支撐板沖壓成形工藝及模具研究設計
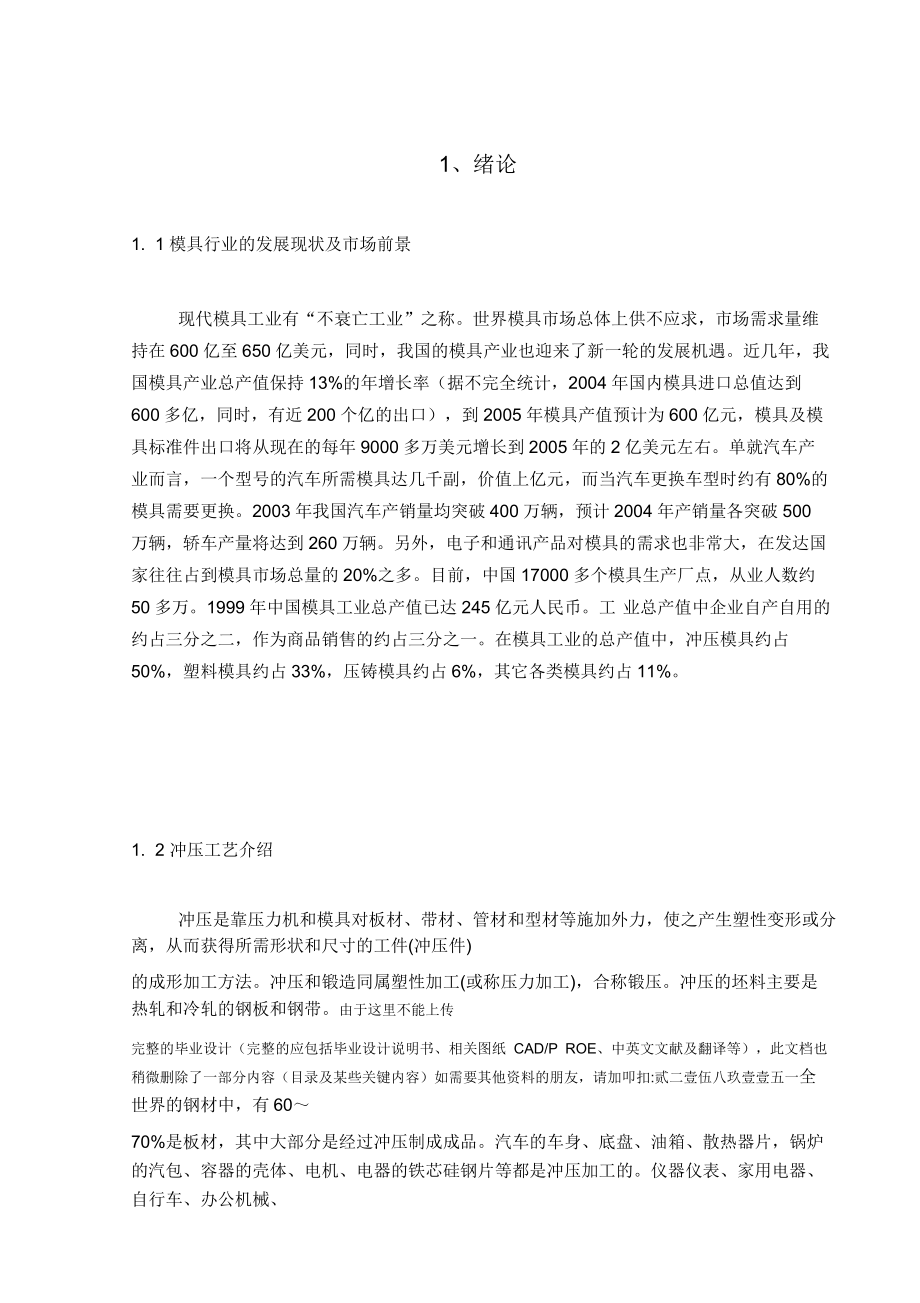


《支撐板沖壓成形工藝及模具研究設計》由會員分享,可在線閱讀,更多相關《支撐板沖壓成形工藝及模具研究設計(30頁珍藏版)》請在裝配圖網(wǎng)上搜索。
1、 1、緒論 1. 1模具行業(yè)的發(fā)展現(xiàn)狀及市場前景 現(xiàn)代模具工業(yè)有“不衰亡工業(yè)”之稱。世界模具市場總體上供不應求,市場需求量維持在600億至650億美元,同時,我國的模具產業(yè)也迎來了新一輪的發(fā)展機遇。近幾年,我國模具產業(yè)總產值保持13%的年增長率(據(jù)不完全統(tǒng)計,2004年國內模具進口總值達到600多億,同時,有近200個億的出口),到2005年模具產值預計為600億元,模具及模具標準件出口將從現(xiàn)在的每年9000多萬美元增長到2005年的2億美元左右。單就汽車產業(yè)而言,一個型號的汽車所需模具達幾千副,價值上億元,而當汽車更換車型
2、時約有80%的模具需要更換。2003年我國汽車產銷量均突破400萬輛,預計2004年產銷量各突破500萬輛,轎車產量將達到260萬輛。另外,電子和通訊產品對模具的需求也非常大,在發(fā)達國家往往占到模具市場總量的20%之多。目前,中國17000多個模具生產廠點,從業(yè)人數(shù)約50多萬。1999年中國模具工業(yè)總產值已達245億元人民幣。工 業(yè)總產值中企業(yè)自產自用的約占三分之二,作為商品銷售的約占三分之一。在模具工業(yè)的總產值中,沖壓模具約占50%,塑料模具約占33%,壓鑄模具約占6%,其它各類模具約占11%。 1. 2 沖壓工藝介紹
3、 沖壓是靠壓力機和模具對板材、帶材、管材和型材等施加外力,使之產生塑性變形或分離,從而獲得所需形狀和尺寸的工件(沖壓件) 的成形加工方法。沖壓和鍛造同屬塑性加工(或稱壓力加工),合稱鍛壓。沖壓的坯料主要是熱軋和冷軋的鋼板和鋼帶。由于這里不能上傳 完整的畢業(yè)設計(完整的應包括畢業(yè)設計說明書、相關圖紙 CAD/P ROE、中英文文獻及翻譯等),此文檔也稍微刪除了一部分內容(目錄及某些關鍵內容)如需要其他資料的朋友,請加叩扣:貳二壹伍八玖壹壹五一全世界的鋼材中,有 60~ 70%是板材,其中大部分是經過沖壓制成成品。汽車的車身、底盤、油箱、散熱器片,鍋爐的汽包、容器的殼體
4、、電機、電器的鐵芯硅鋼片等都是沖壓加工的。儀器儀表、家用電器、自行車、辦公機械、 生活器皿等產品中,也有大量沖壓件。 沖壓件與鑄件、鍛件相比,具有薄、勻、輕、強的特點。沖壓可制出其他方法難于制造的帶有加強筋、肋、起伏或翻邊的工件,以提高其剛性。由于采用精密模具,工件精度可達微米級,且重復精度高、規(guī)格一致,可以沖壓出孔、凸臺等。 冷沖壓件一般不再經切削加工,或僅需要少量的切削加工。熱沖壓件精度和表面狀態(tài)低于冷沖壓件,但仍優(yōu)于鑄件、鍛件,切削加工量少。 沖壓是高效的生產方法,采用復合模,尤其是多工位級進模,可在一臺壓力
5、機上完成多道沖壓工序,實現(xiàn)由帶料開卷、矯平、沖裁到成形、精整的全自動生產。生產效率高,勞動條件好,生產成本低,一般每分鐘可生產數(shù)百件。 1. 3沖壓工藝的種類 沖壓主要是按工藝分類,可分為分離工序和成形工序兩大類。分離工序也稱沖裁,其目的是使沖壓件沿一定輪廓線從板料上分離,同時保證分離斷面的質量要求。成形工序的目的是使板料在不破坯的條件下發(fā)生塑性變形,制成所需形狀和尺寸的工件。在實際生產中,常常是多種工序綜合應用于一個工件。沖裁、彎曲、剪切、拉深、脹形、旋壓、矯正是幾種主要的沖壓工藝。 在實際生產中,常用與沖壓過程近似的工藝性試驗,如拉
