機(jī)械設(shè)計(jì)畢業(yè)設(shè)計(jì)
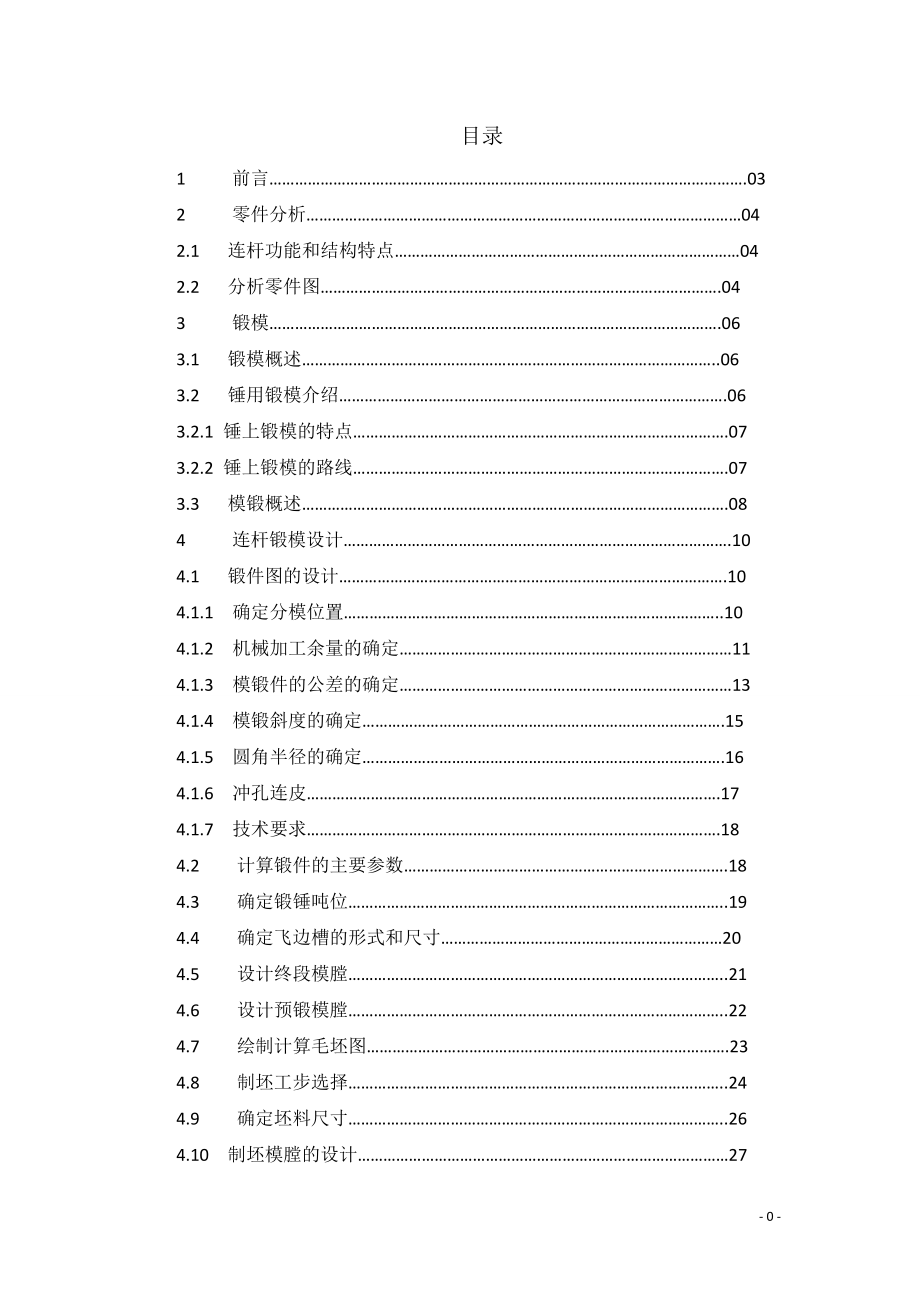


《機(jī)械設(shè)計(jì)畢業(yè)設(shè)計(jì)》由會員分享,可在線閱讀,更多相關(guān)《機(jī)械設(shè)計(jì)畢業(yè)設(shè)計(jì)(41頁珍藏版)》請?jiān)谘b配圖網(wǎng)上搜索。
1、 目錄 1 前言………………………………………………………………………………………………….03 2 零件分析…………………………………………………………………………………………04 2.1 連桿功能和結(jié)構(gòu)特點(diǎn)………………………………………………………………………04 2.2 分析零件圖………………………………………………………………………………….04 3 鍛模…………………………………………………………………………………………….06 3.1 鍛模概述……………………………………………………………………………………..06 3.2 錘
2、用鍛模介紹……………………………………………………………………………….06 3.2.1 錘上鍛模的特點(diǎn)…………………………………………………………………………….07 3.2.2 錘上鍛模的路線…………………………………………………………………………….07 3.3 模鍛概述……………………………………………………………………………………….08 4 連桿鍛模設(shè)計(jì)……………………………………………………………………………….10 4.1 鍛件圖的設(shè)計(jì)……………………………………………………………………………….10 4.1.1 確定分模位置……………………………
3、………………………………………………..10 4.1.2 機(jī)械加工余量的確定……………………………………………………………………11 4.1.3 模鍛件的公差的確定……………………………………………………………………13 4.1.4 模鍛斜度的確定………………………………………………………………………….15 4.1.5 圓角半徑的確定………………………………………………………………………….16 4.1.6 沖孔連皮…………………………………………………………………………………….17 4.1.7 技術(shù)要求…………………………………………………………………………………
4、….18 4.2 計(jì)算鍛件的主要參數(shù)………………………………………………………………….18 4.3 確定鍛錘噸位……………………………………………………………………………..19 4.4 確定飛邊槽的形式和尺寸…………………………………………………………20 4.5 設(shè)計(jì)終段模膛……………………………………………………………………………..21 4.6 設(shè)計(jì)預(yù)鍛模膛……………………………………………………………………………..22 4.7 繪制計(jì)算毛坯圖………………………………………………………………………….23 4.8 制坯工步選擇
5、……………………………………………………………………………..24 4.9 確定坯料尺寸……………………………………………………………………………..26 4.10 制坯模膛的設(shè)計(jì)……………………………………………………………………………27 4.11 模膛結(jié)構(gòu)設(shè)計(jì)……………………………………………………………………………..31 4.12 連桿模鍛流程……………………………………………………………………………..38 4.13 連桿圖……………………………………………………………………………..38 參考文獻(xiàn)……………………………………………………………
6、……………………..40 結(jié)束語………………………………………………………………………………………..41 第一章 前言 通過畢業(yè)設(shè)計(jì),使自己認(rèn)識到三年所學(xué)知識還遠(yuǎn)遠(yuǎn)不夠,而且實(shí)踐經(jīng)驗(yàn)幾乎為零,對于設(shè)計(jì)中的一些具體知識感到含糊,感到無從下手,一些自己認(rèn)為微不足道的東西往往有豐富的內(nèi)涵。在實(shí)習(xí)中,我們不知道向別人學(xué)些什么東西,而看到的東西和我們所學(xué)的有一定的差距,我們也不知道怎樣將學(xué)到的知識運(yùn)用到生產(chǎn)實(shí)踐中。 這次設(shè)計(jì)是對我們大學(xué)所學(xué)知識的綜合運(yùn)用,在老師的辛勤指導(dǎo)下,使我們漸漸能將理論知識運(yùn)用與實(shí)際生產(chǎn)中。這次設(shè)計(jì)為我們以后很快的
7、適應(yīng)新的工作環(huán)境打下了堅(jiān)實(shí)的基礎(chǔ),對我們即將進(jìn)入社會參加工作有重大意義,它使我們認(rèn)識到機(jī)械行業(yè)的廣闊前景,給我們投身機(jī)械研究和發(fā)展增加了信心和動(dòng)力。 在畢業(yè)設(shè)計(jì)中,在老師的辛勤指導(dǎo)下,進(jìn)行“連桿”的零件的鍛模設(shè)計(jì)。在此,對老師表示衷心的感謝!由于時(shí)間倉促,且我們的自身水平有限,設(shè)計(jì)中難免有一些錯(cuò)誤和不 足之處,敬請廣大老師和同學(xué)們批評、指正。 真心的感謝你們,我的老師 第二章 零件的分析 2.1連桿功能和結(jié)構(gòu)特點(diǎn) 連桿是汽車發(fā)動(dòng)機(jī)中的主要部件之一,其小頭經(jīng)活塞銷與活塞連接,大頭與曲軸連桿軸頸連接。燃燒室中受壓縮的油氣混合氣體經(jīng)
8、點(diǎn)火燃燒后急劇膨脹,以很大的壓力壓向活塞頂面,連桿則將活塞所受的力傳給曲軸,推動(dòng)曲軸旋轉(zhuǎn)。 連桿部件一般是由連桿體、連桿蓋和螺栓、螺母等所組成,如圖2.1所示。 圖2.1 連桿實(shí)體圖 在發(fā)動(dòng)機(jī)工作過程中,連桿要承受膨脹氣體交變壓力的作用和慣性力的作用,連桿除應(yīng)具有足夠的強(qiáng)度和剛度外,還應(yīng)盡量減小連桿自身的質(zhì)量,以減小慣性力的作用。連桿桿身一般都采用從大頭到小頭逐步變小的工字型截面形狀。 為了減少磨損和便于維修,在連桿小頭孔中壓入青銅襯套,大頭孔內(nèi)襯有具有鋼質(zhì)基底的耐磨巴氏合金軸瓦。 為了保證發(fā)動(dòng)機(jī)運(yùn)轉(zhuǎn)均衡,同一發(fā)動(dòng)機(jī)中各連桿的質(zhì)量不能相差太大,因此,在連桿部件的大、小頭兩端面設(shè)置
