畢業(yè)設計(論文)車床主軸加工工藝規(guī)程設計
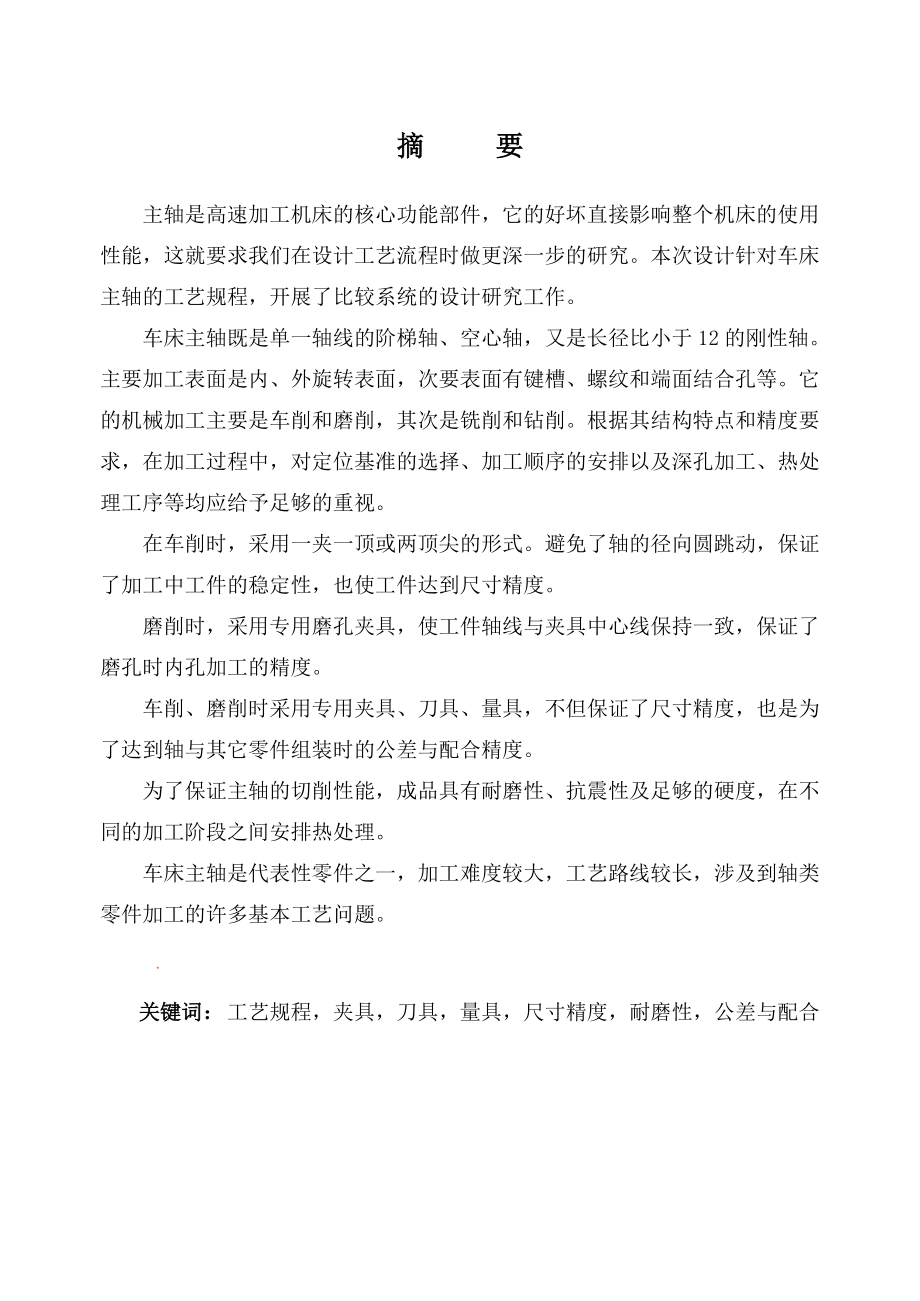


《畢業(yè)設計(論文)車床主軸加工工藝規(guī)程設計》由會員分享,可在線閱讀,更多相關《畢業(yè)設計(論文)車床主軸加工工藝規(guī)程設計(29頁珍藏版)》請在裝配圖網上搜索。
1、 摘 要 主軸是高速加工機床的核心功能部件,它的好壞直接影響整個機床的使用性能,這就要求我們在設計工藝流程時做更深一步的研究。本次設計針對車床主軸的工藝規(guī)程,開展了比較系統(tǒng)的設計研究工作。 車床主軸既是單一軸線的階梯軸、空心軸,又是長徑比小于12的剛性軸。主要加工表面是內、外旋轉表面,次要表面有鍵槽、螺紋和端面結合孔等。它的機械加工主要是車削和磨削,其次是銑削和鉆削。根據其結構特點和精度要求,在加工過程中,對定位基準的選擇、加工順序的安排以及深孔加工、熱處理工序等均應給予足夠的重視。 在車削時,采用一夾一頂或兩頂尖的形式。避免了軸的徑向圓跳動,保證了加工中工件的穩(wěn)定性,也使
2、工件達到尺寸精度。 磨削時,采用專用磨孔夾具,使工件軸線與夾具中心線保持一致,保證了磨孔時內孔加工的精度。 車削、磨削時采用專用夾具、刀具、量具,不但保證了尺寸精度,也是為了達到軸與其它零件組裝時的公差與配合精度。 為了保證主軸的切削性能,成品具有耐磨性、抗震性及足夠的硬度,在不同的加工階段之間安排熱處理。 車床主軸是代表性零件之一,加工難度較大,工藝路線較長,涉及到軸類零件加工的許多基本工藝問題。 . 關鍵詞:工藝規(guī)程,夾具,刀具,量具,尺寸精度,耐磨性,公差與配合 Abstract The main axle processes engine beds c
3、ore functional unit high speed, its quality immediate influence entire engine beds operational performance, this requests us when designs the technical process to do deeper step research. In view of this design, has done the quite systematic design research work. The lathe main axle is not only the
4、 sole spool threads steps and ladders axis, the canon, is also the length to diameter ratio is smaller than 12 rigid axes. The main processing surface is the inside and outside revolving surface, the secondary surface has the key slot, the thread and the end surface union hole and so on. Its machine
5、-finishing is mainly the turning and the grinding, next is the milling and drills truncates. According to its unique feature and the accuracy requirement, in the processing process, to locate the datum the choice, the processing sequence arrangement as well as the deep hole processing, the heat trea
6、tment working procedure and so on should give the enough value. When turning, as soon as uses clamps or two apexs forms. Has avoided the axis radial direction circle beat, has guaranteed in the processing the work piece stability, also enables the work piece to achieve the size precision. When g
7、rinding, uses the special-purpose honing jig, causes the work piece spool thread maintains consistent with the jig middle line, has guaranteed when the honing in hole processing precision. When turning, grinding uses the unit clamp, the cutting tool, the measuring instrument, not only has guarante
8、ed the size precision, is also to achieve time the axis and other components assembly common difference and the grade of fit. In order to guarantee that the main axle has the resistance to wear, the anti-knocking property and the enough degree of hardness, each working procedure carries on the ess
9、ential heat treatment. The lathe main axle is one of representative components, the processing difficulty is big, the craft route is long, involves to the axis class components processing many basic craft question. Therefore understood that its technical process is designers essential process! K
10、ey word: Technical process, jig, cutting tool, measuring instrument, size precision, resistance to wear, common difference and coordination。 目 錄 摘 要 1 abstract 2 第一章 前 言 4 第二章 工藝過程設計概論 2.1 工藝過程的基本要求及主要的技術依據 5 2.2 工藝過程的設計方法 5 第三章 車床主軸加工工藝及分析 3.
