塑料水杯注塑模具設計
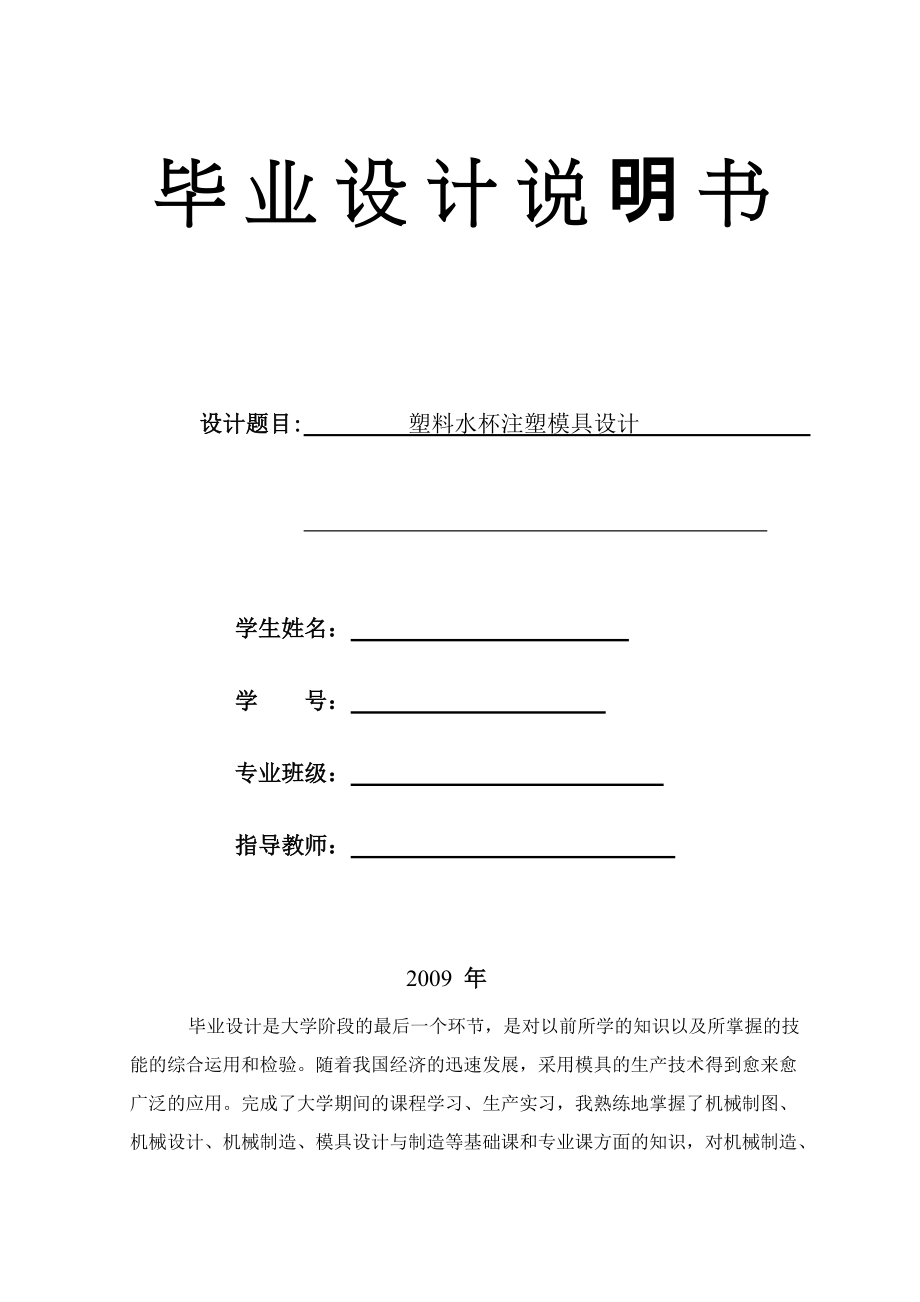


《塑料水杯注塑模具設計》由會員分享,可在線閱讀,更多相關《塑料水杯注塑模具設計(26頁珍藏版)》請在裝配圖網上搜索。
1、 畢業(yè)設計說明書 設計題目: 塑料水杯注塑模具設計 學生姓名: 學 號: 專業(yè)班級: 指導教師: 2009 年 畢業(yè)設計是大學階段的最后一個環(huán)節(jié),是對以前所學
2、的知識以及所掌握的技能的綜合運用和檢驗。隨著我國經濟的迅速發(fā)展,采用模具的生產技術得到愈來愈廣泛的應用。完成了大學期間的課程學習、生產實習,我熟練地掌握了機械制圖、機械設計、機械制造、模具設計與制造等基礎課和專業(yè)課方面的知識,對機械制造、加工的工藝有了一個系統(tǒng)、全面的理解,達到了學習的目的。對于模具設計這個實踐性非常強的設計課題,我們進行了大量的實習。經過在鄭州市第二機床廠、鶴壁天海集團等幾家單位的生產實習,我對于模具特別是塑料模具的設計步驟有了一個全新的認識,豐富了在各種模具的結構和動作過程方面的知識,而對于模具的制造工藝更是實現了重大突破。在老師的指導下和在工廠師傅的講解下,同時在現場查閱
3、了很多相關資料并親手拆裝了一些典型的模具實體,明確了模具的一般工作原理、制造、加工工藝,并在圖書館借閱了許多相關手冊和書籍,設計中,將充分利用和查閱各種資料,并與同學進行充分討論,盡最大努力搞好本次畢業(yè)設計。雖然在設計的過程中會有一定的困難,但有指導老師的悉心指導和自己的努力,相信會圓滿地完成畢業(yè)設計任務。由于學生水平有限,而且缺乏經驗,設計中存在不妥之處在所難免,懇請各位老師指正。 2009年 目錄 1、塑件的工藝性分析……………………………………………………………4 1.1、塑件的原材料
4、分析…………………………………………………………4 1.2、 PC樹脂的工藝特點……………………………………………………… 5 1.3、PC樹脂成型時水分控制及成型加工條件之選擇……………………… 5 1.4、料筒清掃……………………………………………………………………6 1.5、塑件的結構和尺寸精度及表面質量分析…………………………………6 1.6、塑件的體積重量估算………………………………………………………7 2、選取標準模架及注射機………………………………………………………7 3、塑件的注射工藝參數的確定…………………………………………………8 4、模具方案論證……………
5、……………………………………………………9 4.1、成型部件的整體布局………………………………………………………9 4.2、型腔排列方式………………………………………………………………9 4.3、澆口形式……………………………………………………………………10 5、型腔數的確定及澆注系統(tǒng)的設計……………………………………………10 5.1、模具結構形式的確定………………………………………………………10 5.2、分型面的選擇………………………………………………………………10 5.3、型腔數的確定………………………………………………………………11 5.4、確定型腔的排列方式…
6、……………………………………………………11 5.5、澆注系統(tǒng)的設計……………………………………………………………11 5.5.1、主流道的設計……………………………………………………………12 5.5.2、分流道的設計……………………………………………………………13 5.5.3、澆口的設計………………………………………………………………14 5.5.4、冷料穴的設計……………………………………………………………14 6、模具工作零件的設計與計算…………………………………………………15 6.1、凹模的結構設計……………………………………………………………15 6.2、型芯的
7、結構設計……………………………………………………………15 6.3、成型零部件工作尺寸的計算………………………………………………15 6.4、成型零部件的強度與剛度的計算…………………………………………16 7、合模導向機構的設計…………………………………………………………19 7.1、導柱結構的技術要求………………………………………………………19 7.2、導向孔的設計………………………………………………………………19 8、推出機構設計…………………………………………………………………19 9、側向分型機構的設計…………………………………………………………20 9.1、斜導
