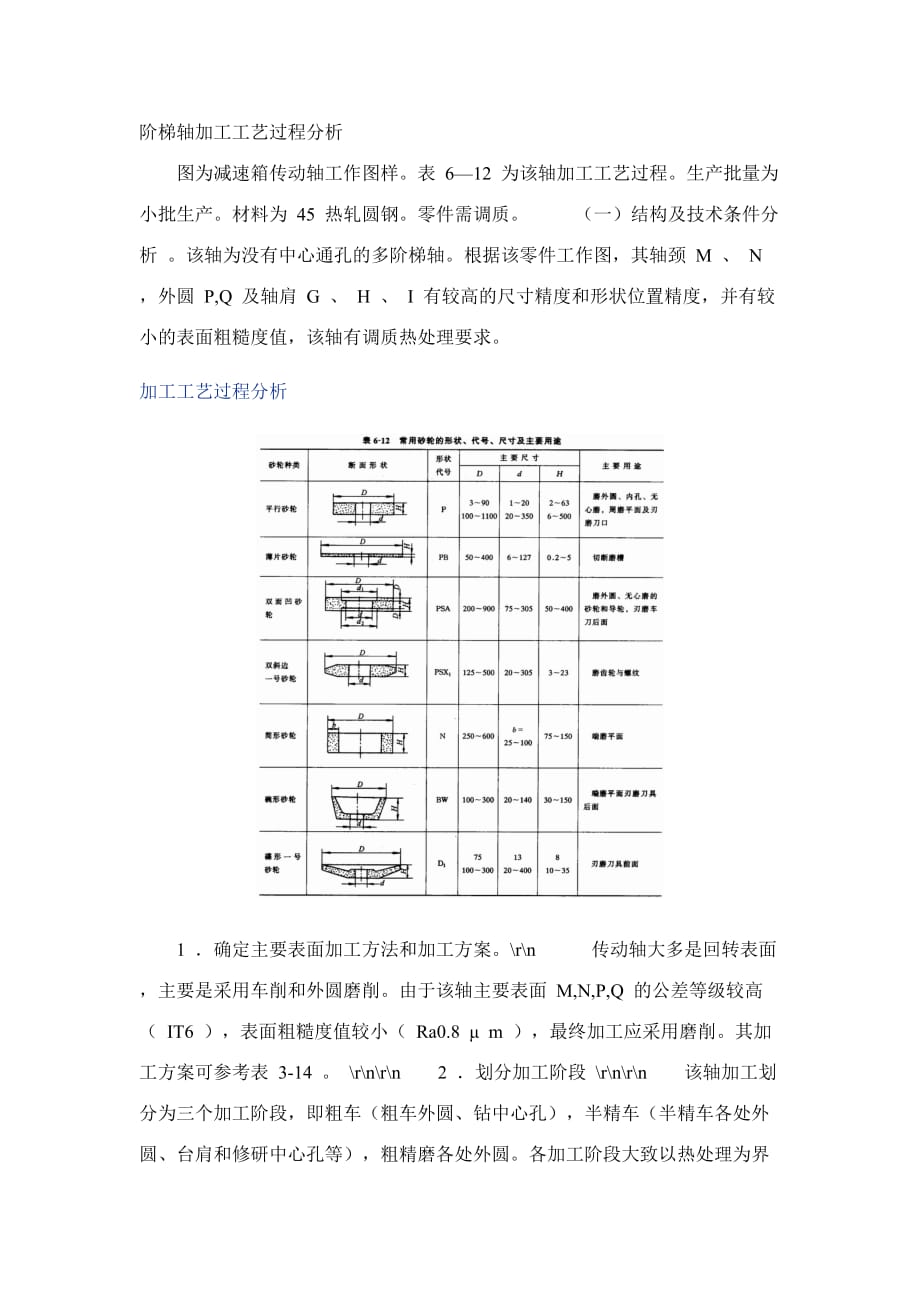


《階梯軸加工工藝過程分析》由會員分享,可在線閱讀,更多相關《階梯軸加工工藝過程分析(15頁珍藏版)》請在裝配圖網(wǎng)上搜索。
1、 階梯軸加工工藝過程分析 圖為減速箱傳動軸工作圖樣。表 6—12 為該軸加工工藝過程。生產(chǎn)批量為小批生產(chǎn)。材料為 45 熱軋圓鋼。零件需調(diào)質(zhì)。 ?。ㄒ唬┙Y(jié)構(gòu)及技術條件分析 。該軸為沒有中心通孔的多階梯軸。根據(jù)該零件工作圖,其軸頸 M 、 N ,外圓 P,Q 及軸肩 G 、 H 、 I 有較高的尺寸精度和形狀位置精度,并有較小的表面粗糙度值,該軸有調(diào)質(zhì)熱處理要求。 加工工藝過程分析 1 .確定主要表面加工方法和加工方案。\r\n 傳動軸大多是回轉(zhuǎn)表面,主要是采用車削和外圓磨削。由于該軸主要表面 M,N,P,Q 的公差等級較高( IT6 ),表面粗糙度值較?。?Ra
2、0.8 μ m ),最終加工應采用磨削。其加工方案可參考表 3-14 。 \r\n\r\n 2 .劃分加工階段 \r\n\r\n 該軸加工劃分為三個加工階段,即粗車(粗車外圓、鉆中心孔),半精車(半精車各處外圓、臺肩和修研中心孔等),粗精磨各處外圓。各加工階段大致以熱處理為界?! ? .選擇定位基準 \r\n\r\n 軸類零件的定位基面,最常用的是兩中心孔。因為軸類零件各外圓表面、螺紋表面的同軸度及端面對軸線的垂直度是相互位置精度的主要項目,而這些表面的設計基準一般都是軸的中心線,采用兩中心孔定位就能符合基準重合原則。而且由于多數(shù)工序都采用中心孔作為定位基面,能最大限度地加工出多個外圓和
3、端面,這也符合基準統(tǒng)一原則。 下列情況不能用兩中心孔作為定位基面 下列情況不能用兩中心孔作為定位基面: ( 1 )粗加工外圓時,為提高工件剛度,則采用軸外圓表面為定位基面,或以外圓和中心孔同作定位基面,即一夾一頂。 ( 2 )當軸為通孔零件時,在加工過程中,作為定位基面的中心孔因鉆出通孔而消失。為了在通孔加工后還能用中心孔作為定位基面,工藝上常采用三種方法。 ①當中心通孔直徑較小時,可直接在孔口倒出寬度不大于 2 mm 的 60 o 內(nèi)錐面來代替中心孔; ②當軸有圓柱孔時,可采用圖 6 — 36 a 所示的錐堵,取 1 ∶ 500 錐度;當軸孔錐度較小時,取錐堵錐度與工
4、件兩端定位孔錐度相同; ③當軸通孔的錐度較大時,可采用帶錐堵的心軸,簡稱錐堵心軸,如圖 6 — 36 b 所示。 使用錐堵或錐堵心軸時應注意,一般中途不得更換或拆卸,直到精加工完各處加工面,不再使 用中心孔時方能拆卸。 stool 愛軸承 打個招呼 秀才三級 3樓 復制 引用 熱處理工序的安排 發(fā)表于2006-04-17 10:12 該軸需進行調(diào)質(zhì)處理。它應放在粗加工后,半精加工前進行。如采用鍛件毛坯,必須首先安排退火或正火處理。該軸毛坯為熱軋鋼,可不必進行正火處理。 愛軸承 打個招呼 秀才三級 4樓 復制 引用