11、1 概述 8 3.2 支承軸頸為主軸的裝配基準 8 3.3 主軸工作表面的技術要求 9 3.4 主軸加工工藝過程分析 11 3.5 主軸加工中的幾個工藝問題 17 3.6主軸的機械加工工藝過程 20 第四章 結 論 26 謝 辭 27 參考文獻 28 第一章 前 言 機械制造業(yè)是為國民經濟提供裝備和為人民生活提供耐用消費品的產業(yè)。國民經濟各部門生產技術的進步和經濟效益的高低,在很大程度上取決于它所采用裝備的性能和質量。所以機械工業(yè)的技術水平和規(guī)模是衡量一個國家科技水平和經濟勢力的重要標準。
12、 在機械行業(yè)中,主軸的加工是代表性零件之一,它是高速加工機床的核心功能部件。由于主軸性能的好壞在很大程度上決定了整臺機床的加工精度和生產效率,因此,各工業(yè)發(fā)達國家都十分關注主軸的研究與發(fā)展,紛紛投入巨資, 裝備精良的加工和測試設備來提高主軸的工藝。盡管我們的科技人員一直努力,但是,與國外發(fā)達國家相比,我國的主軸的工藝設計仍存在著階段性的差距。集中表現(xiàn)為制造技術的落后——在設計方法和手段,制造工藝,制造過程自動化技術及管理技術諸方面都明顯落后于發(fā)達國家。 本次設計的主要目的是通過對主軸的工藝進行研究,解決編制主軸工藝規(guī)程中的實際問題,從而編制出較為合理的工藝規(guī)程。在通常的加工工藝
13、中,存在著主軸精度不高,耐磨性、穩(wěn)定性差、可靠性低等直接影響機床效率的問題,本次設計針對這些問題進行分析。通過采用合理的工序,專用的夾具、刀具、量具和嚴格的科學分析。在一定程度上使這些問題降到最低點或避免這些問題的發(fā)生。 目前,在經濟和科學技術方面,我國與世界各國的聯(lián)系日益緊密,中國市場與國際市場進一步接軌,面對國內外激烈的市場競爭,企業(yè)對技術的需要將更加強化和迫切,先進制造技術將得到更大的重視,機械工業(yè)科技發(fā)展正面臨著挑戰(zhàn)與機遇并存的新形勢。我們應當抓住機遇,迎接挑戰(zhàn),堅決貫徹“以科技為先導,以質量為主體”的方針,進一步推動機械工業(yè)的振興。而要實現(xiàn)機械工業(yè)的振興,就必須不斷提高企業(yè)
14、的產品自主開發(fā)能力和制造技術水平。 第二章 工藝過程設計概論 2.1 工藝過程的基本要求及主要的技術依據 2.1.1 設計工藝過程的基本要求 1) 保證產品的質量符合設計圖提出的全部要求; 2) 保證符合要求的勞動生產效率; 3) 保證經濟的合理性; 質量、生產率和經濟性,是制定工藝過程所必須滿足的技術要求。另外,在設計工藝過程時,必須特別重視改善勞動條件,保障生產安全。 新技術和新工藝的發(fā)展,如毛坯的精化,特種工藝技術和超精工藝技術的發(fā)展,以及計算機技術的應用等,都將對產品的質量和生產周期有很大的影響。隨著技
15、術的發(fā)展,工藝過程設計也應不斷地優(yōu)化,以便能全面保證質量、生產效率和經濟性的要求,并保證產品質量的穩(wěn)定。零件機械加工的工藝過程,取決于零件的要求、產量的大小和現(xiàn)場的生產條件。所以,在設計工藝過程時,需對這些主要技術依據進行分析。 2.1.2 零件圖及技術條件 零件圖及其技術條件,是制造對象的技術要求。在零件圖上應包括: 1)構形 有必要的投影、剖視或剖面等,必須使零件定形。另外,還應有確定構形大小的全部尺寸。 2)技術要求 有關尺寸、形狀和位置關系允許的偏差,表面粗糙度以及某些特殊的技術要求(如平衡、重量等)。 3)材料 有關材料的牌號,毛坯類
16、型,熱處理方法及檢驗等級,材料的無損探傷和表面保護要求等。 另外,所有不能用圖形或符號表示的要求或說明,一般可用文字寫在圖紙或文件上。在設計工藝過程時,應對零件圖進行詳細的工藝分析,以便掌握工藝關鍵從而采取必要的工藝措施。 2.2 工藝過程的設計方法 2.2.1 車床主軸的工藝特點和工藝措施 由于車床主軸要求有很高的質量,效能和可靠性,因此在構造下的特點一般有下列幾個方面: 1)零件的表面及整體構形復雜; 2)零件的制造質量要求高,技術要求(精度、粗糙度)以特種技術條件等要求十分嚴格; 3)可選用材料的品種多,
17、其中包括很多優(yōu)質和難加工材料,并廣泛地進行熱處理和表面處理。 由于零件在構造上有上述這些要求,因此在工藝上常采用下述工藝措施來保證生產中的質量、生產效率和經濟性的要求: (1) 合理地選擇加工方法,以保證經濟地獲得精度高,構造形狀復雜的表面; (2) 將工藝過程劃分為幾個階段進行加工,以逐步保證低剛度、高精度的技術要求; (3) 根據集中或分散的原則,合理地將各表面的加工組合成若干個工序,以保證位置精度和提高生產效率; (4) 合理地選擇工藝基準,以利于保證位置精度的要求; (5) 正確地安排熱處理工序及其位置,以保證獲得規(guī)定的機械性能,同時有利于改善材料的加工性能和減少變形對精度
18、的影響; (6) 合理安排各類輔助工序,使工藝過程順利的執(zhí)行其特殊的技術要求。 設計工藝過程,就是要設計工序的內容、數目和順序。一般先進行總體布局,即進行工藝路線的設計,然后,再對工序進行詳細設計。因此,在設計機械加工工藝過程時,應對組成產品的各種零件進行相似性分析,以便找出最優(yōu)化的生產組織形式,還要對各零件和組件整個的工藝過程的全部工序的工藝尺寸系統(tǒng),定位基準系統(tǒng),工序時間,工序成本等等因素進行分析,以便找出各工序在質量,生產效率和經濟性方面的相互聯(lián)系。從而確定最佳的加工路線和最優(yōu)化的加工方式。 2.2.2 設計工藝過程的步驟 1、 確定生產類型及組織形式 2、 零