6、深性能試驗、脹形性能試驗等檢驗材料的沖壓性能,以保證成品質量和高的合格率。 模具的精度和結構直接影響沖壓件的成形和精度。模具制造成本和壽命則是影響沖壓件成本和質量的重要因素。模具設計和制造需要較多的時間,這就延長了新沖壓件的生產準備時間。 模座、模架、導向件的標準化和發(fā)展簡易模具(供小批量生產)、復合模、多工位級進模(供大量生產),以及研制快速換模裝置,可減少沖壓生產準備工作量和縮短準備時間,能使適用于減少沖壓生產準備工作量和縮短準備時間,能使適用于大批量生產的先進沖壓 技術合理地應用于小批量多品種生產。 沖壓設備除了厚板
7、用水壓機成形外,一般都采用機械壓力機。以現(xiàn)代高速多工位機械壓力機為中心,配置開卷、矯平、成品收集、輸送等機械以及模具庫和快速換模裝置,并利用計算機程序控制,可組成高生產率的自動沖壓生產線。 在每分鐘生產數(shù)十、數(shù)百件沖壓件的情況下,在短暫時間內完成送料、沖壓、出件、排廢料等工序,常常發(fā)生人身、設備和質量事故。因此,沖壓中的安全生產是一個非常重要的問題。 1. 4沖壓行業(yè)阻力和障礙與突破 阻力一:機械化、自動化程度低 美國 680條沖壓線中有 70%為多工位壓力機,日本國內 250條生產線有 32%為多工位壓力機,而這種代表當今國際水
8、平的大型多工位壓力機在我國的應用卻為數(shù)不多;中小企業(yè)設備普遍較落后,耗能耗材高,環(huán)境污染嚴重;封頭成形設備簡陋,手工操作比重大;精沖機價格昂貴,是普通壓力機的 5~10 倍,多數(shù)企業(yè)無力投資阻礙了精沖技術在我國的推廣應用;液壓成形,尤其是內高壓成形,設備投資大,國內難以起步。 突破點:加速技術改造 要改變當前大部分還是手工上下料的落后局面,結合具體情況,采取新工藝,提高機械化、自動化程度。汽車車身覆蓋件沖壓應向單機連線自動化、機器人沖壓生產線,特別是大型多工位壓力機方向發(fā)展。爭取加大投資力度,加速沖壓生產線的技術改造,使盡早達到當今國際水平。。應加速發(fā)展
9、數(shù)字化柔性成形技術、液壓成形技術、高精度復合化成形技術以及適應新一代輕量化車身結構的型材彎曲成形技術及相關設備。同時改造國內舊設備,使其發(fā)揮新的生產能力。 阻力二:生產集中度低 許多汽車集團大而全,形成封閉內部配套,導致各企業(yè)的沖壓 件種類多,生產集中度低,規(guī)模小,易造成低水平的重復建設,難以滿足專業(yè)化分工生產,市場競爭力弱;摩托車沖壓行業(yè)面臨激烈的市場競爭,處于“優(yōu)而不勝,劣而不汰”的狀態(tài);封頭制造企業(yè)小而散,集中度僅 39.2%。 突破點:走專業(yè)化道路 迅速改變目前“大而全”、“散
10、亂差”的格局,盡快從汽車集團中把沖壓零部件分離出來,按沖壓件的大、中、小分門別類,成立幾個大型的沖壓零部件制造供應中心及幾十個小而專的零部件工廠。通過專業(yè)化道路,才能把沖壓零部件做大做強,成為國際上有競爭實力的沖壓零部件供應商。 阻力三:沖壓板材自給率不足,品種規(guī)格不配套 目前,我國汽車薄板只能滿足 60%左右,而高檔轎車用鋼板,如高 強 度 板 、 合 金 化 鍍 鋅 板 、 超 寬 板 ( 16 50 mm 以 上 ) 等 都 依 賴 進 口 。 突破點:所用的材料應與行業(yè)協(xié)調發(fā)展 汽車用鋼板的品種應更趨向合理,朝著高強、高耐蝕和各種規(guī)格的薄