5、 加工順序安排 發(fā)表于2006-04-17 10:12 除了應遵循加工順序安排的一般原則,如先粗后精、先主后次等,還應注意: ?。?1 )外圓表面加工順序應為,先加工大直徑外圓 ,然后再加工小直徑外圓,以免一開始就降低了工件的剛度。 ( 2 )軸上的花鍵、鍵槽等表面的加工應在外圓精車或粗磨之后,精磨外圓之前。 軸上矩形花鍵的加工,通常采用銑削和磨削加工,產(chǎn)量大時常用花鍵滾刀在花鍵銑床上加工。以外徑定心的花鍵軸,通常只磨削外徑鍵側(cè),而內(nèi)徑銑出后不必進行磨削,但如經(jīng)過淬火而使花鍵扭曲變形過大時,也要對側(cè)面進行磨削加工。以內(nèi)徑定心的花鍵,其內(nèi)徑和鍵側(cè)均需進行磨削加工。 ?。?3
6、 )軸上的螺紋一般有較高的精度,如安排在局部淬火之前進行加工,則淬火后產(chǎn)生的變形會影響螺紋的精度。因此螺紋加工宜安排在工件局部淬火之后進行。 愛軸承 打個招呼 秀才三級 5樓 復制 引用 帶輪軸加工工藝過程分析 發(fā)表于2006-04-17 10:15 版主獎勵:30點 圖 6 — 37 為帶輪軸工作圖樣。帶輪軸中的主要技術條件有兩項:一為滲碳層深度,應控制在 1.2— 1.5 mm 范圍內(nèi);二為外圓¢ 22 f 7 需經(jīng)滲碳淬火,其硬度為 HRC58 ~ 63 。可以看出只有¢ 22 f 7 處需滲碳處理,其余部分均不可滲碳。零件上不需滲碳的部分,可用加
7、大余量待滲碳后車去滲碳層或在不需滲碳處涂防滲材料。加工余量應單面略大于滲碳深度,故右端直徑取¢ 25 mm ,單面去碳余量為 2.5 mm ,總長兩端也應放去滲碳余量各 3 mm 。在磨外圓前由于已經(jīng)過淬火工序,兩端中心孔在淬火時易產(chǎn)生氧化皮及變形,故增加一道研磨中心孔的工序。 愛軸承 打個招呼 秀才三級 6樓 復制 引用 表 6 — 13 為帶輪軸… 發(fā)表于2006-04-17 10:24 表 6 — 13 為帶輪軸的加工工藝過程 愛軸承 打個招呼 秀才三級 7樓 復制 引用 細長軸車削的工藝特
8、點 發(fā)表于2006-04-17 10:26 1 .細長軸剛性很差,車削時裝夾不當,很容易因切削力及重力的作用而發(fā)生彎曲變形,產(chǎn)生振動,從而影響加工精度和表面粗糙度。 2 .細長軸的熱擴散性能差,在切削熱作用下,會產(chǎn)生相當大的線膨脹。如果軸的兩端為固定支承,則工件會因伸長而頂彎。 3 .由于軸較長,一次走刀時間長,刀具磨損大,從而影響零件的幾何形狀精度。 4 .車細長軸時由于使用跟刀架,若支承工件的兩個支承塊對零件壓力不適當,會影響加工精度。若壓力過小或不接觸,就不起作用,不能提高零件的剛度;若壓力過大,零件被壓向車刀,切削深度增加,車出的直徑就小,當跟刀架繼續(xù)移動后,支承塊