19、件圖的工藝分析 零件圖是制造零件的主要技術依據,應對其構形、技術要求和材料進行仔細的工藝分析。特別是對主要表面及重要的技術要求及其保證方法,位置尺寸的標注等應作重點分析,以掌握在加工過程中的工藝關鍵問題。 3、 確定毛坯 毛坯的種類及其質量對機械加工有著密切的關系,提高毛坯質量、減少機械加工勞動量,可大大提高材料的利用效率、降低機械加工的成本,因此,需根據產量和毛坯車間的現(xiàn)場生產條件來加以綜合解決。 4、 設計工藝路線 工藝路線設計是設計工藝過程的關鍵步驟,常需要進行方案的論證對與分析,其內容包括: 1) 選擇各表面的最后加工方法以及該方法的準備工序。 2) 依據過程的階段和工序
20、集中與分散原則的分析,進行工序組合; 3) 設計工藝基準(工序、定位和測量基準)系統(tǒng),以確定工序的順序安排; 4) 選擇熱處理工序及其位置安排; 5)安排輔助工序。 5、工序詳細設計 工藝路線確定后,可進行工序內容的設計,其內容包括: 1)選擇加工用的設備及工藝裝備; 2)確定加工余量; 3)計算全部工序尺寸及偏差; 4)選擇合理的切削用量與潤滑冷卻液; 在設計工序時,對某些復雜的重點工序,有時需要設計工序的調整卡。 6、計算工時定額 7、填寫工藝文件 第三章 車床主軸加工工藝及分析 3.1 概 述
21、 車床主軸的功用及結構特點: 車床主軸不但傳遞旋轉運動和扭矩,而且是工件或刀具回轉精度的基礎,是車床的關鍵零件之一,所以一般機床主軸的扭轉剛度和彎曲剛度都很高。 機床主軸不但傳遞旋轉運動和扭矩,而且要求工件或刀具的回轉精度(徑向圓跳動、端面圓跳動、回轉軸心線的穩(wěn)定性等)很高,從而要求主軸的回轉精度更高。影響主軸回轉精度的因素有:主軸本身的結構尺寸及動態(tài)特征(動態(tài)剛度、固有頻率等);主軸本身及軸承的制造精度;軸承的結構及潤滑;裝在主軸上齒輪等的布置;主軸及主軸上固定件的動平衡等。 車床主軸既是一單軸線的階梯軸、空心軸,又是長徑比小于12的剛性軸。主要加工表面是內、外旋轉表面,次要表面有
22、鍵槽、、螺紋和端面結合孔等。它的機械加工主要是車削和磨削,其次是銑削和鉆削。根據其結構特點和精度要求,在加工過程中,對定位基準的選擇、加工順序的安排以及深孔加工、熱處理工序等均應給予足夠的重視。 根據主軸的工作特點,對它的設計要求有:①合理的結構設計②足夠的剛度③一定的尺寸精度、形狀精度、位置精度和表面精度④足夠的耐磨性、抗振性及尺寸穩(wěn)定⑤由于主軸在旋轉過程中承受交變載荷,因此它還應具有一定的抗疲勞強度。其中②④⑤三項要求,主要通過合理的結構設計,正確的選擇主軸材料及熱處理工藝來予以解決,而對于主軸的制造精度則應由機械加工來加以保證。 車床主軸是代表性零件之一,加工難度較大,工藝路線較長,
23、涉及到軸類零件加工的許多基本工藝問題。下面通過對車床主軸的技術條件的分析和工藝過程的討論。 3.2 主軸的裝配基準 支承軸頸制造精度直接影響主軸的回轉精度,主軸上各重要表面均以支承軸頸為設計基準,有嚴格的位置要求。 支承軸頸采用錐面結構,是為了使軸承內圈能漲大以調整軸承間隙。軸承內圈是薄壁零件,裝配時軸頸上的形狀誤差會反映到內圈的滾道上,影響主軸回轉精度,故必須涂色檢查接觸面積,嚴格控制軸頸形狀誤差。 主軸在主軸箱中是以它的三個支承軸頸與相應的軸承內孔配合,從而確定了主軸在主軸箱中的徑向位置。主軸支承軸頸表面的制造精度(圓度、素線平行度、垂直度)將直接影響主軸的工作精度
24、,造成主軸的徑向圓跳動和端面圓跳動。這些跳動又影響工件的加工精度。主軸上的螺帽和軸承端面對主軸回轉軸心線的垂直度誤差是使主軸產生端面圓跳動的原因之一。 3.3 主軸工作表面的技術要求 3.3.1 車床主軸錐孔 車床主軸錐孔是用來安裝頂尖或刀具柄的,前端圓錐面和端面是安裝卡盤或花盤的。這些安裝夾具或刀具的定心表面均是主軸的工作表面。對于它們的要求有:內外錐面的尺寸精度、形狀精度、粗糙度和接觸精度;定心表面相對于支承軸頸A-B軸心線的跳動等。它們的誤差會造成夾具或刀具的安裝誤差,從而影響工件的加工精度。如圖: 圖(2—1) 安裝偏心對加工精度的影響 a) 卡盤
25、安裝偏心 O-O定位面軸線 O1-O1實際回轉軸線 b) 莫式錐孔和支撐軸徑不同軸 O-O頂尖孔中心線 O1-O1實際回轉軸線 c) 定心表面傾斜于回轉中心線 O-O定位面軸線 O1-O1實際回轉軸線 當主軸軸外端外錐相對于支承軸頸有同軸度誤差時(圖a),會使卡盤產生安裝偏心;主軸的莫氏錐度相對于支承軸頸表面的同軸度誤差也會使前后頂尖形成的軸心線與實際的回轉軸心線偏離(圖b)。此外主要端部定心表面軸心線對支承頸表面的軸心線傾斜,會造成安裝在定心表面上的夾具及工件或刀具和回轉中心不同軸,而且是離軸端愈遠,同軸度誤差值愈大(圖c)。因此,在機床精度檢驗標準中,規(guī)定了近主軸端部和離
26、軸端300mm處的圓跳動誤差。 如表(2—1):主軸各表面的粗糙度 表面類別 粗糙度要求 一般機床 精密機床 支承軸頸表面 采用滑動軸承 0.32~0.08 0.08~0.01 采用滾動軸承 0.63 0.32 工作表面 0.63 0.32~0.08 其它配合表面 1.25 1.25~0.32 3.3.2 空套齒輪軸頸的技術要求 空套齒輪軸頸是和齒輪孔相配合的表面,對支承軸頸應有一定的同軸度要求,否則會引起主軸傳動齒輪嚙合不良。當主軸轉速很高時,還會產生振動和噪聲,使工件外圓產生振紋,尤其在精車時,這種影響更為明顯。 空套齒輪軸