11、鋼板方向發(fā)展,并改善沖壓性能。鋁、鎂合金已成為汽車輕量化的理性材料,擴大應用已勢在必行。 阻力四:科技成果轉化慢先進工藝推廣慢 在我國,許多沖壓新技術起步并不晚,有些還達到了國際先進水平,但常常很難形成生產力。先進沖壓工藝應用不多,有的僅處于試用階段,吸收、轉化、推廣速度慢。技術開發(fā)費用投入少,導致企業(yè)對先進技術的掌握應用慢,開發(fā)創(chuàng)新能力不足,中小企業(yè)在這方面的差距更甚。目前,國內企業(yè)大部分仍采用傳統(tǒng)沖壓技術,對下一代輕量化汽車結構和用材所需的成形技術缺少研究與技術儲備 。 突破點:走產、學、研聯(lián)合之路 我國與歐、美、日等
12、相比,存在的最大的差距就是還沒有一個產、學研聯(lián)合體,科研難以做大,成果不能盡快轉化為生產力。所以應圍繞大型開發(fā)和產業(yè)化項目,以高校和科研單位為技術支持, 企業(yè)為應用基地,形成產品、設備、材料、技術的企業(yè)聯(lián)合實體,形成既能開發(fā)創(chuàng)新,又能迅速產業(yè)化的良性循環(huán)。 阻力五:大、精模具依賴進口 當前,沖壓模具的材料、設計、制作均滿足不了國內汽車發(fā)展的需要,而且標準化程度尚低,大約為 40%~45%,而國際上一般在70%左右 。 突破點:提升信息化、標準化水平 必須用信息化技術改造模具企業(yè),發(fā)展重點在于大力推廣CAD/C
13、AM/CAE一體化技術,特別是成形過程的計算機模擬分析和優(yōu)化技術(CAE)。加速我國模具標準化進程,提高精度和互換率。力爭 2005 年模具標準件使用覆蓋率達到 60%,2010年達到 70%以上基本滿足市場需求。 阻力六:專業(yè)人才缺乏 業(yè)內掌握先進設計分析技術和數(shù)字化技術的高素質人才遠遠不能滿足沖壓行業(yè)飛速發(fā)展的需要,尤其是摩托車行業(yè)中具備沖壓知識和技術和技能的專業(yè)人才更為缺乏且大量外流。另外,眾多合資公司由外方進行工程設計,掌握設計權、投資權,我方沖壓技術人員難以真正掌握沖壓工藝的真諦。 突破點:提高行業(yè)人員素質 隨著時代的進步和技術
14、的發(fā)展,國外的一些掌握和能運用新技術的人才如模具結構設計、模具工藝設計、高級鉗工及企業(yè)管理人才,他們的技術水平比較高.故人均產值也較高.我國每個職工平均每年創(chuàng)造模具產值約合 1 萬美元左右,而國外模具工業(yè)發(fā)達國家大多 15~20萬美元,有的達到 25~30萬美元。 國外先進國家模具標準件使用覆蓋率達 70%以上,而我國才達到45%這是一項迫在眉睫的任務,又是一項長期而系統(tǒng)的任務。振興我國沖壓行業(yè)需要大批高水平的科技人才,大批熟悉國內外市場、具有現(xiàn)代管理知識和能力的企業(yè)家,大批掌握先進技術、工藝的高級技能人才。要舍得花大力氣,有計劃、分層次地培養(yǎng)。
15、 2、支撐板工藝分析 零件名稱:支撐板 生產批量:大批量 材料:35 料 厚 : 2mm 零件圖:見圖 零 件 圖 2. 1工藝分析 此彎曲件為 V 型彎曲,零件圖如圖所示。圖中的尺寸公差為未注公差,在處理這類零件公差等級時均按 IT14級要求
16、。彎曲圓角半 徑 r =2 ,均 大 于 最 小 彎 曲 半 徑 :( rmin 0.8 0.8 2 1.6 )故此件形狀, t mm 尺寸,精度均滿足彎曲工藝的要求,可用彎曲工藝進行加工。彎曲后再采用落料、沖孔。沖裁件內外形所能達到的經濟精度為 IT11— I T1 4 , 孔 中 心 與 邊 緣 距 離 尺 寸 公 差 為 ± 0. 5 mm, 將 以 上 精 度 與 零 件 的精度要求相比較,該零件的精度要求能夠在沖裁加工中得到保證,其他尺寸標注、生產批量等情況也均符合沖裁的工藝要求。 2. 2工藝方案的確