8、柱設計…………………………………………………………………21 9.2、側滑塊與導滑槽的設計……………………………………………………22 9.3、楔緊塊的設計………………………………………………………………22 10、設計總結…………………………………………………………………… 23 11、參考文獻…………………………………………………………………… 24 設計計算書 1、塑件的工藝性分析 1.1、塑件的原材料分析 塑件的材料采用聚碳酸脂
9、,是一種性能優(yōu)良的熱塑性工程塑料,具有突出的抗沖擊能力,耐蠕變和尺寸穩(wěn)定性好,耐熱、吸水率低、無毒、介電性能優(yōu)良,且收縮率很低,一般為0.1%-0.2%。是五大工程塑料中唯一具有良好透明性的產品,也是近年來增長速度最快的通用工程塑料。目前廣泛應用于汽車、電子電氣、建筑、辦公設備、包裝、運動器材、醫(yī)療保健等領域,隨著改性研究的不斷深入,正迅速拓展到航空航天、計算機、光盤等高科技領域。PC之所以有大的市場容量是由于它具有比較全面平衡的性能——優(yōu)良的耐沖擊性、耐熱性、尺寸穩(wěn)定性、透明及自熄性等,因此在電氣、電子、精密機械、汽車、保安、醫(yī)療等領域成為可廣泛使用的工程塑料。在作為飲用水桶和食品容器時,易
10、被溶出而影響人們身體健康,因此要開發(fā)衛(wèi)生級的PC樹脂,用作飲水桶和其它食品容器的生產與使用,國內應用前景非??春谩C有很好的機械特性,但流動特性較差,因此這種材料的注塑過程較困難。在選用何種品質的PC材料時,要以產品的最終期望為基準。如果塑件要求有較高的抗沖擊性,那么就使用低流動率的PC材料;反之,可以使用高流動率的PC材料,這樣可以優(yōu)化注塑過程。PC的最大特征是非晶型透明塑料,成型后的尺寸穩(wěn)定性好,從低溫到高溫均能保持穩(wěn)定的機械強度,它的拉伸與形變特性比較接近金屬材料,存在著明顯的彈性極限。 1.2、PC樹脂的工藝特點: 1)、聚集態(tài)特性屬于無定型非結晶性塑料,無明顯熔點,熔體黏度較高
11、。玻璃化溫度140~150℃,熔融溫度215℃~225℃,成型溫度250℃~320℃。 2)、在正常加工溫度范圍內熱穩(wěn)定性較好,300℃長時停留基本不分解,超過340℃開始分解,粘度受剪切速率影響較小。 3)、流變性接近牛頓性液體,表觀黏度受溫度的影響較大,受剪切速率的影響較小,相對分子質量的增大而增大。PC分子鏈中有苯環(huán),所以分子鏈剛性大。 4)、PC的抗蠕變性好,尺寸穩(wěn)定性好;但內應力不易消除。 5)、PC高溫下遇水易降解,成型時要求水分含量在0.02%以下。 6)、制品易開裂。 1.3、PC樹脂的成型工藝控制在成型加工上,水分控制及成型加工條件之選擇是影響成型品質最重要的兩個
12、因素,茲分述如下: A、水分控制 PC類塑膠即使用遇到非常低之水分亦會產生水解而斷鍵、分子量降低和物性強度降低之現象,因此在成型加工前應嚴格地控制PC樹脂之水分在0.02%以下,以避免成型品的機械強度降低或表面產生氣泡、銀紋等異常外觀。為避免水分所產生異常之情況,聚碳酸脂在加工前,應先經熱風干燥3-5h以上,溫度定為120℃,或者用除濕干燥機來處理水分。 B、原料選擇 為滿足各種成型工藝的需求,PC樹脂有不同熔體流動速率的規(guī)格。通常熔體流動速率介于5-25g/10min都可適用于注塑成型。但是其最佳加工條件因注塑機種類、成型品之形狀以及PC樹脂規(guī)格不同而有相當之差異,應根據實際情況加以調整
13、。 C、注塑機選擇要點 鎖模壓力:以成品投影面積每cm2*0.47-0.48T(或每平方寸*3-5T)機臺大小:成品重量約為注塑機容量的40-60%為最佳,如機臺以PS來表示容量(盎斯)時,需減少10%,始為使用PC之容量,(1盎斯=28.3公克)。螺桿:螺桿長度最少應有15個直徑長,其L/D為20:1最佳,壓縮比宜1.5:1至30:1。螺桿前端之止流閥應采用滑動環(huán)式, 其樹脂流動間隙最少應有3.2mm。噴嘴:尖端開口最少有4.5mm直徑。若成品重量為5.5kg以上,則噴嘴直徑應為9.5mm以上,另外,尖端開口需比澆口直徑少0.5-1mm,且段道愈短愈好,約為5mm。 D、成型條件要點:熔
14、融溫度與模溫:最佳的成型溫度設定與很多因素有關,如注塑機大小,螺桿組態(tài)、模具及成型品的設計和成型周期等。一般而言,為了讓塑料漸漸在熔融,在料管后斷/進料區(qū)設定較低的溫度,而在料管前段設定較高的溫度。但若螺桿設計不當或L/D值過小。逆向式的溫度設定亦可。模溫方面,高模溫可提供較佳的表面外觀,殘留應力也會較小,且對較薄或較長的成型品也較填滿;而低模溫則能縮短成型周期。螺桿回轉速度:在40-70rpm較佳,但需視機臺與螺桿設計而調整。注射壓力:根據制品壁厚程度可采取85-140kg/cm2。背壓:一般設定愈低愈好,便為求進料均勻,建議使用3-14kg/cm2。注射速度:射速度澆口設計有很大關系。使用