27、頸對支承軸頸A-B的徑向圓跳動允許差為0.015mm。 3.3.3 螺紋的技術要求 主軸上的螺紋一般用來固定零件或調整軸承間隙。螺紋的精度要求是限制壓緊螺母端面跳動量所必須的。如果壓緊螺母端面跳動過大,在壓緊滾動軸承的過程中,會造成軸承內環(huán)軸心線的傾斜,引起主軸的徑向跳動(在一定條件下,甚至會使主軸產生彎曲變形),不但影響加工精度,而且影響到軸承的使用壽命。因此主軸螺紋的精度一般為6h ;其軸心線與支承軸頸軸心線A-B的同軸度允許為¢0.025mm,擰在主軸螺紋上的螺母支承端面圓跳動允差是在50mm半徑上為0.025mm。 3.3.4 主軸各工作表面的硬度要求
28、所有的機床主軸的支承軸頸表面、工作表面及其它配合表面都受到不同程度的摩擦作用。在滑動軸承配合中,軸頸與軸瓦發(fā)生摩擦,要求軸頸表面有較高的耐磨性。在滾動軸承時,摩擦轉移給軸承環(huán)和滾動體,軸頸可以不要求很高的耐磨性,但仍要求適當的提高其硬度,以改善它的裝配工藝性和裝配精度。 定心表面(內外錐面、圓柱面、法蘭圓錐面等)因相配件(頂尖、卡盤等)需經常拆卸,易碰傷,拉毛表面,影響接觸精度,所以也必須有一定的耐磨性。當表面硬度在HRC45以上時,拉毛現(xiàn)象可大大改善。主軸的工作表面表面粗糙度值Ra在0.8~0.2um之間。 3.3.5主軸的材料和熱處理 表(2-
29、2):主軸常用材料及熱處理 主軸種類 材料 預備熱處理方法 最終熱處理方法 表面硬度(HRC) 車床、銑床主軸 45鋼 正火或調質 局部淬火后回火 45~52 外圓磨床砂輪軸 65Cr 調質 高頻淬火后回火 50~58 專用車床主軸 40Cr 調質 局部淬火后回火 52~56 齒輪磨床主軸 20CrMnTi 正火 滲碳淬火 58~63 臥式鏜床主軸 精密外圓磨床砂輪軸 38CrMo AlA 調質 消除內應力處理 滲氮 65以上 3.4 主軸加工工藝過程分析 3.4.1 軸類零件的技術要求
30、 (1)尺寸精度 凡是與滾動軸承內圈相配的支承軸頸處的尺寸精度應按滾動軸承的精度等級選取。凡是與齒輪相配的軸頸處的尺寸精度,應按相配齒輪的最高精度等級查取。這些主要表面的尺寸精度一般取IT5~IT8級。 (2)形狀精度 軸頸處的幾何形狀精度主要是指圓度或圓柱度,一般應限制在尺寸公差之內。凡與滾動軸承或與齒輪相配處的軸頸的尺寸形狀,也應按滾動軸承或齒輪的精度查取。一般常取3~8um,并用框格標注。 (3) 位置精度 軸類零件是旋轉類零件,軸上裝有傳動件,希望其轉動平穩(wěn),無振動和噪聲,這就要求軸上裝配表面的軸線相對于支承軸頸軸線有同軸度要求,對普通精度的主軸可取0.01~
31、0.03mm;高精度軸可取0.001~0.005mm,一般用徑向圓跳動來標注。 (4)表面粗糙度 支承軸頸處表面粗糙度取Ra0.16~0.63um,配合表面的粗糙度取Ra0.63~2.5um。 3.4.2 軸類零件的材料與毛坯 (1)材料 一般軸類零件用45鋼,采取相應的調質處理后,可獲得一定的強度,韌度和耐磨性。 對中等精度而有較高轉速的軸類零件,可采用40Cr等合金鋼,調質處理及表面淬火后具有較高的綜合力學性能。 對高精度主軸可采用GCr15鋼或65Mn鋼,通過調質處理后獲得更高的耐磨性和耐疲勞性。 對高速重載下工作的主軸,可采用20CrMnTi或2
32、0Cr等低碳合金鋼或38CrMoAl合金結構鋼,經過滲碳淬火或滲氮后,具有很高的硬度,耐沖擊任性和心部高強度的特點,但是熱處理變形大。在采用滲氮時應家一道去應力工序,并且安排在粗磨之后進行,是因為滲氮變形小,且滲氮層較薄之故。 (2)毛坯 凡具有較高力學性能要求的軸,或直徑相差較大的階梯軸,均采用鍛件,對不重要的光軸或直徑相差不大的階梯軸,可采用熱軋棒料或冷拉棒料。 3.4.3 加工階段的劃分 主軸加工過程中的各加工工序和熱處理工序均會不同程度的產生加工誤差和應力,因此要劃分加工階段。主軸加工基本上劃分為下列三個階段。 1. 粗加工階段 (1) 毛坯處理 毛坯
33、備料 鍛造和正火(工序) (2) 粗加工 鋸去多余部分,銑端面、鉆中心孔和荒車外圓等(工序) 主要目的是:用大的切削用量切除大部分余量,把毛坯加工到接近工件的最終形狀和尺寸,只留下少量的加工余量,通過這階段還可以及時發(fā)現(xiàn)鍛件裂紋等缺陷,采取相應措施。 2. 半精加工階段 (1) 半精加工前熱處理 對于40Cr合金鋼一般采用調質處理以達到HRC20~25 (2) 半精加工 車工藝錐面(定位錐孔)、半精車外圓端面和鉆深孔等(工序) 主要目的是:為精加工作好準備,尤其為精加工作好準備。對于一些要求不高的表面,在這個階段加工到圖樣規(guī)定的要求。 3. 精加工階段 (1
34、) 精加工前熱處理 局部高頻淬火(工序); (2) 精加工前各種加工 粗磨定位錐面、粗磨外圓、銑鍵槽,以及車螺紋等(工序); (3) 精加工 精磨外圓和內外錐面以保證主軸是重要表面的精度(工序); 目的是:把各表面都加工到圖樣規(guī)定的要求。各階段的劃分大體以熱處理為界。 由此可見,整個主軸加工的工藝過程,就是以主要表面(支承軸頸、錐孔)的粗加工、半精加工、精加工為主,適當的插入其它的表面的加工工序而組成的,這就說明了,加工階段的劃分起主導作用的是工件的精度要求。對于一般精度的機床主軸,精磨是最終工序。對精密機床的主軸,還要增加光整加工階段,以求獲得更高的尺寸精度和更低的表面粗