17、定 該零件所需的沖壓工序為彎曲、沖孔好落料??蓴M定以下三種方 案 : 方案一:采用簡單模分三次加工,即彎曲—落料—沖孔。 方案二:彎曲、落料、沖孔復合模。 采用方案一,模具結構簡單,但需要三道工序、三套模具才能完成零件的加工,生產效率較低,難以滿足零件大批量生產的需求.由于零件結構簡單,為提高生產效率,主要應采用復合沖裁或級進沖裁方式,方案二和方案三更具優(yōu)越性。 采用方案二,需要一套模具,沖壓件的形位精度和尺寸易于保證,且生產效率也高。 盡管模具結構較方案一復雜,單零件的幾何尺寸相對簡單,模具制造并
18、不困難。 通過對兩種方案的分析比較,該零件的沖壓生產采用方案二的復合膜為佳。 2. 3彎曲工藝計算 彎曲件展開長度的計算 當 彎 曲 圓 角 半 徑 較 小 ( r < 0. 5t ) 時 , 根 據(jù) 毛 坯 與 制 件 等 體 積 法計 算 , 當 彎 曲 圓 角 半 徑 較 大 ( r > 0. 5 t ) 時 , 根 據(jù) 中 性 層 長 度 不 變 原 理 計 算 。 因為 R=2>0. 5×2,屬于圓角半徑較大的彎曲件。所以彎曲件的展開長度按直邊區(qū)與圓角
19、 區(qū)分段進行計算。視直邊區(qū)在彎曲前后長度不變,圓角區(qū)展開按彎曲前后中性層長度不變條件進行計算。 由 于 R/ t = 2/ 2= 1 , 查 表 (《 沖 壓 工 藝 與 模 具 設 計 》 P97 表 3. 4 ) 得 位 移 系 數(shù) x =0. 4 2 變形區(qū)中性層曲率半徑按(《沖壓工藝與模具設計》P97表 3. 7) 公式計算 r kt 得 : r kt 2 0.42 2 2.84mm 毛坯尺寸(中性層長度) L z l A 1 8 0 其 中 A 1 8 0 1
20、80 A 1 180 = 180 110 180 = 70 3.14 180 = 3. 4 68mm (中性層圓角部分的長度) 2.84 180 130 A 2 180 = 50 3.14 2.84 180 =2. 47 7mm 該零件的展開長度為 L z 55 36 26 46 33 3.468 2 2.477 2 207.85mm 以 上 各 式
21、 中 ― ― ― 中 性 層 曲 率 半 徑 , mm; k ― ― ― 中 性 層 位 置 系 數(shù) , 查 表 得 k =0. 4 2, mm; A― ― ― 中 性 層 圓 角 部 分 的 長 度 , mm; t ― ― ― 材 料 彎 曲 厚 度 , mm; L z ― ― ― 彎 曲 件 的 展 開 長 度 , mm; β ― ― ― 彎 角 , ( ° ) 。 2. 4彎曲工作部分尺寸計算 2. 4. 1凸模圓角半徑計算 ① 當 彎 曲 件 r >1 0 時 , 凸 模 圓 角 半
22、 徑 rt 為 rt r sr 1 3 Et ② 當 彎 曲 件 r 較 小 時 , 凸 模 圓 角 半 徑 為 rt r ( 但 ) rtrm i n 此工件的彎曲圓角半徑較小但不小于工件材料所允許的最小彎曲 半 徑 rmin 0.6t 0.6 2 1.2mm ,故 凸 模 圓 角 半 徑 ra 可 取 彎 曲 件 的 內 彎 曲 半 徑 r =2mm。 2. 4. 2凹模圓角半角計算 凹模圓角半徑不能過小,以免增加彎曲力,擦傷工
23、件表面。凹 模 圓 角 半 徑 ra 一 般 按 材 料 的 厚 度 來 取 。 t 2mmra ( 3 ~ 6 ) t t ( 2 ~ 4 ) mmra ( 2 ~ 3) t t 4 mmra 2t 該 工 件 厚 度 為 2 mm, 故 凹 模 半 徑 ra 2t 2 2 4 mm 2. 4. 3凹模工作部分深度的設計計算。 凹模工作部分的深度將決定板料的進模深度,同時也影響到彎曲件直邊的平直度,對工件的尺寸精度造