9、了去不平衡質(zhì)量的凸塊,以便在稱質(zhì)量后切除不平衡質(zhì)量。 連桿大、小頭兩端面對稱分布在連桿中截面的兩側(cè)??紤]到裝夾、安裝、搬運(yùn)等要求,連桿大、小頭的厚度相等(基本尺寸相同)。 在連桿小頭的頂端設(shè)有油孔(或油槽),發(fā)動(dòng)機(jī)工作時(shí),依靠曲軸的高速轉(zhuǎn)動(dòng),把氣缸體下部的潤滑油飛濺到小頭頂端的油孔內(nèi),以潤滑連桿小頭銅襯套與活塞銷之間的擺動(dòng)運(yùn)動(dòng)副。 2.2分析零件圖 連桿上需進(jìn)行機(jī)械加工的主要表面為:大、小頭孔及其兩端面,桿體與桿蓋的結(jié)合面及連桿螺栓定位孔等。仔細(xì)閱讀連桿的零件圖和相關(guān)資料得出連桿總成的主要技術(shù)要求如下: 2.2.1.為了使連桿大、小頭運(yùn)動(dòng)副之間配合良好,大頭孔的尺寸公差等級取為IT6
10、,表面粗糙度Ra應(yīng)不大于1.0;小頭孔的尺寸公差等級取為IT7,表面粗糙度Ra應(yīng)不大于2.0,對它們的圓柱度也相應(yīng)地規(guī)定了嚴(yán)格的要求。 2.2.2大、小頭孔的中心距影響到汽缸的壓縮比,進(jìn)而影響發(fā)動(dòng)機(jī)的效率,故兩孔中心距的尺寸公差等級應(yīng)不低于IT9(0.115mm)。大、小頭孔中心線在兩個(gè)相互垂直的方向上的平行度誤差會使活塞在汽缸中傾斜,致使汽缸磨損不均勻,縮短發(fā)動(dòng)機(jī)的壽命,同時(shí)也使曲軸的連桿軸頸磨損加劇。 3.連桿大頭孔兩端面對大頭孔中心線的垂直度誤差過大,將加劇連桿大頭兩端面與曲軸連桿軸頸兩端面之間的磨損,甚至引起燒傷,一般規(guī)定垂直度公差等級應(yīng)不低于9級(0.062mm)。 4.連桿大
11、小頭兩端面間距離的基本尺寸相同,但是其技術(shù)要求是不同的。大頭兩端面間尺寸公差等級為IT9,表面粗糙度Ra部大于3.2;小頭兩端面間的尺寸公差等級為IT12,表面粗糙度Ra不大于6.3。這是因?yàn)檫B桿大頭兩端面與曲軸連桿軸頸兩軸肩端面間有配合要求,而連桿小頭兩端面與活塞銷孔座內(nèi)檔之間沒有配合要求。連桿大頭兩端面間距離尺寸的公差帶正好落在連桿小頭端面間距離尺寸的公差帶中,這給連桿的加工帶來許多方便。 5.為了保證發(fā)動(dòng)機(jī)運(yùn)轉(zhuǎn)平穩(wěn),對連桿小頭(約占連桿全長2/3)質(zhì)量差和小頭(約占連桿全長1/3)質(zhì)量差分別給以嚴(yán)格的規(guī)定。 第三章 鍛模 3.1鍛模概述 鍛壓加
12、工是機(jī)械制造工業(yè)的一個(gè)重要加工方式,它的加工特點(diǎn)是坯料經(jīng)過加熱,在錘鍛或壓力機(jī)等鍛壓設(shè)備及模具的動(dòng)力作用下,坯料內(nèi)部的應(yīng)力狀態(tài)達(dá)到一定的條件后,引起形狀改變?yōu)樽罱K形狀的鍛件。由于鍛件的內(nèi)部組織與機(jī)械性能較好,因此一般承載力件多選用鍛壓方法進(jìn)行生產(chǎn)。而鍛模是金屬在熱態(tài)和冷態(tài)下進(jìn)行體積成形(鍛壓)時(shí)所用模具的統(tǒng)稱。根據(jù)不同的情況,鍛模的分類也有多種: 1)按鍛造設(shè)備不同,鍛模可以分為錘用鍛模、螺旋壓力機(jī)用鍛模、熱模鍛壓力機(jī)用鍛模、平鍛機(jī)用鍛模、水壓機(jī)用鍛模、輥鍛機(jī)用鍛模、高速錘用鍛模、擺輾機(jī)用鍛模等等,這種分類方法主要考慮了各種鍛壓設(shè)備的工作特點(diǎn)、結(jié)構(gòu)特點(diǎn)和工藝特點(diǎn),因此決定了鍛模的結(jié)構(gòu)和使用條
13、件有所不同。 2)按工藝用途不同,鍛??梢苑譃殄懺炷>摺D壓模具、輥鍛模具、冷鐓模具、校正模具、壓印模具、精整模具、精鍛模具、切邊模具、沖孔模具等等。這種方法主要考慮不同變形工序的規(guī)律,因此各類鍛模的模膛設(shè)計(jì)和模鍛結(jié)構(gòu)也有所不同。 3)其它的分類方法,如按鍛模的結(jié)構(gòu)不同分為整體模和組合鑲塊鍛模;按終鍛模膛結(jié)構(gòu)不同可分為開式鍛模和閉式鍛模;按分模面的數(shù)量不同分為單個(gè)分模面鍛模和多向分模面鍛模等。 目前由于國內(nèi)連桿生產(chǎn)企業(yè)在規(guī)模和技術(shù)先進(jìn)程度存在著差異,因此連桿生產(chǎn)所采用的鍛造工藝也就有所不同。錘用鍛模主要用于鍛件的大量生產(chǎn),是鍛造生產(chǎn)中最基本的鍛造方法。由于模鍛錘具有通用性較強(qiáng),生產(chǎn)效率高
14、等優(yōu)點(diǎn),因此錘用鍛模也是鍛造生產(chǎn)中應(yīng)用最廣的鍛造方法之一。本課題也是就錘用鍛模作為研究對象,來設(shè)計(jì)連桿的錘用鍛模。 3.2 錘用鍛模介紹 錘用鍛模主要用于鍛件的大量生產(chǎn),是鍛造生產(chǎn)中最基本的鍛造方法。由于模鍛錘具有通用性較強(qiáng),生產(chǎn)效率高優(yōu)點(diǎn),因此錘用鍛模也是鍛造生產(chǎn)中應(yīng)用最廣的鍛造方法之一。 3.2.1 錘上鍛模的特點(diǎn) 模鍛錘與鍛壓機(jī)等相比較主要有下列工作特點(diǎn): 1)靠沖壓力使金屬變形,錘頭在行程的最后的、速度約為7-9m/s; 2)受力系統(tǒng)不是封閉的,沖擊力通過下帖傳給基礎(chǔ); 3)單位時(shí)間內(nèi)的打擊次數(shù)多(1-10t模鍛錘為100-400次/min); 4)錘頭的行程不固定
15、; 5)承受偏載的能力和導(dǎo)向精度較差; 6)無頂出裝置。 根據(jù)模鍛錘的工作特點(diǎn),其模鍛工藝和模具設(shè)計(jì)具有下列特點(diǎn): 1)金屬在各模膛中的變形是在錘頭的多次打擊下逐步完成的,錘頭的打擊速度雖然較快,但是在打擊中每一次的變形量較?。? 2)由于靠沖擊力使金屬變形,可以利用金屬的流動(dòng)慣性,有利于金屬充滿模膛。鍛件上難充滿的部分應(yīng)盡量放在上模; 3)在錘上可實(shí)現(xiàn)多種模鍛工步,特別是對長軸類鍛件進(jìn)行滾壓、拔長等制坯工步非常方便。 4)由于模鍛錘的導(dǎo)向精度不太高,工作時(shí)的沖擊性質(zhì)和錘頭行程不固定等,因此,模鍛件的尺寸精度不太高; 5)由于無頂出裝置,鍛模起模較困難,模鍛斜度應(yīng)適當(dāng)大些; 6