35、糙度。 3.4.4 定位基準的選擇 以兩頂尖孔作為軸類零件的定位基準,既符合基準重合原則,又能使基準統(tǒng)一,所以,只要有可能,就盡量采用頂尖孔作為定位基準。本次設計中的粗車、半精車、精車、粗磨、精磨各外圓表面和端面、銑鍵槽和車螺紋等工序,都是頂尖孔作為定位基準。 兩頂尖孔的質量好壞,對加工精度影響很大,應盡量做到兩頂尖軸線重合、頂尖接觸面積大、表面粗糙度低。否則,將會因工件與頂尖間的接觸剛度變化產生加工誤差。因此經常注意保持兩頂尖的質量,是軸類零件加工的關鍵問題之一。 深孔加工后,可以采用帶頂尖孔的錐堵作為定位基準。 為了保證支承軸頸與兩端錐
36、孔的同軸度要求,需要應用互為基準原則。如本圖中主軸在車小端1:20錐孔和大端莫氏6號內錐孔時,用的是與前支承軸頸相鄰而又是用同一基準加工出來的外圓柱表面為定位基面(直接用前支承軸承作為定位基準當然更好,但由于軸頸有錐度,在制造托架時會增加困難);精車各外圓包括支承軸頸的1:12錐度時,即是以上述前后錐孔內所配錐堵的頂尖孔作為定位基準面。在粗磨莫氏6號內錐孔時,又是以兩圓柱表面為定位基準面,這就符合互為基準原則。 在粗精磨兩個支承軸頸的1:12錐度時,再次以粗磨后的錐孔所配錐堵的頂尖孔為定位基準。在最后精磨莫氏6號內錐孔時,直接以精磨后的前支承軸頸和另一圓柱面為定位基準面,基準再一次轉換。隨
37、著基準的不斷轉換,定位精度不斷提高。轉換過程就是提高過程。使加工有一次比一次精度更高的定位基準面?;鶞兽D換次數的多少,要根據加工精度要求而定。 在精磨莫氏6號內錐孔的定位方法中,采用了專用夾具,機床主軸僅起傳遞扭矩的作用,排除了主軸組件本身的回轉誤差,因此提高了加工精度。 精加工主軸外圓表面也可用外圓表面本身來定位,既在安裝工件時以支承軸頸表面本身找正。如圖所示, 圖(2—2) 錐套心軸 1—心軸 2—錐套 3—墊圈 4—螺母 5—夾頭 外圓表面找正是采用一種可拆卸的錐套心軸,心軸依靠螺母4和墊圈3壓緊
38、在主軸的兩端面上。心軸兩端在中心孔,主軸靠心軸中心孔安裝要機床的前后頂尖上,以支承軸頸表面找正時,適當敲動工作,使支承軸頸的徑向圓跳動在規(guī)定的范圍內(心軸和主軸靠端面上摩擦力結合在一起,主軸和錐套并不緊配,留在間隙,允許微量調整),然后進行加工。 用這種方法,只需要準備幾套心軸,因此簡化了工藝裝備,節(jié)省了修正中心孔工序,并可以一次安裝中磨出全部外圓。 3.4.5 工序的安排順序 軸類零件各表面的加工順序,與定位基準的轉換有關,即先行工序必須為后續(xù)工序準備好定位基準,粗、精基準選定后,加工順序也就大致排定。 由表2可見,主軸的工藝路線安排大體如下:毛坯制造—正火—車端面鉆中心
39、孔粗車—調質—半精車—表面淬火—粗、精磨圓錐面—磨錐孔。在安排工序順序時,還應該注意下面幾點。 a) 就基準統(tǒng)一而言,希望始終以頂尖孔定位,避免使用錐堵,則深孔加工應安排在最后,但深孔加工是粗加工工序,要切除大量余量金屬,會引起主軸變形,所以最好在粗車外圓之前就把深孔加工出來。 b) 外圓加工順序安排工作要照顧主軸本身的剛度,應先加工大直徑后加工小直徑,以免一開始就降低主軸剛度。 c) 鍵槽加工應安排在精車之后,粗磨之前,如在精車之前就銑出鍵槽,就會造成斷續(xù)車削,既影響質量又易損壞刀具,而且也難控制鍵槽 的尺寸精度,但這些表面也不宜安排在主要表面最終加工工序之后進行,以防在反復運輸
40、中,碰傷主要表面。 d) 主軸的螺紋對支承軸頸有一定同軸度要求,宜放在淬火后的精加工階段進行,以免受半精加工所產生的應力以及熱處理變形的影響。 e) 主軸系加工要求很高的零件,需安排多次檢驗工序。檢驗工序一般安排在各加工階段前后,以及重要工序前后和花費工時較多的工序前后,總檢驗則放在最后,心要時,還應安排探傷工序。 3.4.6 主軸中心通孔的加工 1、一般把長度與直徑之比大于5的孔稱為深孔。第一類主軸的中心通孔都是深孔。深孔加工比一般孔的加工要困難和復雜的多,原因是: (1) 刀具細而長,剛性差,鉆頭容易引偏,使被加工孔的軸心線歪斜; (2) 排屑困難;(3)鉆頭的散熱
41、條件差,容易喪失切削能力; 針對深孔加工的不利條件,一般采用工件旋轉、刀具進給或用刀具鉆中心空后,在深空鉆。 2、主軸錐孔的精加工 主軸錐孔的精加工是主軸加工的最后一個關鍵工序,由于對主軸錐孔的精度要求高,這道工序往往成為生產中薄弱環(huán)節(jié),許多工廠通過長期的實踐,已成功地用舊機床改裝成專用的主軸錐孔磨床,或設計制造了專用的磨夾具,不僅能穩(wěn)定地生產一般精度機床的主軸,對于高精度機床的主軸也都穩(wěn)定地達到質量要求,并且提高了生產率, 如圖: 圖(2-3) 主軸錐孔專用磨床 如前所述,主軸錐孔磨削的定位方法應該符合基準重合的原則,即以兩個支承軸頸表面作為定位基準面,并
42、以軸肩作軸向定位。 安裝主軸支承軸頸的夾具已有若干種,最初采用和車床中心架相類的夾具如下圖1,夾具的萬能性好,但是支承銷的接觸面積小,容易磨損,需要經常調整支承軸頸的外圓中心與砂輪中心的等高,而且整個夾具以及支承部分的剛性都較差,適用于單件小批量生產及一般精度的主軸。比上一種夾具有所改進了的是圖b所示的剖分軸承式磨夾具。這種夾具用銅瓦支承,與主軸軸頸刮配,能保證軸頸和軸瓦之間的良好配合。這種夾具制造容易,前后夾具可以與底座固定成一個整體,因此無論是夾具本身還是支承部分的剛性都比前一種為好,可以保證高的加工精度,缺點是軸瓦易磨損,需要定時刮研,而且容易使工件的支承軸頸拉毛。目前使用著一種V形磨