9、支承在小直徑外圓處,支承塊與工件脫離,切削力使工件向外讓開,切削深度減小,車出的直徑變大,以后跟刀架又跟到大直徑圓上,又把工件壓向車刀,使車出的直徑變小,這樣連續(xù)有規(guī)律的變化,就會把細長的工件車成“竹節(jié)”形。 愛軸承 打個招呼 秀才三級 8樓 復制 引用 細長軸的先進車削法 —&m… 發(fā)表于2006-04-17 10:27 圖 6––38 為反向走刀車削法示意圖,這種方法的特點是: 1 .細長軸左端纏有一圈鋼絲,利用三爪自定心卡盤夾緊,減小接觸面積,使工件在卡盤內(nèi)能自由地調(diào)節(jié)其位置,避免夾緊時形成彎曲力矩,在切削過程中發(fā)生的變形也不會因卡
10、盤夾死而產(chǎn)生內(nèi)應力。 2 .尾座頂尖改成彈性頂尖,當工件因切削熱發(fā)生線膨脹伸長時,頂尖能自動后退,可避免熱膨脹引起的彎曲變形。 3 .采用三個支承塊跟刀架,以提高工件剛性和軸線的穩(wěn)定性,避免“竹節(jié)”形。 4 .改變走刀方向,使床鞍由主軸箱向尾座移動,使工件受拉,不易產(chǎn)生彈性彎曲變形。 愛軸承 打個招呼 秀才三級 9樓 復制 引用 外圓表面的加工方法和加工方案 發(fā)表于2006-04-17 10:40 版主獎勵:30點 案 \r\n 外圓表面是軸類零件的主要表面,因此要能合理地制訂軸類零件的機械加工工藝規(guī)程,首先應了解外圓表面的各種加工方法和加工方案。
11、本章主要介紹常用的幾種外圓加工方法和常用的外圓加工方案。 \r\n\r\n 一、外圓表面的車削加工 \r\n\r\n 根據(jù)毛坯的制造精度和工件最終加工要求,外圓車削一般可分為粗車、半精車、精車、精細車。 \r\n\r\n 粗車的目的是切去毛坯硬皮和大部分余量。加工后工件尺寸精度 IT11~IT13 ,表面粗糙度 Ra50~12.5 μ m 。 \r\n\r\n 半精車的尺寸精度可達 IT8~IT10 ,表面粗糙度 Ra6.3~3.2 μ m 。半精車可作為中等精度表面的終加工,也可作為磨削或精加工的預加工。 \r\n\r\n 精車后的尺寸精度可達 IT7~IT8 ,表面粗糙度 Ra1
12、.6~0.8 μ m 。 \r\n\r\n 精細車后的尺寸精度可達 IT6~IT7 ,表面粗糙度 Ra0.4~0.025 μ m 。精細車尤其適合于有色金屬加工,有色金屬一般不宜采用磨削,所以常用精細車代替磨削。 \r\n\r\n \r\n 愛軸承 打個招呼 秀才三級 10樓 復制 引用 圓表面的磨削加工 發(fā)表于2006-04-17 10:42 磨削是外圓表面精加工的主要方法之一。它既可加工淬硬后的表面,又可加工未經(jīng)淬火的表面。 根據(jù)磨削時工件定位方式的不同,外圓磨削可分為:中心磨削和無心磨削兩大類。 (一)中心磨削 中心磨削即普通的外圓磨