24、成一定的影響,查表 3. 12 得 凹 模 的 底 部 最 小 厚 度 h 0 4mm 因 此 , 凹 模 工 作 部 分 深 度 h =3 8 +2 +4 =4 4mm 2. 4. 4凸凹模間隙的確定 彎曲模的凸凹模間隙是指單邊間隙 Z/2,V型件彎曲時,凸凹模的間隙時是靠調整壓力機的閉合高度來控制的,不需要在設計,制造模具時確定。在模具設計中,必須考慮到模具閉合時,模具工作部分與工件能緊密貼合,以保證彎曲質量。 ① 一 般 情 況 下 , Z/ 2 =t + 1 + Ct ② 工 件 精 度 要 求 較 高 時 , Z/ 2
25、= t 以 上 各 式 中 t ― ― 工 件 材 料 厚 度 , mm; C―― 間隙系數(shù); 1 ― ― 材 料 厚 度 的 正 偏 差 , mm。 2. 5彎曲件回彈值的計算 小 變 形 程 度 ( r / t ≥ 1 0 ) 時 , 回 彈 大 , 先 計 算 凸 模 圓 角 半 徑 , 再計 算 凸 模 角 度 ; 大 變 形 程 度 ( r / t < 5) 時 , 卸 載 后 圓 角 半 徑 小 , 僅 考慮 彎 曲 中 心 角 的 回 彈 變 化 。 彎 曲 時 , 彎 曲 中 心 角 為 110 o , 查 相
26、關 手冊 , 取 回 彈 角 為 3 o ; 彎 曲 中 心 角 為 130 o , 查 相 手 冊 , 取 回 彈 角 4 o 。 2. 6彎曲力計算 V形件彎曲力 0.6K bt2 b F自 t r = 0.6 1.3 30 2 2 (490 - 637) 2 2 =( 11466 ~ 14905. 8) N 校正彎曲的彎曲力 P校 Ap =1 6 0×30×70 =3 3 6
27、000 N (無論工件形狀如何) F自――沖壓行程結束時自由彎曲的彎曲力(N); K――系數(shù),一般取 1. 3; b ― ― 彎 曲 件 寬 度 ( mm) ; t ― ― 彎 曲 件 材 料 寬 度 ( mm); b ― ― 彎 曲 件 材 料 的 抗 拉 強 度 ( MP); r ― ― 彎 曲 件 的 內 彎 曲 半 徑 ( mm); F校――校正彎曲力(N); A― ― 校 正 部 分 投 影 面 積 ( mm 2 ); p ― ― 單 位 面 積 校 正 力 ( MP), 查
28、表 得 。 2. 7 沖 孔 Φ 10 mm 凸 、 凹 刃 口 尺 寸 的 計 算 由于制件結構簡單,精度要求不高,所以采用凸模和凹模分開加工的方法制作凸、凹模。其凸、凹模刃口尺寸計算如下: 查表 2. 5得凸、凹模制造公差: 凸 0.020mm 凹 0.020 mm 校核查表 2. 5得凸、凹模制造公差 Z max Z min 0.114mm 而 凸 凹 0.045mm 滿 足 Z m a x Z m i n 凸 凹的條件 查 表 2. 6得:IT
29、14 級 時 磨 損 系 數(shù) x= 0. 5 ,0.2 d凸 d minx 0 凸 = ( 1 0+0. 5×0. 2) 0 0.02 =10. 1 0 0 .02 mm d凹 d凸 Z min 凹 0 = ( 1 0. 1+ 0. 2 46 ) 0 0.02 = 10. 346 0 0.02 mm 2. 8外形落料凸、凹刃口尺寸的計算 由于制件結構簡單,精度要求不高,所以采用凸模和凹模分開加工的方
30、法制作凸、凹模。其凸、凹模刃口尺寸計算如下: 查表 2. 5得凸、凹模制造公差: 凸 0.020mm 凹 0.020 mm 校核查表 2. 5得凸、凹模制造公差 Z max Z min 0.114mm 而 凸 凹 0.045mm 滿 足 Z m a x Z m i n 凸 凹的條件 查表 2. 6得:I T14 級 時 磨 損 系 數(shù) x= 0. 5 ,0.2 D 凹 D maxx 凹 0 = ( 166. 4- 0. 5×0. 2) 00.02 = 16 6. 3 00.