15、直接澆口或邊緣澆口時,為防止日暉現象和波流痕現象,則應用較慢這射速,另外,如成品厚度在5mm以上,為避免氣泡或凹陷慢速射出會有幫助。一般而言,射速原則為薄者快,厚者慢。從注塑切換到保壓,保壓要盡量低。以免成型品發(fā)生殘留應力。而殘留應力可用退火方式來解除或減輕,條件是120-130℃約三十分鐘至一小時。 1.4、料筒清掃 1)、在PC樹脂的成型溫度下,加入清洗料(通用級聚苯乙烯或透苯),連續(xù)射出二十至三十次。 2)、將射臺后退,連續(xù)將清洗料空射,直至射出的清洗料開始膨脹起泡。 3)、將料筒溫度重新設定到200至230℃。 4)、繼續(xù)將清洗料空射,直到清料熔膠溫度達到260℃且外表看起來
16、很干凈透明。 1.5、塑件的結構和尺寸精度及表面質量分析: 1.5.1、塑件的結構分析: 該零件的總體形狀為杯狀,結構相對簡單。 1.5.2塑件尺寸精度的分析: 該零件的尺寸精度較低,均沒有公差要求,一般可采用10~12級精度。 由以上的分析可見,該零件的尺寸精度屬中等偏下,對應模具相關零件尺寸的加工可保證。從塑件的壁厚上來看,壁厚1mm,較為均勻。 1.5.3表面質量的分析: 該零件的表面要求無凹坑等缺陷外,表面無其它特別的要求,故比較容易實現。 綜上分析可以看出,注射時在工藝參數控制得較好的情況下,零件的成型要求可以得到保證。 1.5.4塑料件投影面積計算: 通過Pr
17、o-e對塑料件進行投影面積計算,約為:3211.72㎜2 所需鎖模力約為:(0.47~0.48)32.12=150.96~154.18 KN 1.6、塑件的體積重量估算: 計算塑件的重量是為了選用注射機及確定模具型腔數。 通過Pro-e計算得塑件的體積:V=6227.583 ㎜3 計算塑件的質量:公式為W=Vρ 根據設計手冊查得聚碳酸脂的密度為ρ=1.201810-3g/mm3,故塑件的重量為: W=Vρ =6227.5831.201810-3 =7.484g 2、選取標準模架及注射機 標準模架的選用要點: ⑴模架厚
18、度H和注射機的閉合距離L的關系為: Lmin<=H<=Lmax ⑵開模行程與定、動模分開的間距與推出塑件所需行程之間的尺寸關系,設計時需計算確定,在取出塑件時的注射機開模行程應大于取出塑件所需的動、定模分開的距離,而模具推出塑件距離須小于頂出液壓缸的額定頂出行程。 ⑶選用的模架在注射機上的安裝。 ⑷選用模架應符合塑件及其成型工藝的技術要求 查閱《模具設計手冊》,選擇P3型標準模架,尺寸如下: 模板 墊塊 推板 座板 導柱 導套 寬度 長度 厚度 寬度 長度 厚度 寬度 長度 厚度 寬度 長度 厚度 直徑 直徑 315 315 25 56
19、 315 80 199 315 20 400 315 25 32 32 根據注射所需的壓力和塑件的重量以及標準模架厚度情況,可選用的注射機為:XS-ZY-125型注塑成型機,該注塑機的各參數如下表所示: 理論注射量 125 cm3 移模行程 300 mm 螺桿直徑 42mm 最大模具厚度 300 mm 注射壓力 119 Mp 最小模具厚度 200 mm 鎖模力 900 KN 注射時間 1.6 s 拉桿空間 260mm290mm 注射方式 螺桿式 最大成型面積 320 cm2 動、定模固定板尺寸 -- 合模方式 液壓—
20、機械 機器外形尺寸 3.34 m0.75 m 1.55 m 推出方式 中心推出 電動機功率 11.0 kw 3、塑件的注射工藝參數的確定 查閱相關資料,聚碳酸酯的成型工藝參數可作如下選擇,在試模時可根據實際情況作適當的調整。 工藝參數表 干燥條件(溫度/℃)/(時間/h) 120/>4 噴嘴 形式 直通式 溫度/℃ 240~250 料筒溫度/℃ 前段 270~300 中段 —— 后段 260~290 模具溫度/℃ 90~110 注射壓力/MPa 110~140 保壓壓力/MPa 40~50 注射時間/s 0~5 保壓時間/s
21、 20~80 冷卻時間/s 20~50 成型周期/s 50~130 成型收縮率/﹪ 0.5~0.8 4、模具方案論證 4.1、成型部件的整體布局 方案一:模具型芯位于定模一側,杯柄結構內設置活動鑲塊,成型后人工取出; 方案二:模具型芯位于定模一側,動模采用側向分型機構,杯柄結構內不設置活動鑲塊; 方案三:模具型芯位于動模一側,杯柄結構內設置活動鑲塊,成型后人工取出; 方案四:模具型芯位于動模一側,同時采用側向分型機構,杯柄結構內不設置活動鑲塊; 分析對比 方案一的優(yōu)點是成型結構設計較為簡單,但澆注系統(tǒng)布置較困難,流道較長,不利于成型,同時生產率較低,不符