13、削,被磨削的工件由中心孔定位,在外圓磨床或萬能外圓磨床上加工。磨削后工件尺寸精度可達 IT6~IT8 ,表面粗糙度 Ra0.8~0.1 μ m 。按進給方式不同分為縱向進給磨削法和橫向進給磨削法。 1 .縱向進給磨削法(縱向磨法) 如圖 6-2 所示,砂輪高速旋轉(zhuǎn),工件裝在前后頂尖上,工件旋轉(zhuǎn)并和工作臺一起縱向往復運動。 2 .橫向進給磨削法(切入磨法) 如圖 6-3 所示,此種磨削法沒有縱向進給運動。當工件旋轉(zhuǎn)時,砂輪以慢速作連續(xù)的橫向進給運動。其生產(chǎn)率高,適用于大批量生產(chǎn),也能進行成形磨削。但橫向磨削力較大,磨削溫度高,要求機床、工件有足夠的剛度,故適合磨削短而粗,剛性好的
14、工件;加工精度低于縱向磨法。 愛軸承 打個招呼 秀才三級 11樓 復制 引用 無心磨削 發(fā)表于2006-04-17 10:43 版主獎勵:30點 \r\n\r\n 無心磨削是一種高生產(chǎn)率的精加工方法,以被磨削的外圓本身作為定位基準。目前無心磨削的方式主要有:貫穿法和切入法。 \r\n\r\n 如圖 6-4 所示為外圓貫穿磨法的原理。 \r\n\r\n 工件處于磨輪和導輪之間,下面用支承板支承。磨輪軸線水平放置,導輪軸線傾斜一個不大的 λ 角。這樣導輪的圓周速 \r\n\r\n度 υ 導 可以分解為帶動工件旋轉(zhuǎn)的 υ 工 和使工件軸向進給的分量 υ 縱
15、。 \r\n\r\n \r\n\r\n 如圖 6-5 為切入磨削法磨削的原理。導輪 3 帶動工件 2 旋轉(zhuǎn)并壓向磨輪 1 。加工時,工件和導輪及支承板一起向砂輪作橫向進給。磨削結(jié)束后,導輪后退,取下工件。導輪的軸線與砂輪的軸線平行或相交成很小的角度( 0.5~1 o ),此角度大小能使工件與擋鐵 4 (限制工件軸向位置)很好地貼住即可。 \r\n\r\n 愛軸承 打個招呼 秀才三級 12樓 復制 引用 無心磨削時,必須滿足下列條件 發(fā)表于2006-04-17 10:44 無心磨削時,必須滿足下列條件: 1 .由于導輪傾斜了一個 λ角度,為了保證切削平
16、穩(wěn),導輪與工件必須保持線接觸,為此導輪表面應修整成雙曲線回轉(zhuǎn)體形狀。 2 .導輪材料的摩擦系數(shù)應大于砂輪材料的磨擦系數(shù);砂輪與導輪同向旋轉(zhuǎn),且砂輪的速度應大于導輪的速度;支承板的傾斜方向應有助于工件緊貼在導輪上。 3 .為了保證工件的圓度要求,工件中心應高出砂輪和導輪中心連線。高出數(shù)值 H 與工件直徑有關。當工件直徑 d 工 =8 ~ 30mm 時, H ≈ d 工 /3 ;當 d 工 =30 ~ 70mm 時, H ≈ d 工 /4 。 4 、導輪傾斜一個 λ 角度。如圖 6-4 ,當導輪以速度 v 導 旋轉(zhuǎn)時,可分解為: v 工 =v 導 cos λ ; v 縱 =v 導