16、)由于靠沖擊力使金屬變形,模具一般用用整體結(jié)構(gòu); 7)由于靠沖擊力使金屬變形和錘頭行程速度快,通常采用鎖扣裝置導(dǎo)向,較少采用導(dǎo)柱導(dǎo)套。 模鍛錘工作時(shí)振動(dòng)、噪音大,勞動(dòng)條件差,對車間設(shè)備和廠房帶來有害的影響;另外,模鍛錘需要較重的砧座(約為落下部分質(zhì)量的25倍),尤其對大噸位的模鍛錘,制造、運(yùn)輸和安裝都很困難。因此,近幾十年來,16t以上的模鍛錘逐漸地被其他鍛壓設(shè)備所代替。 3.2.2 錘上鍛模的路線 為了得到合格的鍛件所進(jìn)行的全套路線,一般情況下包括下列工序: 1)下料 將原材料切割成所需尺寸的坯料; 2)加熱 為了提高金屬的塑性、降低變形抗力,便于模鍛成形; 3)模鍛
17、 得到鍛件的形狀和尺寸; 4)切邊或沖孔 切去飛邊或者沖孔連皮; 5)熱校正或熱精壓 使鍛件形狀和尺寸準(zhǔn)確; 6)在砂輪上磨毛刺 (切邊所剩的毛刺); 7)熱處理 保證合適的硬度和合格的機(jī)械性能,常用的方法是正火和調(diào)質(zhì); 8)清除氧化皮 得到表面光潔的鍛件。常用的方法有噴砂、噴丸、滾筒拋光、酸洗; 9)冷校正或冷精壓 進(jìn)一步提高鍛件的精度,減小表面粗糙度; 10)檢驗(yàn)鍛件質(zhì)量。 3.3模鍛概述 模鍛工藝是金屬毛坯在外力作用下發(fā)生變形充滿模膛,獲得所需形狀、尺寸并具有一定機(jī)械性能的模鍛件的鍛造生產(chǎn)工藝。 根據(jù)模鍛時(shí)鍛件是否形成橫向飛邊,模鍛工藝可分為
18、兩種: 1)有飛邊模鍛 即開式模鍛,如圖3.1a所示。分模面與模具運(yùn)動(dòng)方向垂直,在模鍛過程中分模面之間的距離逐漸減小,沿分模面形成橫向飛邊,依靠飛邊的阻力使金屬充滿模膛。其特點(diǎn)是鍛件周圍沿分模面形成橫向飛邊。 2)無飛邊模鍛 即閉式模鍛,如圖3.1b所示。分模面與模具運(yùn)動(dòng)方向平行,在模鍛過程中分模面之間的間隙保持不變,不形成飛邊。如果毛坯體積過多,則在模膛充滿后出現(xiàn)少量的縱向毛刺。 圖3.1 a)開式模鍛簡圖 圖3.1 b)閉式模鍛簡圖 根據(jù)金屬毛坯的溫度不同,模鍛工藝可以分為三種: 1)熱模鍛 將金屬毛坯加熱至再結(jié)晶溫度以上時(shí)進(jìn)行模鍛
19、。 2)溫模鍛 將金屬毛坯加熱至金屬再結(jié)晶溫度以下某個(gè)適當(dāng)?shù)臏囟确秶鷥?nèi)進(jìn)行模鍛。 3)冷漠段 在室溫中對金屬毛坯進(jìn)行模鍛 第四章 連桿鍛模的設(shè)計(jì) 4.1 鍛件圖的設(shè)計(jì) 鍛件圖是根據(jù)零件產(chǎn)品圖制定的,它全面地反應(yīng)鍛件的情況。在鍛件圖中要規(guī)定:鍛件公差和機(jī)械加工余量;鍛件的材質(zhì)及熱處理要求;鍛件的清理方式及其他技術(shù)條件內(nèi)容。鍛件圖是編制鍛造工藝卡片、設(shè)計(jì)模和量具以及最后檢驗(yàn)鍛件的依據(jù),也是機(jī)械加工部門驗(yàn)收鍛件,制定切削加工工藝,設(shè)計(jì)加工夾具(用毛坯面定位時(shí))依據(jù),所以鍛件圖是最重要的基本工藝文件之一。設(shè)計(jì)鍛件圖時(shí)必須綜合考慮鍛件的生產(chǎn)批量,設(shè)備工藝條件等各種因素。鍛件圖的設(shè)計(jì)
20、還必須與機(jī)械加工工藝人員協(xié)商并認(rèn)可。 4.1.1 確定分模位置 分模面選擇的基本要求是能保證鍛件從模膛中取出來,因此鍛件的側(cè)面不能有凹的形狀。此外,還要考慮以下因素: 1)保證鍛件容易脫模,一般應(yīng)以最大投影面作為分模面 ,見圖4.1a ; 2)易于檢查上下模膛的相對錯(cuò)移,見圖4.1b; 3)分模線盡可能選直線,使鍛模加工簡單,見圖4.1c;但是對頭部尺寸較大,且上下不對稱的鍛件,則易取折線分模,以保證成形充滿,見圖4.1d; 4)對圓餅類鍛件,當(dāng)H≦D時(shí),宜取徑向分模,而不取軸向分模,見圖4.2e; 5)應(yīng)保證鍛件有合理的金屬流線分布,見圖4.1f; 6)盡量在高度的一
21、半處分模,使鍛件機(jī)械加工余量最小,有利于節(jié)約材料; 7)要使模膛的寬帶大而深度小,這樣金屬容易充滿模膛,鍛件容易出模。 圖4.1不正確與正確的分模面簡圖 綜上分析,再結(jié)合連桿自身的特點(diǎn),分模面選擇在其上下對稱位置,見圖4.1為其示意圖。 圖4.2 分模面位置 4.1.2 機(jī)械加工余量的確定 機(jī)械加工余量的確定于鍛件形狀的復(fù)雜程度、成品零件的精度要求、鍛件的材質(zhì)、模鍛設(shè)備、工藝條件、熱處理的變形量、矯正的難易程度、機(jī)械加工的工序設(shè)計(jì)等許多因素有關(guān),不能籠統(tǒng)地說多大的余量最合適。機(jī)械加工余量也并不是越小越好,為了將鍛件的脫碳層(約0.5mm)和表面的細(xì)小裂紋去掉,留有一定
22、的加工余量是必要的。GB/T 12362-1990規(guī)定的機(jī)械加工余量,根據(jù)估算鍛件質(zhì)量、加工精度及鍛件復(fù)雜系數(shù)查表得到。 (1)鍛件質(zhì)量 估算連桿鍛件的質(zhì)量約為1.5kg,連桿材料為40鋼。 (2)材質(zhì)系數(shù) 鍛件的材質(zhì)系數(shù)分為兩類,即分為和兩級。 是鋼的最高含碳量小于0.65%的碳鋼或合金元素最高總含量小于3.0%的合金鋼。 是鋼的最高含碳量大于或等于0.65%的碳鋼或者合金元素最高總含量大于或等于3.0%的合金。詳見表4.3。 表4.3 鍛件材質(zhì)系數(shù) 級別 鋼的最高含碳量 合金鋼的合金元素最高含量 <0.65% <3.0% ≤0.65% ≥3.0% 4
23、0鋼顯然屬于M1類。 (3)鍛件形狀復(fù)雜系數(shù)S 式中 ; 對于本課題 鍛件形狀復(fù)雜系數(shù)S分級見表4.4。 注:當(dāng)鍛件為薄形圓盤或法蘭件,其厚度與直徑之比≤0.2時(shí),直接確定為復(fù)雜等級。其結(jié)果為S3級。 表4.4 鍛件形狀復(fù)雜系數(shù)S分級表 級別 S數(shù)值范圍 級別 S數(shù)值范圍 簡單 >0.63-1.00 較復(fù)雜 >0.16-0.32 一般 >0.32-0.63 復(fù)雜 ≤0.16 有零件圖中連桿的表面粗糙度可知連桿需要磨削加工,即加工精度為,根據(jù)鍛件質(zhì)量、材質(zhì)系數(shù)、鍛件形狀復(fù)雜系數(shù)和相應(yīng)部位的尺寸查表得: 在厚度方向的單邊加
24、工余量為1.7-2.2mm; 在水平方向的單邊加工余量為 1.7-2.2mm。 故統(tǒng)一取2.0mm。 連桿小頭的孔不不鍛造出來,大頭內(nèi)孔的機(jī)械加工余量參考4.5表 表4.5 鍛件內(nèi)孔的單面機(jī)械加工余量 (摘自GB/T 12362-1990) (mm) 孔徑 孔深 大于 到 大于0 63 100 140 200 至63 100 140 200 280 - 25 2.5 - - - - 25 40 2.0 2.6 - - - 40 63 2.0 2.6 3.0 - - 63 100 2.5 3.0 3.0 4