22、合大批量生產的要求。 方案二在澆注系統(tǒng)布置方面與方案一有相同之處,成型困難,同時在分型脫模過程中可能存在無法順利脫模的問題,但生產率較第一種方案有所提高。 方案三的可行性較強,整個模具結構可緊湊布置。當然,它也存在方案一生產率低下的缺點,具備參考價值。 方案四避免了前三種方案的弊端,無論是結構方面,還是成型方面都較為接近塑件的生產要求。 4.2、型腔排列方式 方案一:型腔對稱布置,杯柄置于中間 方案二:型腔不對稱布置 方案三:型腔對稱布置,杯柄置于兩側 分析對比 方案一結構對稱,在注射及脫模時模具受力平衡性強,有利于延長模具使用壽命,同時便于成型零部件的強度及剛度的校核,
23、缺點澆注系統(tǒng)較長,不利于塑件成型。 方案二結構不對稱,致使模具受力不均,會縮短模具使用壽命,同時也導致了熔體充模時,主流道到各塑件最遠端的距離不相等,容易產生成型缺陷。 方案三繼承了方案一的優(yōu)點,同時也達到了澆注系統(tǒng)最短的要求,在此三種可行性方案中,此方案效果最好,可定為最佳方案。 4.3、澆口形式 查閱相關設計手冊,對于聚碳酸酯(PC)可選用的澆口有以下幾種形式。 方案一:直接澆口,又稱主流道型澆口,它屬于非限制性澆口。 方案二:側澆口,國外稱之為標準澆口,側澆口一般開設在分型面上,塑料熔體從內側或外側充填模具型腔,其截面形狀多為矩形,改變澆口的寬度和厚度可以調節(jié)熔體的剪切速率及
24、澆口的凍結時間。 方案三:點澆口,又稱針點澆口或菱形澆口,是一種截面尺寸很小的澆口,俗稱小澆口。 分析對比 方案一的澆口形式具有流動阻力小、流程短及補縮時間長等特點。由于注射壓力直接作用在塑件上,故容易在進料處產生較大的殘余應力而導致塑件翹曲變形。這種形式的澆口截面大,去除澆口較困難,去除后留有較大的澆口痕跡,影響塑件美觀。另外這種形式的澆口只適用于單型腔模具。 方案二的澆口形式加工和修整方便,因此它是應用較廣泛的一種澆口形式,普遍用于中小型塑件的多型腔模具,且對各種塑料的成型適應性均較強。由于澆口截面小,減少了澆注系統(tǒng)塑料的消耗量,同時去除澆口容易,且不留明顯痕跡。但這種澆口成型的塑
25、件往往有熔接痕存在,且注射壓力損失較大,對深型腔塑件排氣不利。 方案三的澆口形式由于前后兩端存在較大的壓力差,可較大程度增加塑料熔體的剪切速率并產生較大的剪切熱,從而導致熔體的表觀粘度下降,流動性增加,有利于型腔的填充,因而對薄壁塑件以及表觀粘度隨剪切速率變化敏感的塑料成型有利。 相比較之下,方案三最具備可行性,可予以采納。 5、型腔數的確定及澆注系統(tǒng)的設計 5.1、模具結構形式的確定 由于塑件外觀質量要求高,尺寸精度要求一般,且裝配精度要求高,因此我們設計的模具要采用多型腔多分型面。根據本塑件的結構,模具將會采用兩個分型面。 5.2、分型面的選擇 選擇分型面時一般應遵循以下幾項
26、原則: 1) 分型面應選在塑件外形最大輪廓處。 2) 便于塑件順利脫模,盡量使塑件開模時留在動模一邊。 3) 保證塑件的精度要求。 4) 滿足塑件的外觀質量要求。 5) 便于模具加工制造。 6) 對成型面積的影響。 7) 對排氣效果的影響。 8) 對側向抽芯的影響。 為了便于模具加工制造,應盡是選擇平直分型面工易于加工的分型面。本題為杯狀塑件,經分析可采用以水杯大口外圓為分型面的分型方式: 另外,由于此塑件有杯柄結構,故要在模具中設置側向分形機構,以塑件的對稱面作為側向分形面。 5.3、型腔數的確定 型腔數的確定有多種方法,本題采用注射機的鎖模力來確定它的數目。單件塑件
27、所需鎖模力約為:150.96~154.18 KN,注射機公稱鎖模力500kN N*(單件所需鎖模力)<=注射機公稱鎖模力 由于本題生產批量較大,故應盡量使型腔數N取最大值,同時考慮到模具的側向分型,應使型腔數N為偶數,綜合以上可確定型腔數N=2 5.4、確定型腔的排列方式 本塑件在注射時采用一模兩件,即模具需要兩個型腔。綜合考慮澆注系統(tǒng)、模具結構的復雜程度等因素,擬采用兩杯柄朝外對稱分布的型腔排列方式。 5.5、澆注系統(tǒng)的設計 澆注系統(tǒng)的設計是模具設計的一個重要環(huán)節(jié),設計合理與否對塑件的性能、尺寸、內外部質量及模具的結構、塑料的利用率等有較大影響。對澆注系統(tǒng)進行設計時,一般應遵循以
28、下基本原則。 (1)了解塑料的成型性能 (2)盡量避免或減少產生熔接痕 (3)有利于型腔中氣體的排出 (4)防止型芯的變形和嵌件的位移 (5)盡量采用較短的流程充滿型腔 (6)流動距離比和流動面積比的校核 5.5.1、主流道的設計 設計要點: a. 主流道的錐角常取2~4,流動性差的塑料可取3~6,流道壁表面粗糙度取Ra0.8um,且加工時應沿流道軸向拋光。 b.主流道始端球面凹坑半徑比注射機噴嘴球半徑大1~2mm;球面凹坑深度3~5mm;主流道始端入口直徑d比注射機噴嘴直徑大0.5~1mm;一般d=2.5~5mm。 c.主流道末端呈圓角過渡,圓角半徑1~3mm。