43、夾具如圖c。這種夾具由一個V形塊,兩塊硬質合金墊塊,一套壓緊螺釘及支架構成。用V形磨夾具加工主軸錐孔的精度高,質量穩(wěn)定,使用方便,通用性好,當然夾具和墊塊的制造要求高,主軸前后支承軸頸的V形塊有分成兩件的,亦做成一個整體的,后者的剛性比前者更高,但通用性較差。 圖(2-4) 主軸錐孔的磨夾具 3.4.7 鍵槽銑刀 鍵槽銑刀,它主要用于加工圓頭封閉鍵槽。它有兩個刀齒,圓柱面和端面上都有切削刃,端面切削刃延到中心,工作時能沿軸線作進給運動,按國家標準規(guī)定,直柄鍵槽銑刀d=2~22mm,錐柄鍵槽銑刀直徑d=14~50mm。鍵槽銑刀直徑的精度等級有和
44、兩種,通常分別加工和鍵槽。鍵槽銑刀的圓周切削刃僅在靠近端面的一小段長度內發(fā)生磨損,重磨時只需刃磨端面切削刃,銑刀直徑不變。 如下圖所示: 圖(2-5) 鍵槽銑刀 3.5 主軸加工中的幾個工藝問題 3.5.1 錐堵和錐堵心軸的使用 對于空心的軸類零件,當通孔加工后,原來的定位基準——頂尖孔已被破壞,此后必須重新建立定位基準。對于通孔直徑較小的軸,可直接在孔口倒出寬度不大于2mm的60錐面,代替中心孔。而當通孔直徑較大時,則不宜用倒角錐面代之,一般都采用錐堵或錐堵心軸的頂尖孔作為定位基準。 當主軸錐孔的錐度較小時(車床的主軸的錐孔為1:20和莫氏6號)就常
45、用錐堵,如圖所示: 圖(2-6) 錐 堵 使用錐堵或錐堵心軸時應注意以下問題。 (1)一般不中途更或拆裝,以免增加安裝誤差。 (2)錐堵心軸要求兩個錐面應同軸,否則擰緊螺母后會使用工件變形。 3.5.2 頂尖孔的研磨 因熱處理、切削力、重力等的影響,常常會損壞頂尖孔的精度,因此在熱處理工序之后和磨削加工之前,對頂尖孔要進行研磨,以消除誤差。常用的研磨方法有以下幾種。 (1) 用油石或橡膠砂輪夾在車床的卡盤上,用裝在刀架上的金剛鉆將它的前端修整成頂尖形狀(60圓錐體),接著將工件頂在油石或橡膠砂輪頂尖和車床后頂尖之間如圖所示,并加少
46、量的潤滑油,然后開動車床使油石或橡膠砂輪轉動,進行研磨。研磨時用手把持工件并連續(xù)而緩慢的轉動。這種研磨中心孔方法效率高,質量好,也簡便易行。 (2) 用硬質合金頂尖刮研 把硬質合金頂尖的60圓錐體修磨成角錐的形狀,使圓錐面只留下4-6條均勻分布的刃帶,這些刃帶具有微小的切削性能,可對頂尖孔的幾何形狀作微量的修整,又可起擠光的作用。這種方法刮石研的頂尖孔表面粗糙度達Ra0.8u以下,精度較高,還具有工具壽命長,刮研效率比油石高的特點,所以一般主軸的頂尖孔可以用此法修研。 如圖(2-7): 圖(2-7) 用油石研磨頂尖孔 1—油石頂尖 2—工件 3—后頂尖 3.5.3 主
47、軸錐孔加工 主軸前端錐孔和主軸支承軸頸及前端短錐的同軸度要求高,因此磨削主軸的前端錐孔,常常成為機床主軸加工的關鍵工序。成批生產時大都用專用夾具加工,如圖所示,采用這種聯(lián)接方式,機床只起傳遞扭矩作用,排除了磨床主軸圓跳動或同軸度誤差對工件的影響,也可減少機床本身的振動對加工精度的影響。 圖(2-8)磨主軸錐孔夾具 1—鋼球 2—彈簧 3—硬質合金 4—彈性套 5—支架 6—底座 7—撥盤 3.5.4 主軸各外圓表面的精加工和光整加工 主軸的精加工都是用磨削的方法,在熱處理工序之后 進行,用以糾正在熱處理中產生的變形,最后達到所需的精度和表面粗糙度。磨削加工
48、一般能經濟地達到IT6和a0.8-0.2um。對于一般精度的車床主軸,磨削是最后的加工工序。而對精密主軸還需要進行光整加工,光整加工用于精密主軸上尺寸公差等級IT5表面粗糙度低于Ra0.1um的加工表面。 3.5.5 對軸類零件的檢驗 軸類零件在加工過程中和加工完以后都要按工藝規(guī)程的要求進行檢驗,檢驗的項目包括表面粗糙度、硬度、尺寸精度、表面形狀精度和相互位置精度。 1、表面粗糙度和硬度的檢驗:硬度是在熱處理之后用硬度計抽檢。 表面粗糙度般用樣塊比較法檢驗,該主軸所用的就是這種方法。對于精密零件可用干涉顯微鏡進行測量。 2、精度檢驗:精度檢驗應按一定順序進
49、行,先檢驗形狀精度,然后檢驗尺寸精度,最后檢驗位置精度。這樣可以判明和排除不同性質誤差之間對測量精度的干擾。 (1) 形狀精度檢驗 圓度為軸的同一橫截面內最大直徑與最小直徑之差。一般用千分尺按照測量直徑的方法即可檢測。精度高的軸需用比較儀檢驗。圓柱度同樣可用千分尺檢測,彎曲度可以用千分表檢驗,把工件放在平板上工件轉動一周,千分表讀數的最大變動量就是彎曲誤差值。 (2) 尺寸精度檢驗 在單件小批量生產中,軸的直徑一般用外徑千分尺檢驗。精度較高時,可用杠桿卡規(guī)測量,臺肩長度可用游標卡尺、深度游標卡尺和深度千分尺檢驗。該主軸所用的就是采用這種方法。 (3) 位置精度檢驗 為
50、提高檢驗精度和縮短檢驗時間,位置精度檢驗多采用專用檢具,錐孔的接觸精度用專用錐度量規(guī)涂色檢驗,要求接觸面積在70%以上,分布均勻而大端接觸較硬,即錐度只允許偏小,這項檢驗應在檢驗錐孔跳動前進行。 如圖所示: 圖(2-9)專用錐度量規(guī) 1—擋鐵 2—鋼球 3、4—V形架 5—檢驗心棒 各量表的功用如下:量表7檢驗錐孔對支承軸頸的同軸度誤差距軸端300mm外量 表8檢查錐孔軸心線對支承軸頸軸心線的同軸度誤差;量表3、4、5、6檢查各軸相對支承軸頸的徑向跳動;量表10、11、12檢驗端面跳動;量表9測量主軸的軸向竄動。 3.6主軸的機械加工工藝過程 經過對主軸結