25、.0 - 100 160 2.6 3.0 3.4 4.0 4.6 160 250 3.0 3.0 3.4 4.0 4.6 由連桿大頭的尺寸確定單邊機(jī)械加工余量為2.5mm。 4.1.3 模鍛件的公差的確定 模鍛件公差代表模鍛件要求達(dá)到的精度。就尺寸公差而言,是鍛件公稱尺寸所允許的增大值叫做正偏差;對公稱尺寸所允許的減小值叫做負(fù)偏差。鍛件公稱尺寸,公差和余量之間的關(guān)系如圖4.6所示。 圖4.6 鍛件的公稱尺寸、公差和余量 (1)長度、寬度和高度尺寸公差 指在分模線一側(cè)同一塊模具上沿長度l、寬度b、高度h方向上的尺寸公差,此類公差根據(jù)鍛件的基本尺寸
26、、質(zhì)量、形狀復(fù)雜系數(shù)及材質(zhì)系數(shù)查[7]表15-18 查得為: 長度極限偏差為 寬度極限偏差為 高度極限偏差為 在大量生產(chǎn)的條件下,連桿鍛件在機(jī)械加工時(shí)用大小頭端面定位,要求大小頭端面在同一平面上的精度較高,100mm內(nèi)為0.6mm,而模鍛后的高度公差較大,達(dá)不到上述要求,故鍛件在熱處理、清理后增加一道壓?。ㄆ矫胬渚珘海┕ば颉e懠?jīng)壓印后,機(jī)械加工余量可大大減小,取0.75mm,壓印后的鍛件高度公差取0.2mm。連桿鍛件壓印后,大小頭高度尺寸為(38.5+20.75)mm=40mm,單邊壓印余量取0.25mm,同時(shí)模鍛后大小頭部的高度尺寸為(40+)mm=40.5mm。
27、 由于壓印需要余量,如鍛件高度偏差為負(fù)值時(shí)(-0.6),則實(shí)際單邊壓印余量僅為0.15mm,為保證適當(dāng)?shù)膲河∮嗔?,鍛件高度極限偏差調(diào)整為,由于壓印后鍛件水平方向的尺寸稍有增加,故在水平方向的余量可以適當(dāng)減小,把加上余量為103mm的寬度改為109mm等。 (2)厚度尺寸公差 指跨越分模線的厚度尺寸的公差。鍛件所有厚度尺寸去同一公差,其數(shù)值根據(jù)鍛件最大厚度尺寸為: 厚度尺寸公差為。 由于連桿鍛件的分模線是一直線,比較厚度和高度的尺寸公差發(fā)現(xiàn)公差帶值相等,只是上下偏差分布有0.1mm的差入。故厚度的和高度的統(tǒng)一起來與高度尺寸公差一樣。 (3)錯(cuò)位公差和殘留飛邊公差 錯(cuò)位是鍛件在分
28、模線上、下兩部分對應(yīng)點(diǎn)所偏移的距離(圖4.7),數(shù)值為或其中為平行于分模線最大、最小投影長度,為平行于分模線最大、最小投影寬度。 圖4.7 模鍛件的錯(cuò)差簡圖 由質(zhì)量約為1.5kg和分模線對稱得: 連桿鍛件的錯(cuò)位公差為0.6mm。 連桿鍛件的橫向殘留飛邊公差為0.7mm。 (4)允許的表面缺陷深度 對于加工表面,最大深度不超過余量的一半;對于非加工表面,其最大深度不超過最大厚度公差的三分之一。故取鍛件的允許表面缺陷深度為0.5mm。 4.1.4 模鍛斜度的確定 為了便于將成形后的鍛件從模膛中取出,在鍛件上與分模面相互垂直的平面上必要加上一定斜度的余料,這個(gè)斜度就是模
29、鍛斜度。鍛件外壁的斜度成為外模鍛斜度如圖4.8,鍛件內(nèi)壁的斜度稱為內(nèi)模鍛斜度。鍛件成形后,隨著溫度的下降,外膜鍛斜度上的金屬由于收縮而有助于鍛件出模,內(nèi)模鍛斜度的金屬由于收縮反而將模膛的突起部分夾得更緊。所以同一鍛件上內(nèi)模鍛斜度比外模鍛斜度大。 很明顯,加上模鍛斜度后會增加金屬耗材和機(jī)加工工時(shí)。因此應(yīng)盡量選用較小的鍛模斜度,同時(shí)要注意充分利用鍛件的固有斜度。模鍛斜度與模膛內(nèi)壁斜度相對應(yīng)。模膛內(nèi)壁斜度系用指狀標(biāo)準(zhǔn)銑刀加工而成,所以模鍛斜度應(yīng)該選用,,,,標(biāo)準(zhǔn)度數(shù),以便與銑刀規(guī)格一致。為了減少銑削加工的換刀次數(shù),可選用內(nèi)外模鍛斜度為同一數(shù)值。同時(shí)和零件圖
30、的模鍛斜度保持一致,故選模鍛斜度為。 圖4.8 4.1.5 圓角半徑的確定 鍛件上凸起和凹下的部分均應(yīng)帶有圓角,不允許出現(xiàn)銳角。如圖4-4所示。 凸圓角的作用是避免鍛模在熱處理時(shí)和模鍛過程中因?yàn)閼?yīng)力集中導(dǎo)致開裂,也使金屬易于充滿相應(yīng)的部位。凹圓角的作用是使金屬易于流動(dòng),防止模鍛件產(chǎn)生折疊,防止模膛過早磨損和被壓塌。生產(chǎn)上吧模鍛件的凸圓角稱為外圓角半徑r,凹圓角半徑稱為內(nèi)圓角半徑R(圖4.8)。適當(dāng)加大圓角半徑,對防止鍛件轉(zhuǎn)角處的流線被切斷、提高模鍛件品質(zhì)和模具壽命有利。然而,增加外圓角半徑r將會減少相應(yīng)部位的機(jī)加工余量,增加內(nèi)圓角半徑R,將會加大
31、相應(yīng)部位的機(jī)加工余量,增加材料損耗。對某些復(fù)雜鍛件,內(nèi)圓角半徑R過大,也會使金屬過早流 失造成局部充不滿現(xiàn)象。為保證鍛件外圓角處的最小機(jī)加工余量: 式中 —零件相應(yīng)處的圓角半徑或倒角值; 如無倒角: 為了適應(yīng)制造模具所用刀具的標(biāo)準(zhǔn)化,可按下列序列值設(shè)計(jì)圓角半徑(mm):1.0,1.5,2.5,3.0,4.0,5.0,6.0,8.0,10.0,12.0,15.0。當(dāng)圓角半徑大于15mm后,按以5mm為遞增值生成序列選取。在同一鍛件上選定的圓角半徑規(guī)格應(yīng)該
32、盡量一致,不宜過多。 本鍛件高度余量:(0.75+0.4)mm=1.15mm, 則連桿鍛件需要倒角的叉內(nèi)圓角半徑:(1.15+2)=3.15mm,取3.0mm。 其余部位的圓角半徑取1.5mm。 4.1.6 沖孔連皮 具有通孔的零件,在模鍛是不能直接鍛出通孔。所鍛成的盲孔內(nèi)留一層具有一定厚度的金屬層,稱為沖孔連皮。沖孔連皮可利用切邊機(jī)切除。 模鍛時(shí)鍛出盲孔是為了使鍛件更接近零件形狀,減少金屬消耗、縮短機(jī)加工工時(shí)。連皮的厚度s要適當(dāng),過薄易發(fā)生鍛不足,而且容易導(dǎo)致模膛凸起部分打塌;過厚切除連皮困難,而且浪費(fèi)金屬。一般情況下,當(dāng)鍛件內(nèi)孔直徑小于30mm,孔可以不鍛出。當(dāng)鍛件內(nèi)孔直徑大于