31、02 mm D 凸 D 凹 Z min 0 凸 =( 1 66. 3- 0. 24 6 ) 00.02 =1 6 6. 054 0 0. 02 mm 2. 9沖壓力計算 落 料 力 F落 Lt b 60 2 500 60000N 沖 孔 力 F沖 Lt b 10 3.14 2 500 31400N 沖孔時的推件力 F推 nK 推 F沖 取直筒形刃口的凹模刃口形式,由表 2. 2 1 查 得 h= 6mm, 則
32、n= h / t =3 , 查表2.7 得,K推 0.05 F推 nK 推 F沖 3 0.05 31400 4710N 落料時的卸料力 查表2.7 取 K 卸 0.03 F卸 K 卸F落 0.03 60000 1800N 2. 10 壓力中心的計算 由于該件都對稱,故選其幾何中心為壓力中心 2. 11 橡皮的選擇 橡皮允許承受的負荷較彈簧大,且安裝調試方便,在沖裁模中廣泛應用。 ①橡皮的平面尺寸 平面尺寸按其所產生的壓力
33、 F計算 F=Sq 所 以 F 12000 S 11320 q 1.06 橡皮壓縮量 10 15 20 2 5 3 0 35 / % 單位壓力/ 0.26 0.50 0.70 1.06 1.52 2.10 MPa R S 11320 60mm π 3.14 R――橡皮半徑; S―― 橡皮的橫截面子; q ― ― 與 橡 皮 的 壓 縮 量 有 關 單 位 壓 力 , 按 橡 皮 的 壓 縮 特 性 曲
34、 線選 用 。 ② 橡皮的高度 橡皮的高度必須滿足工藝要求與模具結構空間要求,并考慮橡皮的壽命。 ⑴橡皮最大壓縮量不宜超過自由高度 H的 35%~45%。 ⑵橡皮裝在模具上,一般應預先壓縮(10%~15%)H,使預壓的壓力達到所需要的卸料力。 ⑶壓縮工作行程為 H工作 (25%~30%)H 橡皮的自由高度為 H= H 工作 / ( 0. 2 5 ~ 0. 3 0) =20/ ( 0. 25 ~ 0. 3 0) = ( 6 6. 7 ~ 8 0) mm 取 H=7 0 mm
35、 式中 H工作――橡皮壓縮工作行程,根據(jù)模具結構可知; H――橡皮的自由高度。 上式中的高度校核: 高度校核:H=0. 65D 3、模架與壓力機的選用 3. 1模架的選擇 根據(jù)上述分析,本零件的沖壓包括彎曲、沖孔和落料兩三個工序,可采用復合模具,利用彈性卸料裝置,卸料可靠,便于操作。工件留在落料凹??锥粗校脧椥孕读涎b置卸料,落料廢料在落料凸凹模外側自由落下;而沖孔廢料則可以在下模座中開設通槽,使廢料從孔洞中落下。由于在該模具中是先彎曲后
36、落料和沖孔的。 所以彈性元件還應具有壓料的作用,應選用彈性卸料板來卸下工件。 因是大批量生產,采用手動送料方式,從前向后送料。 因采用的是復合模,所以直接用擋料銷和導料銷即可。 為確保零件的質量及穩(wěn)定性,故選用導柱、導套導向。由于該零件導向尺寸較小,且精度要求不是太高,所以宜采用后側導柱模架 。 選擇模架,選擇后側導柱模架,315 × 250 閉合高度 300~350上模座 315×200×30 下模座 315×250×50。 模具閉合高度 H閉合 h 上模座 h 墊板 h凸模固定板 h橡皮
37、 h 彎曲凸模 h凸凹模 h下模座 =35+30+38+60+72+55+50 =3 4 0mm 3. 2壓力機的選擇 選擇型號為 JB23-63 的開式雙柱可傾壓力機滿足使用要求。其主要技術參數(shù)如下: 公稱壓力: 630KN 滑 塊 行 程 :
38、 10 0mm 滑 塊 行 程 次 數(shù) ( 次 / mi n ): 4 0 最大閉合高度: 5 00mm 封閉高度調節(jié)量: 80mm 工作臺尺寸: 570×860 墊塊尺寸: 80 模柄孔尺寸: Φ 50×85 最大傾斜角度: 25 3. 3壓力機的校核 1. 模具閉合高度是指模具工作行程終了時,上模座上平面至下模座下平面之間的距離。 H= 34 0mm< H max - H 1 = 500 - 8 0= 42 0mm 滿足要求。 2. F總 F沖 F落 F自 F