51、構特點、技術條件的分析,即可根根據據生產批量、設備條件等編制主軸的工藝規(guī)程。編制過程中應著重考慮主要表面(如支承軸頸、錐孔、短錐及端面等)和加工比較困難的表面(如深孔)的工藝措施。從而正確地選擇定位基準,合理安排工序。(見零件圖紙) 表(2—3) CA6140車床主軸小批生產的工藝過程 序 號 工 序 工 藝 內 容(02051主軸) 設 備 1 備料 鍛件,退火。40Cr,工序圖見附圖一 2 熱處理 正火。 3 鉗 小端劃中心線,鉆中心孔A4。 4 銑端面鉆中心孔 銑端面 中心孔機床 5
52、 粗車 a、φ80d9及以左外圓均留余量7.46,肩臺留余量2; b、φ80.33(1:12)及以右外圓各留余量7.46, 1:12外錐按大端尺寸留余量,各肩臺留余量2; 以φ100f6及φ70外圓為定位基準: c、車右端面,總長留余量0.5,鉆中心孔A4; d、粗車φ170留余量7.63,; e、粗車1:4外錐為φ112.54,軸向長度車至14,右端倒角1.5x45; f、其余倒角2x45。 臥式車床 6 熱處理 調質 HRC20—25,彎曲<0.6。 7 深孔鉆 一次裝夾車: φ70車至φ72(+0.12,-
53、0.12) φ100f6車至φ102(+0.087,-0.087); 鉆、鏜通孔φ52至尺寸,孔口到3x60(+0.062,-0.062)′。 保證孔與外圓同心<0.10。 深孔鉆床 8 半精車 車左端面見光。 以左端孔、右端外圓為基準車: a、 φ70車至φ71(+0.074,+0.046); b、φ100f6車至φ101(+0.14,+0.087) c、φ83g5車至φ84(+0.087,+0.054); d、其余各外圓留余量1—1.5。 倒頭,卡盤與中心架裝夾車: a、φ170及1:4外錐留余量1—1.5,倒角; b、右端錐孔(莫氏
54、6號)大端口尺寸車至φ62.3-0.1, 錐面接觸50%,孔口倒角3x60(0,-0.20)。 c、φ57車至尺寸。 卡盤與中心架裝夾車: 車左端錐孔留余量0.50—0.60。錐面接觸60%,孔口倒3x60(0,-0.20)。 臥式車床 C620B 9 精車 a、車右端面,保證總長; b、φ170外圓車至φ170(+0.08,+0.05); c、1:4外錐留余量0.60—0.80,肩面留余量0.15—0.20,倒角;φ103車至尺寸; d、其余各<Ra1.6各外圓留磨量0.2—0.4; e、車槽、倒角; f、軸向尺寸:423+0.76、295-
55、0.61、108+0.23、分別車至423.7+0.76、295.2-0.61、108.2+0.23; g、103+0.14右端Ra1.6留磨量0.5—0.6; h、φ105h8右肩面留磨量0.15; k、其余軸向尺寸車成; l、精車三處1:12外錐: 小端尺寸分別車至:φ80.9+0.2、φ83.9+0.2、φ100.9+0.2。 數控車床 CSK6163 10 外磨 φ170外圓磨至φ170(+0.040,+0.025); φ100f6磨至φ100.6(+0.035,0.022); φ83g5、φ83h6至φ83.6(+0.035,0
56、.022); 芯軸:ZF0020A- 外圓磨床 11 鉆大端面各孔 鉆、鉸4—φ23+0.05孔至尺寸; 鉆2-M10底孔,锪2-φ10。 鉆M8底孔、擴、鉸φ19H9至尺寸,攻M8。 鉆模: 塞規(guī):φ23 φ19H9 鉆床Z55 12 熱處理 按圖要求高頻: 外圓6處G50,孔1處G50; 可將φ100.333及以右端部分在鹽爐淬火; 回火后將螺絲—M105.x1.5-6h退火。 13 鉗 精鉸4—φ23 ,φ19H9。 校攻M8,M10; 塞規(guī):φ23、φ19H9 鉆床Z55 14 外磨 磨右端平面及1:4肩面見光,1:4
57、外錐面留磨量0.25—0.30; 粗磨<Ra2.5各外圓留磨量0.25—0.30; φ105h8右肩面見光; 粗磨三處1:12外錐面,環(huán)規(guī)左端面距1:4外錐肩面軸向尺寸分別至426+0.76、298-0.61、111+0.23 外圓磨床 15 銑 銑三處鍵槽至圖樣要求。 請勿夾傷已加工面。工序圖見附圖二 銑床X25 16 外磨 找正外圓↑0.015: 磨1:4錐度肩面; 磨φ170見光; 半精磨三處1:12外錐面,環(huán)規(guī)左端面距1:4肩面分別至423.9+0.8、295.9-0.7、118.9+0.25; 半精磨Ra1.6及以上各外圓留磨
58、量0.05—0.07; M80x1.5磨至φ80(-0.10,-0.12); M105x1.5磨至φ105(-0.10,-0.12); M115x1.5磨至φ115(-0.10,-0.12); 環(huán)規(guī): 專用組合磨床 17 精車 a、刻基準線; b、精車左端內錐孔1:20至尺寸,砂光;精車孔口3x60倒角,砂光。 C、精車右端內錐孔1:20留磨量0.3—0.35,接觸面≥60%偏近大端,精車孔口倒角R3,砂光。 數控車床 CSK6163 18 熱處理 時效,油溫120C,24小時。 19 鉗 清理各部。 20 外