33、30mm,可考慮沖孔,要合理設(shè)計(jì)沖孔連皮的形狀和尺寸。 當(dāng)鍛件內(nèi)孔直徑較小,如連桿小頭的內(nèi)孔,不易鍛出連皮應(yīng)該為壓凹形式,如圖4.9所示。其目的不在于節(jié)省金屬,而是通過壓凹變形有助于小頭部分飽滿成形。 圖4.9 鍛件壓凹 4.1.7 技術(shù)要求 (1)鍛件圖上未標(biāo)注的模鍛斜度為。 (2)鍛件圖上未標(biāo)注的圓角半徑R1.5。 (3)允許的錯(cuò)差量為0.6mm。 (4)允許的殘留飛邊量0.7mm。 (5)允許的便面缺陷深度0.5mm。 (6)鍛件熱處理為:調(diào)質(zhì)。 (7)鍛件表面的清理:為了便于檢查淬火裂紋,系用酸洗。 上述各參數(shù)確定后,便可以繪出制模鍛件圖。帶連皮的模鍛件,不
34、需要繪出連皮的形狀和尺寸。 4.2 計(jì)算鍛件的主要參數(shù) (1)鍛件在平面圖上的投影面積為9630。 連桿小頭為圓形: ≈2060 連桿大頭為半環(huán)形:= ≈2000.2 中間桿部:+-- ≈5570.2 S==9630.4 (2)鍛件周邊長度為:1104mm。 C=2=2() ≈1104mm
35、 (3)鍛件體積為:220326 ≈sh=h=40.5+19525=81856.25 =-0.53240.5 ≈67324 = ≈24635.7 = ≈43106 ≈3404.25 ≈+=220326 (4)鍛件質(zhì)量為:1.73kg M= =7.85220326 ≈1.729(kg ) 取1.73kg 4.3確定鍛錘噸位 總變形面積為鍛件在平面上的投影面積與飛邊面積之和,參考表4-3,按12t錘飛邊槽尺寸考慮,假定飛邊平均寬度為23mm。總變形面積: A=(9630+110423)=35022 因生產(chǎn)中要求搞
36、生產(chǎn)率,按確定噸位的經(jīng)驗(yàn)公式: G=6.3KA 式中 G—錘落下部分質(zhì)量(kg); A—鍛件和飛邊(按倉部的0.5計(jì)算)在水平面上的投影() K—材質(zhì)系數(shù),取1.0 G=6.3KA=6.31.035022kg=2206.4kg≈3000kg 故選用3t鍛錘。 表4.10 飛邊槽尺寸與鍛錘噸位的關(guān)系() 錘噸位 備注 1t夾板錘 0.6 3 8 20 1.5 1t模鍛錘 1-1.6 4 8 25 1.5 齒輪鎖扣=30 1.5t模鍛錘 1.6-2 4
37、8 25-30 2 2t模鍛錘 2 4 10 30-40 2.5 齒輪鎖扣=40 3t模鍛錘 3 5 12 30-40 3 齒輪鎖扣=45 5t模鍛錘 3 26 26 50 3 齒輪鎖扣=55 10t模鍛錘 5 36 16 50 3 4.4 確定飛邊槽的形式和尺寸 錘上模鍛為開式模鍛,一般終鍛模膛周圍必須有飛邊槽,其主要作用是增加金屬流出模膛的阻力,迫使金屬充滿模膛。飛邊還可容納多余金屬。鍛造時(shí)飛邊起到緩沖作用,減弱上模對下模的打擊,使模具不易壓塌和開裂。此外飛邊處厚度較薄,便于切除。飛邊槽一般由橋口和倉部組成。 (1)
38、飛邊槽形式的選擇 連桿鍛件質(zhì)量為1.73kg,質(zhì)量不大,而且形狀上下對稱,還不太復(fù)雜,故選用標(biāo)準(zhǔn)形見圖4.11,其優(yōu)點(diǎn)是橋口在上模,模鍛時(shí)受熱時(shí)間短,溫開較低,橋口不易壓塌和磨損。 圖4.11飛邊槽的結(jié)構(gòu)形式 (2)飛邊槽的尺寸確定 設(shè)計(jì)錘上飛邊槽尺寸有兩種方法: ①噸位法。鍛件的尺寸即是選擇噸位的依據(jù),也是選擇飛邊槽尺寸的主要依據(jù)。生產(chǎn)中通常按設(shè)備噸位來選定飛邊槽尺寸,如表4.10所列。 ②計(jì)算法。利用經(jīng)驗(yàn)公式計(jì)算橋口高度后根據(jù)表4.4確定其他相關(guān)尺寸。 式中 S—鍛件在分模面上的投影面積()。
39、 由表4.4可以看出飛邊槽的尺寸選用3t中的下限。即: =3mm =30mm B=12mm =5mm R=3mm 飛邊斷面積: =()+bh-()2 = 30(5+1.5)+123-(25-0.253.14) =220.25220() 因桿部斷面積太小,考慮到拔長難以達(dá)到最小斷面積,需增大飛邊槽倉部寬度;大頭部分叉口較寬分料困難,流入飛邊槽的金屬較少,將該處減小到20。使模膛安排緊張,且增加承擊面積。 鍛件飛邊平均斷面積為: =0.7=0.7220=154 飛邊體積: =1104154=170
40、016 4.5 設(shè)計(jì)終段模膛 終鍛模膛是鍛件最后成形的模膛,通過它獲得帶飛邊的鍛件。終鍛模膛是按照熱鍛件圖制造的,模膛設(shè)計(jì)的主要內(nèi)容是繪制熱鍛圖和確定飛邊槽尺寸。 考慮金屬的熱脹冷縮,熱鍛件圖上的尺寸應(yīng)比鍛件圖的相應(yīng)尺寸有所放大。終鍛溫度下的收縮率為普通鋼:1.2%-1.5%;連桿熱鍛件圖考慮1.5%冷縮率。根據(jù)生產(chǎn)中的經(jīng)驗(yàn)總結(jié),考慮到鍛模使用后承擊面下陷,模膛深度減小及精壓是變形不均,橫向尺寸增大等因素,需要修改幾處尺寸:連桿小頭高度40.5處,理論上應(yīng)為41,實(shí)際取為41.5;大頭和小頭一樣;小頭50應(yīng)為50.6,而實(shí)際仍為50等。繪制的熱鍛件圖見鍛件圖。 4.6 設(shè)計(jì)預(yù)鍛模膛
41、 帶工字形截面的鍛件以兩桿為其代表。鍛件大部分表面不經(jīng)過機(jī)械加工。質(zhì)量要求嚴(yán)格,不允許有折疊,成品連桿有質(zhì)量要求,尺寸精度要求高。一般均采用預(yù)鍛。 預(yù)鍛模膛是用來對制坯后的坯料進(jìn)一步變形,合理地分配坯料的各部位的金屬體積,使其接近鍛件外形,改善金屬在終鍛模膛內(nèi)的流動(dòng)條件,保證終鍛時(shí)成形飽滿;避免折疊、裂紋或其他缺陷,減少終鍛模膛的磨損,同時(shí)還可以提高終端模膛壽命,使鍛件的尺寸穩(wěn)定。 叉形鍛件模鍛時(shí)常常在內(nèi)端角處產(chǎn)生不滿的情況,為避免這種缺陷,終鍛前需要進(jìn)行預(yù)鍛,用帶有劈料臺的預(yù)鍛模膛先將叉形部分劈開(如圖4.12)。這樣,終鍛時(shí)就會改善金屬流動(dòng)情況,保證內(nèi)端角部位充滿。 圖4.12
42、 叉形部分劈料臺 B=0.25B=0.25302=15 h=(0.4-0.7)H=0.541.5≈20 R取20。 可以是等寬的如圖所示,也可以是變寬的,而變寬的效果較好。 預(yù)鍛模膛和終鍛模膛的形狀基本一樣,也是根據(jù)熱鍛件圖加工出來的。 預(yù)鍛模膛與終鍛模膛的差別不大,為了盡可能做到預(yù)鍛后的坯料容易地放入終鍛模膛,預(yù)鍛模膛的寬度比終鍛模膛的小1-2,高度比終鍛模膛的高2-5,預(yù)鍛模膛的寬度有終鍛的111改為109;兩端的高度由41.5改為43;桿部的高度由19.3改為21,桿部中間部分由5改為5.5等。 為了鍛模制造方便,預(yù)鍛模膛的斜度一般應(yīng)與終鍛模膛相同。故鍛模斜度不變。