39、校 = 3140 0+6 0000 +14 90 5+33 600 0 = 4423 05 N F壓力 600000N (1.2 1.3)F總 (1.2 1.3) 442305 530766N 574996N 滿足使用要求 3. 工作臺尺寸: 570×860 模具尺寸:315×250 4. 模柄孔尺寸: Φ50×85 模柄安裝尺寸:Φ45×55 4、模具主要零部件的設計。 4. 1沖孔Φ10凸模設計。 由于凸模較長,為了增加凸模的強度
40、與剛度,凸模非工作部分應 制 成 逐 漸 增 大 的 多 級 形 式 , 凸 模 固 定 板 厚 度 去 3 8mm, 凸 模 結 構 根據(jù)結構上的需要來確定。 L h凸模固定板 h 橡皮 h彎曲凸模 26 = 38 +60 +1 10- 26 = 19 2 mm ① 承壓應力校核 沖裁時凸模承受的壓應力 p , 必 須 小 于 凸 模 材 料 強 度 所 允 許 的 壓 應 力 p F p A p 對于圓形凸模,由上式可得 d 4
41、 即 4 t t dmin p p dmin 4 450 2 1200 3.6 mm 凸模淬火到 58~62HRC時 p ( 10 0 0 ~ 16 00 ) MPa ②失穩(wěn)彎曲應力檢驗 圓形凸模 L max 270 d 2 100 270 152.5mm F 31400 滿足設計要求 4. 2落料凹模的設計 落料凹模內部有彈性卸料裝置,
42、所以凹模刃口應采用直臂形刃口 , 查 表 得 ,取 刃 口 高 度 h =6 mm,由 于 該 模 具 選 用 組 合 式 凹 模 。 根 據(jù)模具結構選用一組對稱的。沖裁時凹模承受沖裁力合側向擠壓力的作用。由于凹模的結構形式方法眾多,受力情況又比較復雜,目前還不能用理論方法精確地把凹模外輪廓尺寸算出來。在 實際生產中,通常根據(jù)沖件的料厚度和沖件的輪廓尺寸,把凹模刃壁至外形邊的距離,按經驗公式來確定。 4. 3凸凹模的設計 再復合模中,至少有一個凸凹模。凸凹模的外緣均為刃口,內外緣之間的壁厚取決于沖裁件的尺寸,從強度考慮,壁厚受最小值限制。對于
43、倒裝復合膜,因孔內會積存廢料,所以最小壁厚要厚一些。凸凹模的最小壁厚一般由經驗數(shù)據(jù)決定。 4. 4凸模固定板的設計 凸模固定板的作用是用來固定凸模的,由于該模具的主要作用是固定用的,因此該零件不需要太高的硬度,故選用經常用的 45鋼來加工該零件,在設計該零件時,要保證上下兩面的平行度要求,且需要保證
44、凸模孔的精度要求。凸模固定板的厚度一般取凹模厚度的 0. 6-0. 8 倍,其平面尺寸可與凹模、卸料板外形尺寸相同,固定 板 的 凸 模 安 裝 孔 與 凸 模 采 用 過 渡 配 合 H7/ m6 、 H7/ n 6, 壓 裝 后 將 凸 模斷面與固定板一起磨平。 4. 5墊板的設計 墊板的作用是直接承受和擴散凸模傳遞的壓力,以降低模座所受的單位壓力,防止模座被壓出凹坑,影響凸模的正常工作。模具中最為常見的是凸模墊板,模具是否加裝墊板要根據(jù)模座所受壓力的大小進行判斷,若模座所受單位壓力大于模座材料的需用壓應力,則 需 加
45、墊 板 。墊 板 外 形 尺 寸 可 與 固 定 板 相 同 ,其 厚 度 一 般 取 3 - 10 mm。墊板材料為 45 鋼,淬火硬度為 43-48HRC。墊 板上下表面應磨平,以保證平行度要求。為了便于模具裝配,墊板上銷釘通過孔直徑可比銷 釘 直 徑 增 大 0. 3 - 0. 5mm。 4. 6模座的設計 上模座用來固定上模部分零件,并同過模柄或螺栓、壓板把上模固定到壓力機滑塊上,同時又起到傳遞并承受沖裁力的作用。下模座用來固定下模部分零件,并通過螺栓,壓板將下模座固定在壓力機工作臺面上,同時起著承受并分散沖裁力的作用。設計模座時