29、d.主流道長度以小于60mm為佳,最長不宜超過95mm。 e.主流道常開設在可拆卸的主流道襯套上;其材料常用T10A,熱處理淬火后硬度54~58HRC。 根據設計手冊查得XS-Z-60型注射機噴嘴有關尺寸如下: 噴嘴前端孔徑:d0=φ4mm 噴嘴前端球面半徑:R0=12mm 主流道的小端直徑: D=d+(0.5-1)mm=φ4+1=φ5mm 主流道始端球面凹坑半徑: R=12+(1~2)mm=13mm 主流道的半錐角α通常為1~2過大的錐角會產生湍流或渦流,卷入空氣,過小的錐角使凝料脫模困難,還會使充模時熔體的流動阻力過
30、大,此處的錐角選用4。 澆口套形式如圖: 5.5.2、分流道的設計 分流道在設計時應盡量減小在流道內的壓力損失和熱量損失,同時還要考慮減小流道的容積?,F在常用的分流道截面形式有圓形、梯形、U形、半圓形等幾種。圓形截面的 比面積最小,但需開設在分型面的兩側,在制造時一定要注意模板上兩部分形狀對中吻合;梯形及U形截面分流道加工較容易,且熱量損失與壓力損失均不大,為常用的形式;半圓形截面分流道需用球頭銑刀加工,其表面積比梯形和U形截面分流道略大,在設計中也有采用。本次設計可采用圓形截面分流道。 分流道截面尺寸視塑料品種、塑件尺寸、成型工藝條件以及流道的長度等因素來確定。通常圓形截面分
31、流道的直徑在4.8~9.5mm內選取。由于分流道中與模具接觸的外層塑料迅速冷卻,只有內部的熔體流動狀態(tài)比較理想,因此分流道表面粗糙度要求不能太低,一般Ra取1.6um左右,這可增加對外層塑料熔體的流動阻力,使外層塑料冷卻皮固定,形成絕熱層。形式如圖: 實際加工時,用銑床銑出流道后,稍微省一下模,省掉加工紋理就行了。(省模:制造模具的一道很重要的工序,一般配備了專業(yè)的省模女工,即用打磨機,沙紙,油石等打磨工具將模具型腔表面磨光,磨亮,降低型腔表面粗糙度。) 分流道的布置形式 分流道在分型面上的布置與前面所述型腔排列密切相關,有多種不同的布置形式,但應遵循兩方面原則:即一方面排列緊湊、縮
32、小模具板面尺寸;另一方面流程盡量短、鎖模力力求平衡。 本模具的流道布置形式采用平衡式。 5.5.3澆口的設計 模具設計時,澆口的位置及尺寸要求比較嚴格,初步試模后還需進一步修改澆口尺寸,無論采用何種澆口,其開設位置對塑件成型性能及質量影響很大,因此合理選擇澆口的開設位置是提高質量的重要環(huán)節(jié),同時澆口位置的不同還影響模具結構??傊顾芗哂辛己玫男阅芘c外表,一定要認真考慮澆口位置的選擇,通常要考慮以下幾項原則: 1) 盡量縮短流動距離。 2) 澆口應開設在塑件壁厚最大處。 3) 必須盡量減少熔接痕。 4) 應有利于型腔中氣體排出。 5) 考慮分子定向影響。 6) 避免產生噴射
33、和蠕動。 7) 澆口處避免彎曲和受沖擊載荷。 8) 注意對外觀質量的影響。 以下是可選用的澆口形式: A、直接澆口。 B、側澆口。 C、點澆口。 分析以上幾種澆口形式,同時結合塑件具體結構特征,本模具采用點澆口形式較為合適。下圖是一種適用于一模多件的點澆口形式: 5.5.4冷料穴的設計 在完成一次注射循環(huán)的間隔,考慮到注射機噴嘴和主流道入口這一小段熔體因輻射散熱而低于所要求的塑料熔體的溫度,從噴嘴端部到注射機料筒以內約10-25mm的深度有個溫度逐漸升高的區(qū)域,這時才達到正常的塑料熔體溫度。位于這一區(qū)域內的塑料的流動性能及成型性
34、能不佳,如果這里溫度相對較低的冷料進入型腔,便會產生次品。為克服這一現象的影響,用一個井穴將主流道延長以接收冷料,防止冷料進入澆注系統(tǒng)的流道和型腔,把這一用來容納注射間隔所產生的冷料的井穴稱為冷料穴。 冷料穴一般開設在主流道對面的動模板上(也即塑料流動的轉向處),其標稱直徑與主流道大端直徑相同或略大一些,深度約為直徑的1~1.5倍,最終要保證冷料的體積小于冷料穴的體積 6、模具工作零件的設計與計算 構成塑料模具模腔的零件統(tǒng)稱為成型零部件。成型零件工作時,直接與塑料熔體接觸,承受熔體料流的高壓沖刷、脫模摩擦等,因此,成型零件不僅要求有正確的幾何形狀、較高的尺寸精度和較低的表面粗糙度,而且還
35、要求有合理的結構,較高強度、剛度及較好的耐磨性。 6.1、凹模的結構設計 凹模亦稱型腔,是成型塑件外表面的主要零件,按結構不同可分為整體式和組合式兩種結構形式。根據塑件的具體形狀特征,此次設計采用組合式結構。大體結構如下: 6.2、型芯的結構設計 成型塑件內表面的零件稱凸?;蛐托?,主要有主型芯、小型芯、螺紋型芯和螺紋型環(huán)等。按結構主型芯可分為整體式和組合式兩種,此次同樣采用組合式結構。大體結構如下: 6.3、成型零部件工作尺寸的計算 計算成型零部件工作尺寸要考慮的要素: A、塑件的收縮率波動 B、模具成型零件的制造公差 C、模具成型零件的磨損