43、 預(yù)鍛模膛的圓角半徑一般比終鍛模膛大,這樣可以減輕金屬流動(dòng)阻力,防止產(chǎn)生折疊。一般 式中 C一般為2-5。 因此,預(yù)鍛模膛的圓角半徑取15。 此外,預(yù)鍛與終鍛不同之處詳見連桿熱鍛圖。 4.7 繪制計(jì)算毛坯圖 根據(jù)平面變形假設(shè)進(jìn)行計(jì)算并經(jīng)修正所得的具有圓形或方形截面的中間坯料叫計(jì)算毛坯或計(jì)算坯料,它的各個(gè)橫截面積等于沿鍛件長度上各相應(yīng)截面積加上飛邊的截面積。即: 式中 —任意一處計(jì)算毛坯的橫截面積; —相應(yīng)處鍛件的橫截面積; —相應(yīng)處飛邊的橫截面積; —相應(yīng)處飛邊
44、槽的橫截面積; —充滿系數(shù),形狀簡單的鍛件取0.3-0.5,形狀復(fù)雜的取0.5-0.8,兩端面一般取1,計(jì)算中,由于兩桿形狀復(fù)雜,取0.5 根據(jù)可以計(jì)算出計(jì)算毛坯上任意處的直徑(或邊長),即 根據(jù)連桿形狀的特點(diǎn),共選取13個(gè)斷面,分別計(jì)算、、、列于表4.13,并繪出連桿的截面圖和計(jì)算毛坯圖,見圖4.14為了設(shè)計(jì)滾擠模膛方便,截面圖和計(jì)算毛坯圖按鍛件熱尺寸計(jì)算。 由截面圖所圍面積,即為鍛件體積,得 =2012512=250240 平均斷面積: ==1009 平均端面邊長: ==31.8 按體積相等修正截面圖和計(jì)算毛坯
45、圖(見圖4.14中雙點(diǎn)劃線部分)。修正后最大端面積為1440,則最大斷面邊長為=49.4。其毛坯的尺寸計(jì)算數(shù)據(jù)如表4.13中所示。 表4.13 計(jì)算毛坯的計(jì)算數(shù)據(jù) 斷 面 號 =2或1.4 修正 修正 (修正) 1 246 252 498 22.3 - - 1.1 24.5 2 1658 176 1834 42.8 2000 44.7 1.1 49.2 3 1612 176 1788 42.3 2440 49.4 1.2 59.3 4 1888 176 2064 45.4 1
46、480 38.5 1.1 42.2 5 2392 176 2568 50.7 1300 36.1 1.1 39.7 6 308 176 484 22 - - 0.8 17.6 7 300 176 476 21.8 - - 0.8 17.4 8 268 176 444 21.1 - - 0.8 16.9 9 776 176 952 30.9 - - 0.9 27.8 10 1600 176 1776 42.1 - - 1 42.1 表4.7(續(xù)) 11 1764 176 1
47、940 44.1 - - 1 44.1 12 1600 176 1776 42.1 - - 1 42.1 13 125 252 252 15.9 - 0.9 14.3 4.8 制坯工步選擇 計(jì)算毛坯為雙頭一桿,應(yīng)簡化為兩個(gè)簡單計(jì)算毛坯來選擇制坯工步。連桿大頭一端: 金屬流入頭部的繁重系數(shù) 金屬沿軸向流動(dòng)的繁重系數(shù) 桿部錐度的大小的繁重系數(shù) 式中 ; ; ; 。 按圖4.14,此鍛件采用坺長—滾壓工步。為易于充滿,應(yīng)選用方料,先坺長,后開式滾壓,整個(gè)工步為:坺長——開式滾壓——預(yù)鍛
48、——終鍛。 圖4.14連桿的計(jì)算毛坯圖簡圖 4.9 確定坯料尺寸 由截面圖知, =21.5,大頭端計(jì)算毛坯桿部體積=80305,大頭端計(jì)算毛坯桿部長度=109,故可以拐點(diǎn)處尺寸: =42.1() 故桿部錐度為: =0.189 按截面有關(guān)公式求其截面面積: 坺長坯料截面積: =2130 滾壓坯料截面積: =(1.05-1.2)=1.11009=1110 坯料截面積:
49、 =2130-0.189(2130-1110) =1940() 式中 —計(jì)算毛坯頭部體積; —計(jì)算毛坯頭部長度; —平均斷面積。 毛坯邊長:=44 取=45 坯料體積: =(220326+170016)(1+0.03)=402052..26 式中:——燒損率 坯料長度: ==198.5 根據(jù)坯料的重量和長度,適于采用調(diào)頭模鍛,一
50、料兩件,料長為2002=400,經(jīng)試鍛調(diào)整后,下料長度定為420。 4.10 制坯模膛的設(shè)計(jì) 制坯工步的作用是為了初步改變原坯料的形狀,合理地分配坯料,以適應(yīng)鍛件橫截面積和形狀的要求,使金屬能較好地充滿模膛。不同形狀的鍛件采用的制坯工步不同。錘上鍛模所用的制坯模膛主要有坺長模膛、滾壓模膛、彎曲模膛、成形模膛等。本課題只有坺長和滾壓模膛。 (1) 滾壓模膛設(shè)計(jì) 滾壓模膛可以改變坯料形狀,起到分配金屬,是坯料某一部分截面積減小,某一部分截面積稍稍增大(聚料),獲得接近毛坯圖形狀和尺寸的作用。另外,滾壓還可以將毛坯滾光和清除氧化皮。采用開式滾壓,模膛的尺寸和形狀主要根據(jù)計(jì)算毛坯圖和
51、坯料橫截面尺寸來確定。 模膛高度h=k,可按各斷面的高度值繪出滾壓縱剖面外形見圖4.10,然后利用圓弧或直線光滑連接并進(jìn)行簡化。 模膛寬度為 桿部: ≈38 頭部: >+10=1.13+10 =1.13+10 =66 經(jīng)試生產(chǎn),調(diào)整模膛寬度為B=80。 模膛長度L等于計(jì)算毛坯圖的長度. 試用調(diào)整后,修改個(gè)別尺寸:最大高度由59.3改為h=81,以容納氧化皮。小頭部分作出了一定斜度,簡化后滾壓模膛如圖4.15所示。 圖4.15開式滾壓模膛外形設(shè)計(jì)簡圖 (2) 坺長模膛設(shè)計(jì) 坺長模膛用來減少坯料的截面積
52、,增加坯料長度。一般坺長模模膛是變形工步的第一道,它兼有清除氧化皮的作用。為了便于金屬縱向流動(dòng),在坺長過程中坯料不斷翻轉(zhuǎn),還要送進(jìn)。坺長模膛有坎部和倉部組成??膊渴侵饕ぷ鞑糠?,而倉部容納坺長后的金屬,所以在坺長模膛設(shè)計(jì)中,主要設(shè)計(jì)坎部尺寸,包括坎部的高度h,坎部的長度c和坎部的寬度B。設(shè)計(jì)依據(jù)是計(jì)算毛坯。由[3]表24.2-29,可知: ①坺長坎部高度 ==0.9 =17 式中: ——計(jì)算毛坯桿部體積 ——計(jì)算毛坯桿部長度 =222.8-2-39.5-20=161.3≈161 ②坺長坎長度: l==1.1
53、3 =1.1345=51=56 其中: 取1.1。 ③圓角圓弧半徑: =0.25l=0.2556=14 =10=140 ④模膛高度: B=+(10-20)=(1.3551+10)=78.5 取B=75。 ⑤模膛深度: E=1.2=1.243=53 ⑥坺長模膛長度: =195 按照上述設(shè)計(jì)可鍛出合格鍛件,但為了提高生產(chǎn)率,將坺長模膛的h縮小,、增大,坺長過程只需打擊三次。將計(jì)算數(shù)值與實(shí)際數(shù)值比較如表4.16所示。 采用圖4.17所示的坺長模