46、一般按照國標規(guī)定的標準模架設計,自行設計時,圓形模座的直徑應 比 凹 模 板 直 徑 大 30 - 7 0mm, 矩 形 模 座 的 長 度 應 比 凹 模 板 長 度 大 4 0- 70 mm。 寬 度 可 以 略 大 于 或 等 于 凹 模 板 的 寬 度 , 模 座 的 厚 度 可 以 參照標準模座,一般為凹模板厚度的 1.0-1. 5 倍。模座材料一般選用鑄鐵,也可以用 Q235、Q255 結構鋼,沖裁力大時也可以選用鑄鋼 ZG3 5 ZG4 5. 4. 7模柄的設計 模柄的作用是使模具的中心線與壓力機的中心線重合,并把沖壓模具零件部
47、分固定在壓力機的滑塊上,常用于 1000KN以下的壓力機上的中、小模具的安裝。此套模具選用壓入式模柄,他與模座孔采用過渡配合,加銷釘以防止轉動,模柄有較高的垂直度和同軸度。 4. 8導柱、導套的選擇 對于生產批量大、要求模具壽命高的模具,一般采用導柱、導套來保證上、下模的導向精度。導柱、導套在模具中
48、主要起導向作用。導柱與導套之間采用間隙配合。根據(jù)沖壓工序性質、沖壓的精度及材料厚度等的不同,其配合間隙也稍微不同。因為本制件的厚度 為 0. 6 mm, 所 以 采 用 H7/ h6 。 5、繪制模具總裝配圖
49、 這是一個后側導柱導向的復合模,橡皮的作用是提供彎曲時所需的壓力,為后來的沖孔落料提供必要的空間,同時也起到了壓料與卸料作 用。由于限位螺釘?shù)淖饔茫鼓1幌拗圃谝欢ǖ幕顒臃秶鷥?,不會因自重而落下,由于沖孔凸模采用階梯結構,有效地保證了凸模的剛度。落料凸模與彎曲凹模做在一起,彎曲后在進行落料,結構簡單,同樣保證了落料凸模與彎曲凹模強度,故不再考慮由于制件的不對稱,而產生的偏移現(xiàn)象。 6、結束語 大學三年的學習即將結束,畢業(yè)設計是其中最后一個實踐環(huán)節(jié)
50、,是對以前所學的知識及所掌握的技能的綜合運用和檢驗。隨著我國經濟的迅速發(fā)展,采用模具的生產技術得到愈來愈廣泛的應用。在完成大學三年的課程學習和課程、生產實習,我熟練地掌握了機械制圖、機械設計、機械原理等專業(yè)基礎課和專業(yè)課方面的知識,對機械制造、加工的工藝有了一個系統(tǒng)、全面的理解,達到了學習的目的。對于模具設計這個實踐性非常強的設計課題,我們進行了大量的實習。經過在新飛電器有限公司、洛陽中國一拖的生產實習,我對于模具特別是塑料模具的設計步驟有了一個全新的認識,豐富了各種模具的結構和動作過程方面的知識,而對于模具的制造工藝更是實現(xiàn)了零的突破。在指導老師的協(xié)助下和在工廠師傅的講解下,同時在現(xiàn)場查閱了很多相關資料并親手拆裝了一些典型的模具實體,明確了模具的一般工作原理、制造、加工工藝。并在圖書館借閱了許多相關手冊和書籍,設計中,將充分利用和查閱各種資料,并與同學進行充分討論,盡最大努力搞好本次畢業(yè)設計。 在設計的過程中,將有一定的困難,但有指導老師的悉心指導和自己的努力,相信會完滿的完成畢業(yè)設計任務。由于學生水平有限,而且缺乏經驗,設計中不妥之處在所難免,肯請各位老師指正。
- 溫馨提示:
1: 本站所有資源如無特殊說明,都需要本地電腦安裝OFFICE2007和PDF閱讀器。圖紙軟件為CAD,CAXA,PROE,UG,SolidWorks等.壓縮文件請下載最新的WinRAR軟件解壓。
2: 本站的文檔不包含任何第三方提供的附件圖紙等,如果需要附件,請聯(lián)系上傳者。文件的所有權益歸上傳用戶所有。
3.本站RAR壓縮包中若帶圖紙,網(wǎng)頁內容里面會有圖紙預覽,若沒有圖紙預覽就沒有圖紙。
4. 未經權益所有人同意不得將文件中的內容挪作商業(yè)或盈利用途。
5. 裝配圖網(wǎng)僅提供信息存儲空間,僅對用戶上傳內容的表現(xiàn)方式做保護處理,對用戶上傳分享的文檔內容本身不做任何修改或編輯,并不能對任何下載內容負責。
6. 下載文件中如有侵權或不適當內容,請與我們聯(lián)系,我們立即糾正。
7. 本站不保證下載資源的準確性、安全性和完整性, 同時也不承擔用戶因使用這些下載資源對自己和他人造成任何形式的傷害或損失。