36、 D、模具安裝配合誤差 型芯徑向尺寸的計算: Lm(52)=[(1+S)LS+XΔ] 0-δz =[(1+0.0065)52+0.6250.3]0-0.12 =52.5260-0.12mm 型腔深度尺寸的計算: Hm(73)=[(1+S)Hs-XΔ]0+δz =[(1+0.0065)73-0.6250.3]0+0.12 =73.2870+0.12mm 型芯高度尺寸的計算: Hm(73)=[(1+S)hs+XΔ] 0-δz =[(1+0.0065)73+0.6250.3] 0-0.12 =73.6620-0.12mm Hm(34)=[(1+S)h
37、s+XΔ] 0-δz =[(1+0.0065)34+0.6250.25]0-0.1 =34.3770-0.1mm 中心距尺寸的計算: Cm(17)=(1+S)Csδz/2 =(1+0.0065)170.07/2 =17.1110.035mm Cm(4)=(1+S)Csδz/2 =(1+0.0065)40.048/2 =4.0260.024mm 6.4、成型零部件的強度與剛度的計算 塑料模具型腔在成型過程中受到熔體的高壓作用,應具有足夠的強度和剛度,否則可能引起變形破壞及撓曲變形。因此應通過強度和剛度計算來確定型腔壁厚,尤其是精度要求較高的或大型的模具型腔,更不能單純地憑經
38、驗來確定型腔側壁和底板厚度。 模具型腔壁厚的計算應以最大壓力為準。理論分析和生產實踐表明,大尺寸模具型腔剛度不夠是主要矛盾,型腔壁厚應以滿足剛度條件為準,而對于小尺寸的模具型腔,在發(fā)生大的彈性變形前,其應力往往超過了模具材料的許用應力,因此強度不夠是主要矛盾,所以,設計型腔壁厚應以滿足強度條件為準。 計算強度、剛度時考慮的要素: ⑴塑件成型過程中不產生溢料,當高壓熔體注入型腔時,模具型腔的某些配合面會產生間隙,間隙過大則出現溢料,查閱相關手冊,得到:聚碳酸酯的允許變形值<=0.06~0.08mm。 ⑵保證塑件的尺寸精度,某些塑件個別部位的尺寸精度比較高,這就要求模具型腔應具有很好的剛性
39、,以保證塑料熔體注入型腔時不產生較大的彈性變形。
⑶保證塑件的順利脫模,如果型腔剛度不足,在熔體高壓作用下型腔會產生過大的彈性變形,當變形量超出塑件的收縮率時,塑件周邊將被型腔緊緊包住而難以脫模,因此型腔的允許彈性變形量應小于塑件壁厚的收縮值,即:[δ] 40、程上常用的近似計算法,以滿足設計上的需要。對于不規(guī)則的型腔,可簡化為規(guī)則型腔進行近似計算。本次的模具型腔可簡化為圓形型腔進行側壁和底板厚度的計算。
組合式圓形型腔側壁可看作是兩端開口、僅受均勻內壓力的厚壁圓筒。當型腔受到熔體高壓作用時,其內半徑增大,在側壁與底板之間產生縱向間隙,間隙過大會導致溢料。
以下幾式中:
P—型腔內單位面積熔體壓力,取119MPa;
μ—型腔材料泊桑比,取0.3;
E—型腔材料拉伸彈性模量,鋼彈性模量取2.06105MPa;
r—型腔內壁半徑,r=35;
[δ]—允許彈性變形量,取0.06mm;
[σ]—抗拉強度,取550MPa;
按剛度條件 41、計算壁厚為:
S>=r[(1-μ+E[δ]/rp)/( E[δ]/rp-μ-1)]0.5-r
>=35[(1-0.3+2.061050.06/35119)/(2.061050.06/35119-0.3-1)]0.5-35
>=17.5mm
按強度條件計算壁厚為:
S>=r[[σ]/( [σ]-2p)]0.5-r
>=35[550/(550-2119)]0.5-35
>=11.9mm
按剛度條件計算底板厚度為:
h>=(0.74pr4/E[δ])1/3
>=(0.74119354/2.061050.06)1/3
>=22.2mm
按強度條件計算底板厚度為:
h>=(1. 42、22pr2/[σ])0.5
>=(1.22119352/550)0.5
>=18.2mm
另外,以下經驗數據可供參考:
圓形型腔內壁直徑(mm)
型腔壁厚(mm)
模套壁厚(mm)
>50~60
10
25
>60~70
11
28
>70~80
12
32
>80~90
13
35
動模支承板厚度可參考下面的經驗數據:
塑件在分型面上的投影面積/cm2
支承板厚度/mm
<5
15
5~10
15-20
10~50
20-25
50~100
25-30
100~200
30-40
>200
>40
7、合模導向機 43、構的設計
7.1、導柱結構的技術要求
①形狀 導柱前端應做成錐臺形或半球形,以使導柱能順利地進入導向孔。由于半球形加工困難,所以導柱前端形式以錐臺形為多。
②材料 導柱應具有硬而耐磨的的表面和堅韌而不易折斷的內芯,因此多采用20鋼或者T8、T10鋼,硬度為54~58HRC。導柱固定部分的表面粗糙度為Ra=0.8μm,導向部分的表面粗糙度為Ra=0.8~0.4μm。