54、膛,坺長后毛坯見圖4.18,坺長部分某些截面小于計(jì)算毛坯最小截面。但是坺長部分長度比計(jì)算毛坯相應(yīng)部分長度小,結(jié)果在滾壓是靠近大小頭的部分金屬,除流向頭部外,還向桿部流動(dòng),滾壓是整毛坯長度還有一定的增長。滾壓后毛坯的形狀見圖4.18.由此可知,坺長后需滾壓的,為減少坺長打擊次數(shù),可減少坺長坎高度,增大圓角、圓弧半徑。坺長后毛坯表面是否粗糙不影響鍛件質(zhì)量。坺長后毛坯的長度可比相應(yīng)的計(jì)算毛坯長度短一些,以減小滾壓端部毛刺。 表4.16連桿鍛模坺長模膛尺寸 (mm) 模膛尺寸 數(shù)值 H L R 計(jì)算數(shù)值 17 56 14 140 目前采用數(shù)值 14 77 30、3
55、2 150 圖4.17 坺長模膛設(shè)計(jì) 圖4.18 坺長、滾壓后坯料形狀 4.11 模膛結(jié)構(gòu)設(shè)計(jì) 錘鍛模的結(jié)構(gòu)設(shè)計(jì)對鍛件品質(zhì)、生產(chǎn)率、勞動(dòng)強(qiáng)度、鍛模和鍛錘的使用壽命等有很大的影響。錘鍛模的結(jié)構(gòu)設(shè)計(jì)應(yīng)著重考慮模膛的布排、錯(cuò)移力的平衡及鍛模的強(qiáng)度、模塊尺寸、導(dǎo)向等等。 (1.模膛的布排 模膛的布排要根據(jù)模膛數(shù)以及各模膛的作用和操作方便安排。錘鍛模一般有多個(gè)模膛,終鍛模膛和預(yù)鍛模膛的變形力較大,在模膛布置過程中一般首先考慮模鍛模膛。 當(dāng)模鍛有預(yù)鍛模膛是,兩個(gè)中心(鍛模中心:錘鍛模的緊固一般都是利用楔鐵和鍵塊配合燕尾緊固下模,鍛模中心指鍛模燕尾中心線與上鍵槽中心線的交點(diǎn),
56、它是位于鍛桿軸心線上,應(yīng)是鍛錘打擊力的作用中心。模膛中心:鍛造時(shí)模膛承受鍛件反作用力的合力作用點(diǎn)。)時(shí),兩個(gè)模膛中心一般都不可能與鍛模中心重合。為了減少錯(cuò)差、保證鍛件品質(zhì),應(yīng)力求終鍛模膛和預(yù)鍛模膛中心靠近模鍛中心。在鍛模前后方向上,兩模膛中心均應(yīng)在鍵槽中心線上;在鍛模左右方向上,終鍛模膛與鍛模中心線的偏移量不要過大。 為了減小終鍛模膛與預(yù)鍛模膛中心距L,保證模膛壁有足夠的強(qiáng)度,可選用平行排列法(還有前后錯(cuò)開排列法、反向排列法),終鍛模膛和預(yù)鍛模膛中心位于鍵槽中心線上,L值減小的同時(shí)前后方向的錯(cuò)差量也較小,鍛件品質(zhì)好。 終鍛模膛和預(yù)鍛模膛的模膛中心位置確定后,模膛在模塊還不能完全放置,還需對
57、模膛的前后方向進(jìn)行排列。本課題采用鍛件大頭靠近鉗口,是鍛件質(zhì)量大且難出模的一段接近操作者,這樣操作方便、省力。 除終鍛模膛和預(yù)鍛模膛以外的其他模膛由于變形力較小,可布置在終鍛模膛和預(yù)鍛模膛兩側(cè)。模膛的排列應(yīng)與加熱爐、切邊壓力機(jī)和吃風(fēng)機(jī)的位置相應(yīng)。氧化皮最多的模膛是鍛模中頭道制坯模膛,應(yīng)靠近加熱爐的一側(cè),且在吹風(fēng)管對面,不要讓氧化皮吹落到終鍛模膛、預(yù)鍛模膛內(nèi)。假設(shè)加熱爐在鍛錘的右方,故坺長模膛布置在右邊,滾壓模膛在左邊,預(yù)鍛及終鍛工步從左至右。 (2.錯(cuò)移力的平衡與鎖扣的設(shè)計(jì) 錯(cuò)移力一方面使鍛件錯(cuò)移,影響尺寸精度和加工余量;另一方面加速鍛錘導(dǎo)軌磨損,使錘桿過早折斷。我們知道,設(shè)備的精度對減
58、小鍛件的錯(cuò)差有一定的影響,但最根本、最有積極意義的是在模具設(shè)計(jì)方面采取措施,因?yàn)楹笳叩挠绊懜苯樱哂袥Q定作用。模膛中心與錘桿中心不一致,終鍛模膛中心偏離鍛桿中心,產(chǎn)生偏心距。為了減小由這些原因引起的錯(cuò)移力,處設(shè)計(jì)時(shí)盡量使模膛中心與錘桿中心一致外,還可采用導(dǎo)向鎖扣。導(dǎo)向鎖扣的主要功能是導(dǎo)向,平衡錯(cuò)移力,它補(bǔ)充了設(shè)備的導(dǎo)向功能,便于模具安裝和調(diào)整。工字型鍛件不易檢查和調(diào)整其錯(cuò)移量,故采用縱向鎖扣。如圖4.19所示. 圖4.19縱向鎖扣 鎖扣尺寸,由噸位確定: =35,=45,=0.3,△=2,=,=3,=5。 由于上有坺長和滾壓模膛,故取=85。 (3.鉗口設(shè)計(jì) 終鍛和預(yù)鍛模膛
59、都必須設(shè)有鉗口,它位于模膛前方,鉗口可分夾鉗口與鉗口頸兩部分。夾鉗口在模鍛是是作為放置棒料及夾鉗用的,見圖4.20;鉗口頸是用于加強(qiáng)夾鉗聊頭與鍛件之間的連接,便于鍛件起模;在鍛造時(shí),鉗口作為澆鑄模膛檢驗(yàn)件的澆口之用。 圖4.20 鉗口 圖4. 21 常用鉗口形式 鉗口尺寸坯料邊長45選擇對應(yīng)得鉗口尺寸: =90, =40, =15 因?yàn)榈纛^模鍛,鉗口尺寸應(yīng)考慮第一件終鍛后飛邊不影響第二件模鍛,故定為:=80, =30,取=50。 鉗口頸尺寸有鍛件質(zhì)量選擇鉗口頸尺寸: =1.5, =8 取=20。預(yù)鍛鉗口頸尺寸需考慮兩件連接處發(fā)生斷裂等因素,將其加大到幾乎與整個(gè)鉗口
60、寬度相等。此時(shí),金屬消耗增加。 (4.模具強(qiáng)度設(shè)計(jì) 錘上鍛模與強(qiáng)度有關(guān)的破壞形式主要有下列4種:在燕尾根部轉(zhuǎn)角產(chǎn)生裂紋;在模膛深處沿高度方向產(chǎn)生的縱向裂紋;模壁打斷;承擊面打塌。外因是打擊力極高或反復(fù)打擊;內(nèi)因主要因?yàn)榻Y(jié)構(gòu)設(shè)計(jì)不合理,鍛模強(qiáng)度不夠。如模膛壁較薄,模塊高度較低,承擊面小,燕尾根部的轉(zhuǎn)角過小,模塊纖維方向分布不合理等。 對于長軸類鍛件,纖維方向應(yīng)與鍛件軸線方向一致。 模壁厚度是由模膛到模塊邊緣,以及模膛之間的壁厚。鍛件寬度為109(熱鍛尺寸),模膛的最小外壁厚度=1.720.8≈35。模膛間距=121.3。預(yù)鍛模膛與終鍛模膛的中心距為(109+21.3)=124.8
61、,取為125。 考慮鍛模應(yīng)用足夠的承擊面,鎖扣之間寬度取305,可使承擊面積達(dá)50000以上。 燕尾中心線至檢驗(yàn)邊的距離為+b+5+20=130+85+5+20=240. 故模塊的寬度為: 2235+5=475 模塊的長度為: ++=50+248+35=333,考慮到飛邊槽取350。 模塊高度最小為170,由于燕尾以及起重孔和檢查邊等因素取275。 用實(shí)測方法找出終鍛模膛中心離連桿大頭前端115,結(jié)合模塊長度及鉗口長度定出鍵槽中心線的位置為165。 故模塊尺寸為:475350275 (寬長高) (5.檢驗(yàn)角 檢驗(yàn)角在鍛模設(shè)計(jì)與制造時(shí),是各模膛和燕尾