17、 sin λ 粗磨時, λ 取 3 ~ 6 ;精磨時, λ 取 1 ~ 3 。 無心磨削時,工件尺寸精度可達 IT6-IT7 ,表面粗糙度 Ra0.8-0.2um. 愛軸承 打個招呼 秀才三級 13樓 復制 引用 外圓磨削的質(zhì)量分析 發(fā)表于2006-04-17 10:45 版主獎勵:30點 在磨削過程中,由于有多種因素的影響,零件表面容易產(chǎn)生各種缺陷。常見的缺陷及解決措施分析如下: 1 .多角形 在零件表面沿母線方向存在一條條等距的直線痕跡,其深度小于 0.5 μ m ,如圖5-6 所示。 產(chǎn)生原因主要是由于砂輪與工
18、件沿徑向產(chǎn)生周期性振動所致。如砂輪或電動機不平衡;軸承剛性差或間隙 太大 ;工件中心孔與頂尖接觸不良;砂輪磨損不均勻等。消除振動的措施,如仔細地平衡砂輪和電動機;改善中心孔和頂尖的接觸情況;及時修整砂輪;調(diào)整軸承間隙等。 2 .螺旋形 磨削后的工件表面呈現(xiàn)一條很深的螺旋痕跡,痕跡的間距等于工件每轉(zhuǎn)的縱向進給量。如圖 6-7 所示。 產(chǎn)生原因主要是砂輪微刃的等高性破壞或砂輪與工件局部接觸。如砂輪母線與工件母線不平行;頭架、尾座剛性不等;砂輪主軸剛性差。消除的措施,修正砂輪,保持微刃等高性;調(diào)整軸承間隙;保持主軸的位置精度;砂輪兩邊修磨成能成臺肩形或倒圓角,使砂輪兩端不
19、參加切削;工件臺潤滑油要合適,同時應有卸載裝置;使導軌潤滑為低壓供油。 3 .拉毛(劃傷或劃痕) 常見的工件表面拉毛現(xiàn)象如圖 6-8 所示。 產(chǎn)生原因主要是磨粒自銳性過強;切削液不清潔;砂輪罩上磨屑落在砂輪與工件之間等。消除拉毛的措施,選擇硬度稍高一些的砂輪;砂輪修整后用切削液和毛刷清洗;對切削液進行過濾;清理砂輪罩上的磨屑等。 4 .燒傷 可分為螺旋形燒傷和點燒傷,如圖 6-9 所示。 燒傷的原因主要是由于磨削高溫的作用,使工件表層金相組織發(fā)生變化,因而使工件表面硬度發(fā)生明顯變化。消除燒傷的措施,降低砂輪硬度;減小磨削深度
20、;適當提高工件轉(zhuǎn)速;減少砂輪與工件接觸面積;及時修正砂輪;進行充分冷卻等。 愛軸承 打個招呼 秀才三級 14樓 復制 引用 外圓表面的精密加工 發(fā)表于2006-04-17 10:46 隨著科學技術的發(fā)展,對工件和加工精度和表面質(zhì)量要求也越來越高。因此在外圓表面精加工后,往往還要進行精密加工。外圓表面的精密加工方法常用的有高精度磨削、超精度加工、研磨和滾壓加工等。 高精度磨削 使軸的表面粗糙度值在 Ra0.16 μ m 以下的磨削工藝稱為高精度磨削,它包括精度磨削( Ra0.6-0.06 μ m )、超精密磨削( Ra0.04-0.02 μ m )
21、和鏡面磨削( Ra ﹤ 0.01 μ m)。 高精度磨削的實質(zhì)在于砂輪磨粒的作用。經(jīng)過精細修整后的砂輪的磨粒形成了同時能參加磨削的許多微刃。如圖 6 -10a,b,這些微刃等高程度好,參加磨削的切削刃數(shù)大大增加,能從工件上切下微細的切屑,形成粗糙度值較小的表面。隨著磨削過程的繼續(xù),銳利的微刃逐漸鈍化,如圖 6 -10c。鈍化的磨粒又可起拋光作用,使粗糙度進一步降低。 愛軸承 打個招呼 秀才三級 15樓 復制 引用 超精加工 發(fā)表于2006-04-17 10:47 版主獎勵:50點 \r\n\r\n 用細粒度磨具的油石對工件施加很小的壓力,油石作往復振動和慢