③數量及布置 導柱應合理均勻布置在模具分型面的四周,導柱中心至模具邊緣應有足夠的距離,以保證模具強度(導柱中心到模具邊緣距離通常為導柱直徑的1~1.5倍)。為確保合模時只能按一個方向合模,導柱的布置可采用等直徑導柱不對 44、稱布置或不等直徑導柱對稱布置的方式。
④配合精度 導柱固定端與模板之間一般采用H7/m6或H7/k6的過渡配合,導柱的導向部分通常采用H7/f7或H8/f7。
7.2、導向孔的設計
形狀 為使導柱順利進入導套,導套的前端應倒圓角。導向孔最好做成通孔,以利于排除孔內的空氣。如果模板較厚,導孔必須做成盲孔時,可在盲孔側壁上打一小孔排氣或在導柱的側壁磨出排氣槽。
材料 與導柱相同。
固定形式及配合精度 直導柱用過盈配合嵌入模板,為了增加導套鑲入的牢固性,防止開模時導套被拉出來,可以用止動螺釘緊固。帶頭導套用過渡配合鑲入模板,導套固定部分的粗糙度為Ra 45、=0.8μm,導向部分粗糙度為Ra=0.8~0.4μm。
8、推出機構設計
推出機構一般由推出、復位和導向三大部分組成。
推出機構的設計要求:
①設計推出機構時應盡量使塑件留于動模一側
②塑件在推出過程中不發(fā)生變形或破壞
③被損壞塑件的外觀質量
④合模時應使推出機構正確復位
⑤推出機構應動作可靠
塑件注射成型后,塑件在模內冷卻定型,由于體積收縮,對型芯產生包緊力,當其從模具中推出時,就必須克服因包緊力而產生的摩擦力。對底部無孔的筒、殼類塑件,脫模推出時還要克服大氣壓力。型芯的成型端部,一般均要設計脫模斜度,另外,塑件剛開始脫模時,所需的脫模力最大,其后,推出力的作用僅僅是為了 46、克服推出機構移動的摩擦力。
復位形式的設計
由于塑件形狀特殊,在模具中放置復位桿較困難,故模具采用彈簧復位的形式。
9、側向分型機構的設計
側抽距離:
S=S1+2~3=30~31mm
式中S1---側成型零件位置點與不妨礙塑件軸向推出之極限相關點間的距離。
側向抽拔力的估算:
F=Lhp(μcosα-sinα)
=2157310(0.390.9397-0.3420)
=3842.6N
L---側型芯成型部分的截面平均周長;
h---側型芯成型部分的高度;
p---塑件對側型芯的包緊力,一般情況下模內冷卻的塑 47、件脫模時取p=8~12MPa;
μ---塑料在熱狀態(tài)時對鋼的摩擦系數(查表得:0.39);
α---側型芯的脫模斜度。
斜導柱側向分型抽芯機構結構緊湊,動作可靠,加工制造方便,廣泛應用于抽拔距和抽拔力不太大的場合。其結構要素組成是斜導柱、側滑塊、導滑槽、楔緊塊與側滑塊的定位裝置。
9.1、斜導柱設計
9.1.1、斜導柱的結構與裝配
斜導柱的結構形式如圖所示。材料一般采用T8、T10,也可用20鋼以滲碳處理,要求硬度55~60HRC。斜導柱與模板固定孔間的配合采用H7/m6,與滑塊導滑孔間采用H11/b11的間隙配合,或采用0.5~1mm的雙邊 48、間隙值;當要求滑塊運動滯后于開模運動時,可采用2~3mm的雙邊間隙值。
斜導柱安裝傾角α的取值;當側抽拔方向垂直于開模方向時,12<=α<=25, 這里取20。
9.1.2、斜導柱的截面尺寸
按斜導柱所受最大彎曲應力小于材料的許用應力來計算。
當抽拔方向垂直于開模方向時,彎曲力N計算式如下:
N=F/[cosα(1-2ftgα-f2)]
=3842.6/[0.9397(1-20.150.364-0.0225)]
=4709.6N
式中 F---側抽芯力(N);
f---鋼材之間的摩擦系數,通常取0.15;其余符號同上。
斜導柱有效導滑長度L4的 49、計算公式:
L4=Scosβ/sinα=30/0.342=87.7mm
式中 S---抽芯距(30mm);
β---側滑塊滑出方向與垂直于開模方向的夾角(0)。
針對圓形截面斜導柱直徑:
d=(10NL4/[σ])1/3
=(4709687.7/[σ]) 1/3
≈20mm
式中 [σ]---斜導柱材料的許用應力(MPa);
N---垂直作用在斜導柱上的彎曲力(N)。
9.1.3、斜導柱的 50、長度及完成側抽芯所需要的開模行程H的計算
斜導柱長度的計算公式為:
L=L1+L2+L3+L4+L5= tgα D/2+hcosα+tgαd/2+L4+L5
=0.36425/2+200.9397+0.36420/2+87.7+8
=122.7mm
式中 α---斜導柱軸線與主開模方向的夾角(20);
L5---錐臺長度,可取d/3或8~15mm
完成側抽芯所需的開模行程為:
H=S(ctgαcosβsinβ)=302.747=82.41mm
式中,當側滑塊滑出方向偏向導柱安裝側 51、時,取式中的“+”;當側滑塊的滑出方向偏離導柱安裝側時,式中取“-”;其他符號同上。
9.2、側滑塊與導滑槽的設計
9.2.1、側滑塊的結構形式 側滑塊分整體式與組合式。這里采用整體式結構。
9.2.2、側滑塊的結構尺寸
側滑塊上斜導孔的直徑與傾角應保證能與斜導柱實現H11/b11的間隙配合。