62、尺寸的基準(zhǔn)面;在生產(chǎn)中士模具調(diào)整的依據(jù)。檢驗(yàn)角的二個(gè)平面互相垂直,一般是做在模塊前面與左面或有面,應(yīng)根據(jù)模膛排布情況而定。示意圖如圖4.22 寬度b b=5 高度h h取110 圖4.22 鍛模結(jié)構(gòu)圖 (6.鍛模材料 由鍛模種類和設(shè)備噸位選擇為5。模膛表面硬度為39-44HRC,燕尾部分硬度為32-37 HRC。 (7.燕尾與鍵槽及起重孔尺寸 燕尾與鍵槽尺寸由噸位選: b=260, h=50.5, b=50。 起重孔尺寸由噸位選: d=30, S=60 (8.定位鍵和楔鐵及墊片 楔鐵見零件圖所示,由噸位確定尺寸規(guī)格: 上楔鐵
63、: h=65, b=50.8, l=930 下楔鐵: h=65, b=50.7, l=1100 定位鍵見4.23圖所示,由噸位確尺寸規(guī)格: f=110, h=65, L=123, =62.5, =74.9 其他尺寸如圖所示。 圖4.23 定位鍵 墊片由噸位確定其尺寸: h=65, l=1000, =54 S=0.75 材料為35鋼。 (9.模膛尺寸極限偏差 鍛模模膛尺寸公差可按工廠規(guī)定的技術(shù)條件執(zhí)行。具體各模膛的公差各尺寸為: 終鍛: 深度 寬度 長度 預(yù)鍛: 深度 寬度
64、 長度 制坯: 深度 寬度 長度 坺長: 深度 寬度 長度 注:設(shè)計(jì)時(shí)一般在鍛模圖樣中都不標(biāo) (10.模膛表面粗糙度 整體模在生產(chǎn)中的表面粗粗度,可作為設(shè)計(jì)時(shí)參考,故取此些數(shù)據(jù)。預(yù)鍛型槽、分模面等部分經(jīng)過精銑后使其表面粗糙度達(dá)到R1.6m;終鍛型槽及毛邊槽橋部還需加以拋光,使表面粗糙度達(dá)R0.8m;毛邊槽倉部、起重孔及鉗口等非加工表面,銑削加工達(dá)R0.8m即可。 注:錘鍛模模膛表面粗糙度一般在鍛件圖樣中不標(biāo)出。 4.12 連桿模鍛流程 (1) 切料: 5000kN型剪機(jī)冷切。 (2) 加熱:
65、 半連續(xù)式爐,1220-1240。 (3) 模鍛: 2t模鍛錘,坺長、開滾、預(yù)鍛、終鍛,每班約生產(chǎn)1100件。 (4) 熱切邊: 1600kN切邊壓機(jī)。 (5) 磨毛邊: 砂輪機(jī)。 (6) 熱處理: 連續(xù)熱處理爐,調(diào)質(zhì)。 (7) 酸洗: 酸洗槽。 (8) 冷校正: 1t夾板錘。 (9) 冷精壓: 10000kN精壓機(jī)。 (10) 檢驗(yàn)。 4.13 連桿圖 圖4.24 連桿實(shí)體造型 圖4.25連桿凹模 、 參考文獻(xiàn) [1] 許發(fā)樾主編.使用模具設(shè)計(jì)與制造手冊.北京:機(jī)械工業(yè)出版社,2001 [2]
66、姚澤坤主編.鍛造工藝學(xué)與模具設(shè)計(jì).西安:西北工業(yè)大學(xué)出版社,2004 [3]周大雋主編.鍛壓技術(shù)數(shù)據(jù)手冊.北京:機(jī)械工業(yè)出版社,1998 [4]大連理工大學(xué)工程畫教研室編.機(jī)械制圖.北京:高等教育出版社,2003 [5] 呂炎主編.鍛造工藝學(xué).機(jī)械工業(yè)出版社,1995 [6]陳曉華主編.典型零件模具圖冊[M].北京:機(jī)械工業(yè)出版社,2006. [7]胡亞民主編.鍛造工藝過程與模具設(shè)計(jì)[M].北京:北京大學(xué)出版社,2006. [8]李志剛主編.模具大典第四卷:鍛模與粉末冶金模設(shè)計(jì)[M]. [9]于駿一主編.典型零件制造工藝[M]. 北京:機(jī)械工業(yè)出版社,1990. [10]黃毅宏、李明輝主編.模具制造工藝[M]. 北京:機(jī)械工業(yè)出版社,2007. [11]付建軍主編.模具制造工藝[M]. 北京:機(jī)械工業(yè)出版社,2009. [12]李 云主編.機(jī)械制造工藝及設(shè)備設(shè)計(jì)指導(dǎo)手冊[M].北京:機(jī)械工業(yè)出版社,2007. [13]余初靜撰寫施志輝指導(dǎo).連桿鍛模參數(shù)化設(shè)計(jì)及其數(shù)控加工編程的研究[D],2005. [14]李玉偉主編.Master
- 溫馨提示:
1: 本站所有資源如無特殊說明,都需要本地電腦安裝OFFICE2007和PDF閱讀器。圖紙軟件為CAD,CAXA,PROE,UG,SolidWorks等.壓縮文件請下載最新的WinRAR軟件解壓。
2: 本站的文檔不包含任何第三方提供的附件圖紙等,如果需要附件,請聯(lián)系上傳者。文件的所有權(quán)益歸上傳用戶所有。
3.本站RAR壓縮包中若帶圖紙,網(wǎng)頁內(nèi)容里面會有圖紙預(yù)覽,若沒有圖紙預(yù)覽就沒有圖紙。
4. 未經(jīng)權(quán)益所有人同意不得將文件中的內(nèi)容挪作商業(yè)或盈利用途。
5. 裝配圖網(wǎng)僅提供信息存儲空間,僅對用戶上傳內(nèi)容的表現(xiàn)方式做保護(hù)處理,對用戶上傳分享的文檔內(nèi)容本身不做任何修改或編輯,并不能對任何下載內(nèi)容負(fù)責(zé)。
6. 下載文件中如有侵權(quán)或不適當(dāng)內(nèi)容,請與我們聯(lián)系,我們立即糾正。
7. 本站不保證下載資源的準(zhǔn)確性、安全性和完整性, 同時(shí)也不承擔(dān)用戶因使用這些下載資源對自己和他人造成任何形式的傷害或損失。
最新文檔
- 6.煤礦安全生產(chǎn)科普知識競賽題含答案
- 2.煤礦爆破工技能鑒定試題含答案
- 3.爆破工培訓(xùn)考試試題含答案
- 2.煤礦安全監(jiān)察人員模擬考試題庫試卷含答案
- 3.金屬非金屬礦山安全管理人員(地下礦山)安全生產(chǎn)模擬考試題庫試卷含答案
- 4.煤礦特種作業(yè)人員井下電鉗工模擬考試題庫試卷含答案
- 1 煤礦安全生產(chǎn)及管理知識測試題庫及答案
- 2 各種煤礦安全考試試題含答案
- 1 煤礦安全檢查考試題
- 1 井下放炮員練習(xí)題含答案
- 2煤礦安全監(jiān)測工種技術(shù)比武題庫含解析
- 1 礦山應(yīng)急救援安全知識競賽試題
- 1 礦井泵工考試練習(xí)題含答案
- 2煤礦爆破工考試復(fù)習(xí)題含答案
- 1 各種煤礦安全考試試題含答案
相關(guān)資源
更多