22、速沿工件軸向運動,以實現(xiàn)微量磨削的一種光整加工方法。 \r\n\r\n 如圖 6-11 所示為其加工原理圖。加工中有三種運動:工件低速回轉(zhuǎn)運動 1 ;磨頭軸向進給運動 2 ;磨頭高速往復振動 3 。如果暫不考慮磨頭軸向進給運動,磨粒在工件表面上走過的軌跡是正弦曲線,如圖 6-11b 所示。 \r\n \r\n\r\n 超精加工大致有四個階段: \r\n\r\n 1 .強烈切削階段 開始時,由于工件表面粗糙,少數(shù)凸峰與油石接觸,單位面積壓力很大,破壞了油膜,故切削作用強烈。 \r\n\r\n 2 .正常切削階段 當少數(shù)凸峰磨平后,接觸面積增加,單位面積壓力降低,致使切削作用減弱,進入正常
23、切削階段。 \r\n\r\n 3 .微弱切削階段 隨著接觸面積進一步增大,單位面積壓力更小,切削作用微弱,且細小的切屑形成氧化物而嵌入油石的空隙中,因而油石產(chǎn)生光滑表面,具有摩擦拋光作用。 \r\n\r\n 4 .自動停止切削階段 工件磨平,單位面積上的壓力很小,工件與油石之間形成液體摩擦油膜,不再接觸,切削作用停止。 \r\n\r\n 經(jīng)超精加工后的工件表面粗糙度值 Ra0.08-0.01 μ m. 。然而由于加工余量較小(小于 0.01mm ),因而只能去除工件表面的凸峰,對加工精度的提高不顯著。 \r\n\r\n 愛軸承 打個招呼 秀才三級 16樓 復制 引
24、用 研 磨 發(fā)表于2006-04-17 10:48 用研磨工具和研磨劑,從工件表面上研去一層極薄的表層的精密加工方法稱為研磨。 研磨用的研具采用比工件材料軟的材料(如鑄鐵、銅、巴氏合金及硬木等)制成。研磨時,部分磨粒懸浮在工件和研具之間,部分研粒嵌入研具表面,利用工件與研具的相對運動,磨粒應切掉一層很薄的金屬,主要切除上工序留下來的粗糙度凸峰。一般研磨的余量為 0.01 -0.02mm 。研磨除可獲得高的尺寸精度和小的表面粗糙度值外,也可提高工件表面形狀精度,但不能改善相互位置精度。 當兩個工件要求良好配合時,利用工件的相互研磨(對研)是一種有效的方法。如內(nèi)燃機中的氣閥與閥
25、座,油泵油咀中的偶件等。 愛軸承 打個招呼 秀才三級 17樓 復制 引用 滾壓加工 發(fā)表于2006-04-17 10:49 滾壓加工是用滾壓工具對金屬材質(zhì)的工件施加壓力,使其產(chǎn)生塑性變形,從而降低工件表面粗糙度,強化表面性能的加工方法。它是一種無切屑加工。 圖 6-12 為滾壓加工示意圖。滾壓加工有如下特點: 1 .滾壓前工件加工表面粗糙度值不大于 Ra5 μ m ,表面要求清潔,直徑余量為 0.02 -0.03mm 。 2 .滾壓后的形狀精度和位置精度主要取決于前道工序。 3 .滾壓的工件材料一般是塑性材料,并且材料組織要均勻。鑄鐵件一