59、磨 精磨Ra1.6以上各外圓至圖樣要求; 精磨三處1:12外錐面至圖樣要求; 精磨1:4外錐面至圖樣要求。 專用組合磨床 21 內磨 精磨右端莫氏6號錐孔至圖樣要求。 專用主軸錐孔磨床 22 精車 找正外徑↑0.015內: a、與螺母配車兩處螺紋M80x1.5-6h、M100x1.5-6h端面跳動≤0.025; b、與螺母配車M105x1.5-6h至尺寸; c、車槽保證軸向尺寸103.5+0.14; d、修車各處倒角,砂光 e、修車空刀槽至尺寸。 (光亮) 工序圖見附圖三 臥式車床 23 檢 按技術條件檢驗各項合格。
60、 24 鉗 涂油防銹。 本次設計中: 粗車精度達到IT11-13; 半精車精度達到IT8-9; 精車精度達到IT6-7; 銑精度達到IT9-10; 深孔鉆精度達到IT8-9; 粗磨精度達到IT8-9; 半精磨精度達到IT7-8; 精磨精度達到IT6-7; 第四章 結 論 通過設計精密主軸工藝流程,深切體會到,它是我以后設計的基礎。本次設計以主軸的工藝流程為主線,主要介紹了主軸的工藝特點及性質。并在研究主軸加工過程中涉及到夾具、量具、車
61、刀以及一些加工方法。此外關于軸類的公差與配合也有介紹。 本次設計使我對主軸工藝有了一個總體的了解和把握。在設計中,通過翻閱資料,也對夾具、刀具、量具有了系統(tǒng)的認識,在一定程度上認識到,設計是一個很嚴謹的過程。從毛坯的選擇、工件的裝夾定位、刀具夾具的選擇、到工序的安排、熱處理的時效,都不依賴與個人的經驗和技術。要注意必須理論聯(lián)系實際,在實際中總結理論,切忌死搬硬套,應該具體問題具體分析,從多方面、多角度、多層次去完成一次設計! 謝 辭 本次設計是在指導老師的悉心指導下完成的。康老師為論文課題的研究提出了許多指導性的意見,為論文的撰
62、寫、修改提供了許多具體的指導和幫助。指導老師的嚴謹治學、不斷探索的科研作風,敏銳深邃的學術洞察力,孜孜不倦的敬業(yè)精神,給我留下了深刻的印象,使我受益良多。在本文結束之際,特向我敬愛的導師致以最崇高的敬禮和深深的感謝! 在我撰寫論文期間,得到了機械系機電工程學院多位老師的幫助,在忙碌的工作之余,給予我專業(yè)知識上的指導,而且教給我學習的方法和思路,使我在科研工作及論文寫作過程中不斷有新的認識和提高。在此,我對他們表示由衷的謝意! 通過這次畢業(yè)設計,對所學知識進行了一次系統(tǒng)的綜合考察,感到收獲很大,鍛煉了獨立思考的能力,學會了如何分析問題解決問題。同時使自己在設計中提高了自己分析問題,解
63、決問題的能力,為自己今后走向工作崗位打下一個結實的基礎,使自己掌握了又一有利工具,為以后激烈的工作競爭中增強實力 。同時在這次設計中,我也發(fā)現(xiàn)自己的不足。這次畢業(yè)設計的時間短,任務重,缺乏理論和實驗基礎,再加上我們的能力有限,在設計中難免有考慮不周之處,還有望于實際調試中不斷完善自己。這將會是我今后努力和學習的方向。導師在設計過程中給予了我關鍵性的指導與幫助。我再一次表示衷心的感謝! 衷心的感謝給予建議和幫助的各位老師! 參考文獻 1.徐嘉元、曾家駒主編. 機械制造工藝學(含機床夾具設計). 北京:機械 工業(yè)出版社,2006
64、 2. 徐圣群主編. 簡明機械加工工藝手冊. 上海:上海科學技術出版社,1991 3.李洪主編. 機械加工工藝手冊. 北京:北京出版社,1990 4.劉友才、肖繼德主編. 機床夾具設計. 北京:機械工業(yè)出版社,1992 5.劉守勇主編. 機械制造工藝與機床夾具. 北京:機械工業(yè)出版社,2003 6.顧崇銜等主編. 機械制造工藝學. 陜西:陜西科學技術出版社,1985 7.黃鶴汀、王芙蓉、趙春久主編. 金屬切削機床. 北京:機械工業(yè)出版社, 2006 8.劉飛主編. 互換性與測量技術基礎. 北京:機械工業(yè)出版社,2004 9.陸劍中、孫家寧主編. 金屬切削原理與刀具
65、. 北京:機械工業(yè)出版社, 2005 10. 余強、王建平、辛會珍等編著. AutoCAD2005 機械制圖經典事例教程. 北京:機械工業(yè)出版社,2005 11.王信義等主編. 機械制造工藝學. 哈爾濱;哈爾濱工業(yè)大學出版社, 1990 12.吳天林,段正澄主編. 機械加工系統(tǒng)自動化. 北京;機械工業(yè)出版社, 1991 13.李碩根等主編. 互換性與測量技術基礎. 北京;中國計量出版社,1998 14.陳立德主編. 機械設計基礎. 北京;高等教育出版社,2002 15.蔡安江主編.機械制造技術基礎. 北京;機械工業(yè)出版社,2007
- 溫馨提示:
1: 本站所有資源如無特殊說明,都需要本地電腦安裝OFFICE2007和PDF閱讀器。圖紙軟件為CAD,CAXA,PROE,UG,SolidWorks等.壓縮文件請下載最新的WinRAR軟件解壓。
2: 本站的文檔不包含任何第三方提供的附件圖紙等,如果需要附件,請聯(lián)系上傳者。文件的所有權益歸上傳用戶所有。
3.本站RAR壓縮包中若帶圖紙,網頁內容里面會有圖紙預覽,若沒有圖紙預覽就沒有圖紙。
4. 未經權益所有人同意不得將文件中的內容挪作商業(yè)或盈利用途。
5. 裝配圖網僅提供信息存儲空間,僅對用戶上傳內容的表現(xiàn)方式做保護處理,對用戶上傳分享的文檔內容本身不做任何修改或編輯,并不能對任何下載內容負責。
6. 下載文件中如有侵權或不適當內容,請與我們聯(lián)系,我們立即糾正。
7. 本站不保證下載資源的準確性、安全性和完整性, 同時也不承擔用戶因使用這些下載資源對自己和他人造成任何形式的傷害或損失。