9.2.3、側滑塊的導滑形式
側滑塊的導滑形式設計為如下結構:
導滑槽應有足夠的長度,其與滑塊的滑動配合長度常取滑塊寬度的1.5倍,必要時可適當加長以保證完成側抽后還有2/3的滑塊長度留在導滑槽內。
滑塊與導滑槽配合面的配合精度一般采用H8/f8或H8/f7,其余各對應面間均留 52、0.5~1mm的間隙。
9.2.4、側滑塊與導滑槽的材料及表面處理
滑塊與導滑槽的材料都常用45鋼、T8和T10,滑動部分表面淬火,要求滑塊的導滑面硬度等于或大于40HRC,導滑槽的導滑面硬度常取52~56HRC;另外側滑塊上成型部分表面熱處理硬度大于或等于50HRC?;瑝K與導滑槽的滑動配合面的表面粗糙度Ra<=0.63μm。
9.3、楔緊塊的設計
楔緊塊的作用就是使側滑塊在模具閉合后能精確復位,并鎖緊側滑塊,以承受注射成型時熔體對側型芯的壓力。楔緊塊的楔緊斜面的傾角α’應大于斜導柱的安裝傾角α,一般取α’=α+2~3。楔緊塊楔緊面的熱處理硬度為54~58HRC。
53、
設計總結
以前做設計都是手工完成,此次畢業(yè)設計所牽涉到的圖紙以及設計說明書均通過計算機輔助完成,這首先讓我體會了計算機輔助設計在機械行業(yè)的重要性和實用性。
此次設計是一項系統(tǒng)性的工程,從自主選題到方案規(guī)劃、方案論證、說明書編寫最后到繪制工程圖,后期整理、完善、標準化,每一步都需要我們認真對待,否則很難做到設計的完整、準確、一致。
一套模具作下來,需要完成許許多多個零部件的尺寸及工藝編制,它們的設計順序也需要認真安排,否則就會導致返工的情況。做設計,特別是機械類設計,準備工作很重要,如果準備不足,就會在設計時一旦遇到問題就卡在那里,耽誤整個工作進程 54、。有些同學喜歡“前緊后松”,我覺得這樣做并不好,他只會增加你的懶惰性和對他人的依賴性,長期下去,會使整個人不思進取,失去斗志。
由于在此之前作過幾次課程設計,所以在說明書編寫方面沒有太大問題,只要按部就班,說明書的編寫不會遇到什么麻煩,但在后期整理時,就會用到word等辦公軟件,這也是對我們業(yè)余技能的一次考驗。如果這些軟件用不熟練,會很影響工作進度,特別要注意的是,越到后期,越要做好設計資料的備份工作,一旦資料丟失,那將是毀滅性的災難。
在繪制工程圖的時候,要經常與指導老師進行交流,相比之下,老師在實際生產中還是很有經驗的,有些拿不準的結構性問題要及時向老師交換意見,這樣會使自己的設計更具 55、備可行性。
經過這次畢業(yè)設計,我發(fā)現自己在計算機操作方面還不很熟練,在今后的工作當中需再接再厲,以實現進一步的提高。
最后再次感謝在此次設計中幫助過我的所有同學和老師們,沒有他們的無私付出也不會有今天的結果,我想由衷地說:謝謝你們!
參考文獻
[1]楊占堯主編.塑料注塑模結構與設計.北京:機械工業(yè)出版社,2003.8
[2]程志遠主編.實用注塑模設計手冊. 北京:機械工業(yè)出版社,2000.4
[3]閻亞林主編.塑料模具手冊. 北京:機械工業(yè)出版社,2004.8
[4]黃云清主編.公差配合與測量技術. 北京:機械工業(yè)出版社,2003.7
[5]《中國模具設計大典》 56、
[6]鄧明主編.實用模具設計簡明手冊. 北京:機械工業(yè)出版社,2006.3
[7]劉京華主編.模具識圖與制圖. 北京:化學工業(yè)出版社,2007.3
[8]申開智主編.塑料成型模具.北京:中國輕工業(yè)出版社,2003
[9] 現代模具編委會.塑料成型原理與注塑模設計.北京:國防工業(yè)出版社,1996
[10] 李秦蕊.塑料模具設計.西安:西北工業(yè)大學出版社,1997
[11] 申樹義,高濟主編.塑料模具設計. 北京:機械工業(yè)出版社,2005
[12] 劉小年,劉振魁主編.機械制圖. 北京:高等教育出版社,2000
25
- 溫馨提示:
1: 本站所有資源如無特殊說明,都需要本地電腦安裝OFFICE2007和PDF閱讀器。圖紙軟件為CAD,CAXA,PROE,UG,SolidWorks等.壓縮文件請下載最新的WinRAR軟件解壓。
2: 本站的文檔不包含任何第三方提供的附件圖紙等,如果需要附件,請聯系上傳者。文件的所有權益歸上傳用戶所有。
3.本站RAR壓縮包中若帶圖紙,網頁內容里面會有圖紙預覽,若沒有圖紙預覽就沒有圖紙。
4. 未經權益所有人同意不得將文件中的內容挪作商業(yè)或盈利用途。
5. 裝配圖網僅提供信息存儲空間,僅對用戶上傳內容的表現方式做保護處理,對用戶上傳分享的文檔內容本身不做任何修改或編輯,并不能對任何下載內容負責。
6. 下載文件中如有侵權或不適當內容,請與我們聯系,我們立即糾正。
7. 本站不保證下載資源的準確性、安全性和完整性, 同時也不承擔用戶因使用這些下載資源對自己和他人造成任何形式的傷害或損失。