26、般不適合滾壓加工。 4 .滾壓加工生產(chǎn)率高。 愛軸承 打個招呼 秀才三級 18樓 復制 引用 外圓表面加工方案的選擇 發(fā)表于2006-04-17 10:49 版主獎勵:30點 \r\n\r\n 上面介紹了外圓表面常用的幾種加工方法及其特點。零件上一些精度要求較高的面,僅用一種加工方法往往是達不到其規(guī)定的技術要求的。這些表面必須順序地進行粗加工、半精加工和精加工等加工方法以逐步提高其表面精度。不同加工方法有序的組合即為加工方案。表 3-14 即為外圓柱面的加工方案。 \r\n\r\n 確定某個表面的加工方案時,先由加工表面的技術要求(加工精度、表面粗糙度等
27、)確定最終加工方法,然后根據(jù)此種加工方法的特點確定前道工序的加工方法,如此類推。但由于獲得同一精度及表面粗糙度的加工方法可有若干種,實際選擇時還應結(jié)合零件的結(jié)構(gòu)、形狀、尺寸大小及材料和熱處理的要求全面考慮。 \r\n\r\n 表 3-14 中序號 3 (粗車—半精車—精車)與序號 5 (粗車—半精車—磨)的兩種加工方案能達到同樣的精度等級。但當加工表面需淬硬時,最終加工方法只能采用磨削。如加工表面未經(jīng)淬硬,則兩種加工方案均可采用。若零件材料為有色金屬,一般不宜采用磨削。 \r\n\r\n 再如表 3-14 中序號 7 (粗車—半精車—粗磨—精磨—超精加工)與序號 10 (粗車—半精車—粗磨—精磨—研磨)兩種加工方案也能達到同樣的加工精度。當表面配合精度要求比較高時,終加工方法采用研磨較合適;當只需要求較小的表面粗糙度值,則采用超精加工較合適。但不管采用研磨還超精加工,其對加工表面的形狀精度和位置精度改善均不顯著,所以前道工序應采用精磨,使加工表面的位置精度和幾何形狀精度已達到技術要求。
- 溫馨提示:
1: 本站所有資源如無特殊說明,都需要本地電腦安裝OFFICE2007和PDF閱讀器。圖紙軟件為CAD,CAXA,PROE,UG,SolidWorks等.壓縮文件請下載最新的WinRAR軟件解壓。
2: 本站的文檔不包含任何第三方提供的附件圖紙等,如果需要附件,請聯(lián)系上傳者。文件的所有權(quán)益歸上傳用戶所有。
3.本站RAR壓縮包中若帶圖紙,網(wǎng)頁內(nèi)容里面會有圖紙預覽,若沒有圖紙預覽就沒有圖紙。
4. 未經(jīng)權(quán)益所有人同意不得將文件中的內(nèi)容挪作商業(yè)或盈利用途。
5. 裝配圖網(wǎng)僅提供信息存儲空間,僅對用戶上傳內(nèi)容的表現(xiàn)方式做保護處理,對用戶上傳分享的文檔內(nèi)容本身不做任何修改或編輯,并不能對任何下載內(nèi)容負責。
6. 下載文件中如有侵權(quán)或不適當內(nèi)容,請與我們聯(lián)系,我們立即糾正。
7. 本站不保證下載資源的準確性、安全性和完整性, 同時也不承擔用戶因使用這些下載資源對自己和他人造成任何形式的傷害或損失。